DE RE METALLICA
+13
PatBig
Verchère
CLOSDELIF
fcrozet
freebird
Pâtre
Paul-Emmanuel
Tourblanche
cd ram
Jeanghis
lionrobe
ratapignata06
Baccardi
17 participants
Page 2 sur 4
Page 2 sur 4 • 1, 2, 3, 4
Les minerais de fer
Aux dernières nouvelles, il nous arriverait de l'Est une nouvelle pratique appliquable aux minerais pauvres et impurs, qui sont de très loin les plus courants !
Il paraît donc nécessaire de détailler un peu ces minerais et leurs impuretés, avant que de vous présenter cette technique innovante...
Le fer étant omniprésent, on ne s'intéresse qu'aux roches qui en contiennent une concentration élevée sous forme exploitable. Par suite de la grande solubilité du fer, elles sont très diversifiées en types et en époques : à chaque plissement de l'écorce terrestre succéda une intense érosion provoquant la mise en mouvement et la sédimentation de grandes masses ferrugineuses. Les premiers gisements ont ainsi plus de 500 millions d'années, et il s'en constitue encore de nos jours...
Au début du XXe siècle la France possédait plus de la moitié des réserves européennes connues, et n'exploitait plus que les minerais des Pyrénées, de l'Ouest et surtout de Lorraine, ces trois régions concentrant 95% des réserves nationales de fer. Mais au début du XIXe presque toutes les régions exploitaient du minerai local, dont la formation s'étalait du silurien (~ 420 Ma, donc un peu plus ancien que nos massifs granitiques) en Maine et Loire et en Calvados, à l'éocène (~ 40 Ma) dans les Pyrénées ; le plus gros volume datant du toarcien (~180 Ma, au jurassique) en Lorraine et Franche-Comté.
La plupart des minerais exploités étant d'origine sédimentaire, ils contiennent diverses impuretés, en quantité variable, mêlées au minerai ou l'enveloppant (gangues). Les minerais très purs, soit parce qu'ils sont restés proches de la roche-mère, soit grâce à une sédimentation très sélective, ne sont pas rarissimes mais tout de même largement minoritaires.
Impuretés
La gangue est argileuse (silicate d'alumine), calcaire (carbonate de calcium), ou silicieuse. Généralement gênante, elle doit être prise en compte dans les opérations.
Les impuretés, que l'on retrouvera dans le métal, sont principalement le soufre, le phosphore, le manganère et le silicium. Quoique parfois utiles ou même indispensables dans des usages particuliers, elles sont souvent malvenues. Voire réhibitoires comme le phosphore, qui a longtemps rendu la plupart des minerais impropres à la fabrication d'acier.
Ou le soufre, cependant principalement apporté par le combustible : si le charbon de bois est plutôt propre, la houille l'est beaucoup moins. Provenant de végétaux accumulés dans des marais, elle est chargée de diverses saletés, en quantités variables selon les gisements.
Minerais
(les teneurs indiquées sont celles des minerais français, et les lieux ne sont que des exemples)
Le minerai de choix est l'hématite, sesquioxyde de fer anhydre Fe²O³, contenant 45 à 62% de Fe et très peu d'impuretés. C'est de l'oxyde de fer quasi-pur, aggloméré en roche généralement rouge par l'effet des pressions telluriques. Les plus fameux gisements se trouvent près de Bilbao en Espagne, et on l'a aussi exploitée en Angleterre, aux USA, en Algérie, au Brésil et aux Indes. Pour la France, dans les Pyrénées, en Normandie et Roussillon.
Une forme cristallisée en lamelles, le fer oligiste, se trouve en zone volcanique (condensation de fumerolles).
La limonite est semblable, mais intimement associée à de l'eau de constitution (qui n'est pas gênante en métallurgie car la chaleur l'évacue dès le début du processus). Couleur rouge brique ou brune.
Le fer oolithique, 2 Fe²O³, 3 H²O, se trouve en petites boules rondes à croûte silicieuse, dans des couches sédimentaires. Avec une concentration en Fe de 24 à 40% et souvent riche en phosphore (jusqu'à 2%), pendant longtemps ce minerai n'était pas utilisable pour une production de qualité. Mais on le trouve facilement un peu partout en France, et surtout en Lorraine où il constitue (constitua ?) une des plus importantes réserves mondiales.
La magnétite, ou oxyde magnétique (Fe³O4) est un minerai très pur, formant des gisements très abondants en Suède, Espagne, Sibérie, Algérie. Il donne d'excellents aciers mais sa réduction exige plus d'énergie que le Fe²O³.
Le carbonate de fer, sidérose ou fer spathique, est généralement assez pur (30 à 54%). Il est exploité en Espagne, en Allemagne, et dans le département de la Manche. Une simple cuisson préalable est nécessaire, pour le transformer en oxyde.
Les sulfures de fer , ou pyrites, doivent d'abord être grillées pour se transformer en oxyde et évacuer un maximum de soufre. Mais il reste toujours un peu de soufre ; par contre, il n'y a pas de phosphore. Elles viennent surtout d'Espagne, mais il se trouve quelques gîtes en France.
Il paraît donc nécessaire de détailler un peu ces minerais et leurs impuretés, avant que de vous présenter cette technique innovante...
Le fer étant omniprésent, on ne s'intéresse qu'aux roches qui en contiennent une concentration élevée sous forme exploitable. Par suite de la grande solubilité du fer, elles sont très diversifiées en types et en époques : à chaque plissement de l'écorce terrestre succéda une intense érosion provoquant la mise en mouvement et la sédimentation de grandes masses ferrugineuses. Les premiers gisements ont ainsi plus de 500 millions d'années, et il s'en constitue encore de nos jours...
Au début du XXe siècle la France possédait plus de la moitié des réserves européennes connues, et n'exploitait plus que les minerais des Pyrénées, de l'Ouest et surtout de Lorraine, ces trois régions concentrant 95% des réserves nationales de fer. Mais au début du XIXe presque toutes les régions exploitaient du minerai local, dont la formation s'étalait du silurien (~ 420 Ma, donc un peu plus ancien que nos massifs granitiques) en Maine et Loire et en Calvados, à l'éocène (~ 40 Ma) dans les Pyrénées ; le plus gros volume datant du toarcien (~180 Ma, au jurassique) en Lorraine et Franche-Comté.
La plupart des minerais exploités étant d'origine sédimentaire, ils contiennent diverses impuretés, en quantité variable, mêlées au minerai ou l'enveloppant (gangues). Les minerais très purs, soit parce qu'ils sont restés proches de la roche-mère, soit grâce à une sédimentation très sélective, ne sont pas rarissimes mais tout de même largement minoritaires.
Impuretés
La gangue est argileuse (silicate d'alumine), calcaire (carbonate de calcium), ou silicieuse. Généralement gênante, elle doit être prise en compte dans les opérations.
Les impuretés, que l'on retrouvera dans le métal, sont principalement le soufre, le phosphore, le manganère et le silicium. Quoique parfois utiles ou même indispensables dans des usages particuliers, elles sont souvent malvenues. Voire réhibitoires comme le phosphore, qui a longtemps rendu la plupart des minerais impropres à la fabrication d'acier.
Ou le soufre, cependant principalement apporté par le combustible : si le charbon de bois est plutôt propre, la houille l'est beaucoup moins. Provenant de végétaux accumulés dans des marais, elle est chargée de diverses saletés, en quantités variables selon les gisements.
Minerais
(les teneurs indiquées sont celles des minerais français, et les lieux ne sont que des exemples)
Le minerai de choix est l'hématite, sesquioxyde de fer anhydre Fe²O³, contenant 45 à 62% de Fe et très peu d'impuretés. C'est de l'oxyde de fer quasi-pur, aggloméré en roche généralement rouge par l'effet des pressions telluriques. Les plus fameux gisements se trouvent près de Bilbao en Espagne, et on l'a aussi exploitée en Angleterre, aux USA, en Algérie, au Brésil et aux Indes. Pour la France, dans les Pyrénées, en Normandie et Roussillon.
Une forme cristallisée en lamelles, le fer oligiste, se trouve en zone volcanique (condensation de fumerolles).
La limonite est semblable, mais intimement associée à de l'eau de constitution (qui n'est pas gênante en métallurgie car la chaleur l'évacue dès le début du processus). Couleur rouge brique ou brune.
Le fer oolithique, 2 Fe²O³, 3 H²O, se trouve en petites boules rondes à croûte silicieuse, dans des couches sédimentaires. Avec une concentration en Fe de 24 à 40% et souvent riche en phosphore (jusqu'à 2%), pendant longtemps ce minerai n'était pas utilisable pour une production de qualité. Mais on le trouve facilement un peu partout en France, et surtout en Lorraine où il constitue (constitua ?) une des plus importantes réserves mondiales.
La magnétite, ou oxyde magnétique (Fe³O4) est un minerai très pur, formant des gisements très abondants en Suède, Espagne, Sibérie, Algérie. Il donne d'excellents aciers mais sa réduction exige plus d'énergie que le Fe²O³.
Le carbonate de fer, sidérose ou fer spathique, est généralement assez pur (30 à 54%). Il est exploité en Espagne, en Allemagne, et dans le département de la Manche. Une simple cuisson préalable est nécessaire, pour le transformer en oxyde.
Les sulfures de fer , ou pyrites, doivent d'abord être grillées pour se transformer en oxyde et évacuer un maximum de soufre. Mais il reste toujours un peu de soufre ; par contre, il n'y a pas de phosphore. Elles viennent surtout d'Espagne, mais il se trouve quelques gîtes en France.
Re: DE RE METALLICA
Pourquoi, mais pourquoi l'ami Verchère rentre-t-il dans tous ces détails? D'abord, parce qu'il aime ça, certes, mais aussi pour vous permettre de mieux profiter de la suite de notre grande aventure
La méthode indirecte — le haut fourneau.
Le bas fourneau, simple à construire et à utiliser, présentait malgré tout quelques inconvénients : les plus primitifs étaient détruits par la récupération de la loupe, tous consumaient une immense quantité de combustible, et on ne pouvait y réduire que des minerais riches en fer (>70 %) pour espérer obtenir un produit final utilisable.
Or, la réduction en bas fourneau, si elle permet d’obtenir du fer très pur lorsqu’elle est bien menée, donnait aussi quelquefois (souvent) de l’acier de différentes nuances, très recherché, et un produit longtemps considéré comme un rebut, la fonte.
La fonte, qui est du fer combiné à un pourcentage en masse de carbone compris entre 2 % et 6 % environ, possède des caractéristiques totalement différentes du fer et de l’acier.
Elle est dure, cassante, ne se travaille bien ni à chaud ni à froid. Par contre, elle peut se couler dans des moules à l’état liquide et en garder fidèlement l’empreinte une fois refroidie.
Une autre qualité intéressante est que son taux de carbone abaisse fortement sa température de fusion (fer 1480°, fonte entre 1135 et 1350° ). Et au-dessus de 1000°, pour gagner 300 ou même 100°, il faut beaucoup d’énergie…
Vers le XIIe siècle a commencé à se développer un nouveau procédé technique, dérivé du bas fourneau, mais qui, grâce à une température interne plus élevée et l’ajout de produits annexes au minerai, permettait d’obtenir non plus du fer, mais de la fonte ; à coup sûr et avec un rendement bien meilleur, tout en acceptant des minerais plus médiocres. On verra alors apparaître les premiers objets coulés dans ce métal.
C’est toutefois vers le XVIe siècle que ce procédé prendra véritablement son essor, lorsqu’auront été développés les procédés d’affinage permettant d’obtenir fer et acier à partir de la fonte.
Méthodologie.
Le haut fourneau est très comparable au bas fourneau en tour dont il dérive. En coupe, il présente deux troncs de cônes opposés : le premier est la cuve, le second l’ouvrage (dont le tronc de cône inversé forme les étalages), et l’endroit où il se rejoignent s’appelle le ventre. Tout en bas se trouve le creuset, qui s’ouvre en deux points sur l’extérieur : par un orifice, bouché pendant l’opération, au point le plus bas, et par un déversoir, au point haut, par-dessus une plaque appelée la dame (de damm, digue en néerlandais).
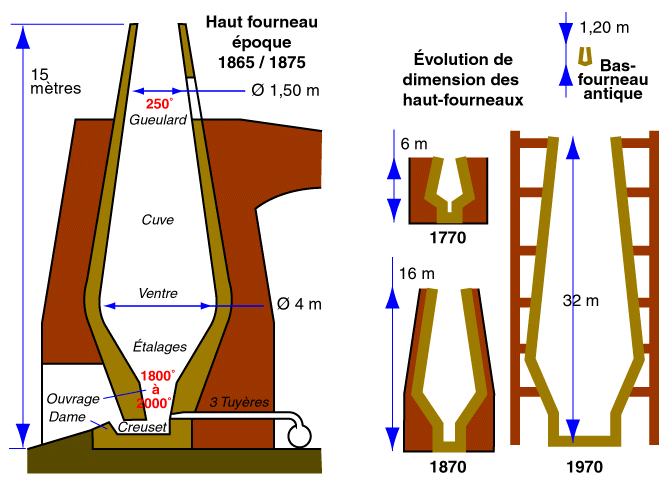
(croquis réalisé par Verchère)
La réduction en haut fourneau est une opération continue : une fois à température de marche, le fourneau va fonctionner sans discontinuer pendant plusieurs mois. On ne l’arrête que pour les périodes de gros travaux agricoles, durant lesquelles la main d’œuvre fait défaut ; on en profite alors pour le réparer et recompléter les stocks de matière.
Quand on arrivera à l’ère industrielle, au XVIIIe, mais surtout au XIXe, le fourneau ne s’arrêtera plus et le personnel sera permanent ; quitte à faire venir une main-d’œuvre étrangère (les paysans locaux ayant longtemps fait passer leur maigre lopin de terre avant l’emploi salarié, et refusant donc obstinément de pointer à l’heure tous les jours et en toutes saisons).
En bas de l’ouvrage règne une fournaise : les tuyères amènent un flot d’air qui consume le charbon, en donnant une chaleur extrême et une grande quantité de gaz carbonique (CO2). En remontant, le flot de gaz carbonique traverse du charbon et, comme nous l’avons vu dans le bas fourneau, se combine avec celui-ci pour donner du monoxyde de carbone (CO2 + C => 2 CO). La chaleur est encore assez intense en approchant du gueulard pour briser la vapeur d’eau présente dans le minerai et donner de l’oxygène et de l’hydrogène. Le monoxyde de carbone et l’hydrogène, tous deux inflammables, forment au gueulard une torchère bleutée caractéristique.
Quand le fourneau est chaud et rempli de combustible (charbon de bois ou coke), on commence à alterner les couches de minerai, de combustible et de fondant par le gueulard.
Le fondant est un élément très important de cette méthode.
Dans un premier temps, le minerai a été préparé, concassé, lavé et grillé. Cette dernière opération a pour but de le débarrasser de toutes les impuretés facilement brûlées, dont le soufre qui donne de très mauvaises caractéristiques au métal.
Mais il reste toujours une bonne quantité de gangue (argile, calcaire ou silice), difficilement fusible et gênant les réactions. D'autant que la silice s'associe avidement au fer nouvellement réduit pour former un silicate de fer irrécupérable ! Cependant, un bon dosage aluminium, calcium et silicium produit un silicate double d'alumine et de calcium, assez fusible pour constituer une scorie liquide absorbant divers éléments indésirables. À cette fin, on ajoute un fondant : pour les minerais siliceux de la castine (calcaire broyé = carbonate de calcium), et parfois pour les minerais calcaires de l'erbue (argile = silicate d'alumine), mais le plus souvent on leur mélange simplement du minerai siliceux, qui est assez commun.
En Bretagne, faute de calcaire on utilisait parfois des coquilles d'huitre en guise de castine. Avec le chauffage au coke, il faut augmenter la proportion de calcium, afin de piéger dans la scorie un maximum du soufre apporté par ce charbon.
Les nouveaux hauts-fourneaux étant d'assez grandes dimensions, il est devenu indispensable que ces fondants soient mélangés à la charge. En réduction directe, l'ajout de castine s'est fait aussi, mais les anciens bas-fourneaux étant plus étroits et à usage unique, un matériau de paroi approprié pouvait apporter un peu du fondant nécessaire ; trop peu, mais on s'en contenta longtemps.
En haut du fourneau, la chaleur encore modérée assèche le minerai et continue le grillage, le débarrassant des impuretés les plus facilement combustibles et commençant à briser la gangue.
Puis, en parcourant la cuve, la chaleur augmente et démarre la réduction des oxydes de fer, sous l’effet de la masse de monoxyde de carbone qui remonte. Le fer est donc produit dans cette zone, mais il reste pâteux et prisonnier de la gangue. Une fois dépassé le ventre, la charge pénètre dans l’ouvrage où la chaleur est telle qu’elle permet la fusion de la gangue qui va se combiner avec le fondant pour former le laitier, composé de silicates (du verre). La gangue liquide coule alors à travers l’ouvrage pour s’amasser dans le creuset, libérant le fer encore pâteux. Celui-ci, mis en présence d’une grande quantité de carbone à une température de plus de 800 °C va se carburer fortement. Cette carburation abaisse son point de fusion et vers 1200 °C, le métal fond et coule rapidement jusqu’au creuset où il va se déposer par gravité sous le laitier. Cette fonte de fer perd une partie de son carbone qui est brûlé au passage devant les tuyères, mais il est protégé par la rapidité de son passage et par la couche de laitier qui le recouvre (et qui représente tout de même 5 à 6 fois le volume de fonte).
Quand le creuset est plein, et avant qu’il ne bouche les tuyères, le laitier passe par dessus la dame et s’écoule au-dehors. Lorsque le niveau de fonte est tel que l’épaisseur de laitier risque de ne plus être suffisant pour empêcher la décarburation, on débouche le trou de coulée situé en bas de la dame, et on procède à un prélèvement de fonte liquide qui coule dans des moules de sable où elle refroidira pour former un bloc massif que les ouvriers qui devaient la manier ensuite à la main appelleront « la gueuse ».
On peut également procéder à la coulée directe dans des moules pour former des pièces en fonte dite « de première coulée », mais ce procédé, aux époques qui nous intéressent, n’a pas d’utilité martiale.
Les gueuses de fonte refroidies seront ensuite affinées pour former du fer, et dans les périodes plus récentes (à partir de la moitié du XIXe siècle) directement de l’acier.
Mais leur principale destination restera longtemps la coulée de pièces en fonte « de seconde fusion » à l’aide d’un cubilot. C’est un troisième type de fourneau à cheminée, comme un petit haut-fourneau quasi cylindrique, chargé en couches alternées de charbon et de fonte. Le mélange métal / combustible permet la fusion avec un rendement énergétique inégalable, et éventuellement un ajustement de la composition du métal (ou un massacre si on rate son coup ; ce qui est facile, car la conduite est instinctive comme dans tous les fourneaux à cheminée). Les hauts fourneaux étaient cantonnés aux régions minières, mais il y eut peu de petites villes ou gros bourgs ne possédant pas de cubilot…

(gravure tirée de Le fer, la fonte et l'acier, M.E.Dreyfus, 1875, libre de droit)
À suivre : quelques notions de résistances des matériaux. (et après, promis, on commencera à affiner tout ça pour produire du métal utilisable...)

La méthode indirecte — le haut fourneau.
Le bas fourneau, simple à construire et à utiliser, présentait malgré tout quelques inconvénients : les plus primitifs étaient détruits par la récupération de la loupe, tous consumaient une immense quantité de combustible, et on ne pouvait y réduire que des minerais riches en fer (>70 %) pour espérer obtenir un produit final utilisable.
Or, la réduction en bas fourneau, si elle permet d’obtenir du fer très pur lorsqu’elle est bien menée, donnait aussi quelquefois (souvent) de l’acier de différentes nuances, très recherché, et un produit longtemps considéré comme un rebut, la fonte.
La fonte, qui est du fer combiné à un pourcentage en masse de carbone compris entre 2 % et 6 % environ, possède des caractéristiques totalement différentes du fer et de l’acier.
Elle est dure, cassante, ne se travaille bien ni à chaud ni à froid. Par contre, elle peut se couler dans des moules à l’état liquide et en garder fidèlement l’empreinte une fois refroidie.
Une autre qualité intéressante est que son taux de carbone abaisse fortement sa température de fusion (fer 1480°, fonte entre 1135 et 1350° ). Et au-dessus de 1000°, pour gagner 300 ou même 100°, il faut beaucoup d’énergie…
Vers le XIIe siècle a commencé à se développer un nouveau procédé technique, dérivé du bas fourneau, mais qui, grâce à une température interne plus élevée et l’ajout de produits annexes au minerai, permettait d’obtenir non plus du fer, mais de la fonte ; à coup sûr et avec un rendement bien meilleur, tout en acceptant des minerais plus médiocres. On verra alors apparaître les premiers objets coulés dans ce métal.
C’est toutefois vers le XVIe siècle que ce procédé prendra véritablement son essor, lorsqu’auront été développés les procédés d’affinage permettant d’obtenir fer et acier à partir de la fonte.
Méthodologie.
Le haut fourneau est très comparable au bas fourneau en tour dont il dérive. En coupe, il présente deux troncs de cônes opposés : le premier est la cuve, le second l’ouvrage (dont le tronc de cône inversé forme les étalages), et l’endroit où il se rejoignent s’appelle le ventre. Tout en bas se trouve le creuset, qui s’ouvre en deux points sur l’extérieur : par un orifice, bouché pendant l’opération, au point le plus bas, et par un déversoir, au point haut, par-dessus une plaque appelée la dame (de damm, digue en néerlandais).
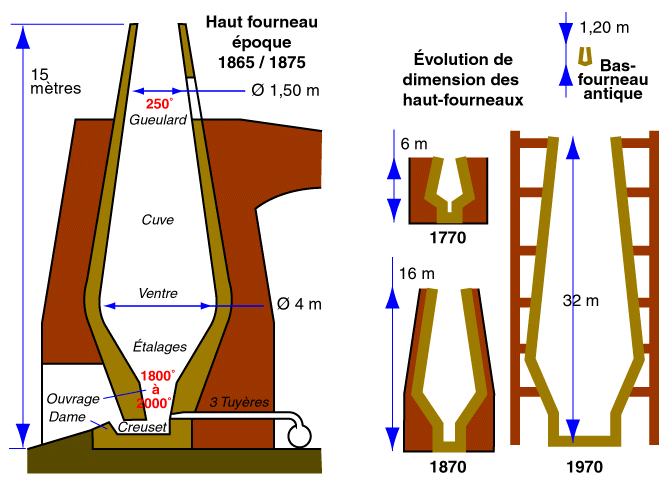
(croquis réalisé par Verchère)
La réduction en haut fourneau est une opération continue : une fois à température de marche, le fourneau va fonctionner sans discontinuer pendant plusieurs mois. On ne l’arrête que pour les périodes de gros travaux agricoles, durant lesquelles la main d’œuvre fait défaut ; on en profite alors pour le réparer et recompléter les stocks de matière.
Quand on arrivera à l’ère industrielle, au XVIIIe, mais surtout au XIXe, le fourneau ne s’arrêtera plus et le personnel sera permanent ; quitte à faire venir une main-d’œuvre étrangère (les paysans locaux ayant longtemps fait passer leur maigre lopin de terre avant l’emploi salarié, et refusant donc obstinément de pointer à l’heure tous les jours et en toutes saisons).
En bas de l’ouvrage règne une fournaise : les tuyères amènent un flot d’air qui consume le charbon, en donnant une chaleur extrême et une grande quantité de gaz carbonique (CO2). En remontant, le flot de gaz carbonique traverse du charbon et, comme nous l’avons vu dans le bas fourneau, se combine avec celui-ci pour donner du monoxyde de carbone (CO2 + C => 2 CO). La chaleur est encore assez intense en approchant du gueulard pour briser la vapeur d’eau présente dans le minerai et donner de l’oxygène et de l’hydrogène. Le monoxyde de carbone et l’hydrogène, tous deux inflammables, forment au gueulard une torchère bleutée caractéristique.
Quand le fourneau est chaud et rempli de combustible (charbon de bois ou coke), on commence à alterner les couches de minerai, de combustible et de fondant par le gueulard.
Le fondant est un élément très important de cette méthode.
Dans un premier temps, le minerai a été préparé, concassé, lavé et grillé. Cette dernière opération a pour but de le débarrasser de toutes les impuretés facilement brûlées, dont le soufre qui donne de très mauvaises caractéristiques au métal.
Mais il reste toujours une bonne quantité de gangue (argile, calcaire ou silice), difficilement fusible et gênant les réactions. D'autant que la silice s'associe avidement au fer nouvellement réduit pour former un silicate de fer irrécupérable ! Cependant, un bon dosage aluminium, calcium et silicium produit un silicate double d'alumine et de calcium, assez fusible pour constituer une scorie liquide absorbant divers éléments indésirables. À cette fin, on ajoute un fondant : pour les minerais siliceux de la castine (calcaire broyé = carbonate de calcium), et parfois pour les minerais calcaires de l'erbue (argile = silicate d'alumine), mais le plus souvent on leur mélange simplement du minerai siliceux, qui est assez commun.
En Bretagne, faute de calcaire on utilisait parfois des coquilles d'huitre en guise de castine. Avec le chauffage au coke, il faut augmenter la proportion de calcium, afin de piéger dans la scorie un maximum du soufre apporté par ce charbon.
Les nouveaux hauts-fourneaux étant d'assez grandes dimensions, il est devenu indispensable que ces fondants soient mélangés à la charge. En réduction directe, l'ajout de castine s'est fait aussi, mais les anciens bas-fourneaux étant plus étroits et à usage unique, un matériau de paroi approprié pouvait apporter un peu du fondant nécessaire ; trop peu, mais on s'en contenta longtemps.
En haut du fourneau, la chaleur encore modérée assèche le minerai et continue le grillage, le débarrassant des impuretés les plus facilement combustibles et commençant à briser la gangue.
Puis, en parcourant la cuve, la chaleur augmente et démarre la réduction des oxydes de fer, sous l’effet de la masse de monoxyde de carbone qui remonte. Le fer est donc produit dans cette zone, mais il reste pâteux et prisonnier de la gangue. Une fois dépassé le ventre, la charge pénètre dans l’ouvrage où la chaleur est telle qu’elle permet la fusion de la gangue qui va se combiner avec le fondant pour former le laitier, composé de silicates (du verre). La gangue liquide coule alors à travers l’ouvrage pour s’amasser dans le creuset, libérant le fer encore pâteux. Celui-ci, mis en présence d’une grande quantité de carbone à une température de plus de 800 °C va se carburer fortement. Cette carburation abaisse son point de fusion et vers 1200 °C, le métal fond et coule rapidement jusqu’au creuset où il va se déposer par gravité sous le laitier. Cette fonte de fer perd une partie de son carbone qui est brûlé au passage devant les tuyères, mais il est protégé par la rapidité de son passage et par la couche de laitier qui le recouvre (et qui représente tout de même 5 à 6 fois le volume de fonte).
Quand le creuset est plein, et avant qu’il ne bouche les tuyères, le laitier passe par dessus la dame et s’écoule au-dehors. Lorsque le niveau de fonte est tel que l’épaisseur de laitier risque de ne plus être suffisant pour empêcher la décarburation, on débouche le trou de coulée situé en bas de la dame, et on procède à un prélèvement de fonte liquide qui coule dans des moules de sable où elle refroidira pour former un bloc massif que les ouvriers qui devaient la manier ensuite à la main appelleront « la gueuse ».
On peut également procéder à la coulée directe dans des moules pour former des pièces en fonte dite « de première coulée », mais ce procédé, aux époques qui nous intéressent, n’a pas d’utilité martiale.
Les gueuses de fonte refroidies seront ensuite affinées pour former du fer, et dans les périodes plus récentes (à partir de la moitié du XIXe siècle) directement de l’acier.
Mais leur principale destination restera longtemps la coulée de pièces en fonte « de seconde fusion » à l’aide d’un cubilot. C’est un troisième type de fourneau à cheminée, comme un petit haut-fourneau quasi cylindrique, chargé en couches alternées de charbon et de fonte. Le mélange métal / combustible permet la fusion avec un rendement énergétique inégalable, et éventuellement un ajustement de la composition du métal (ou un massacre si on rate son coup ; ce qui est facile, car la conduite est instinctive comme dans tous les fourneaux à cheminée). Les hauts fourneaux étaient cantonnés aux régions minières, mais il y eut peu de petites villes ou gros bourgs ne possédant pas de cubilot…

(gravure tirée de Le fer, la fonte et l'acier, M.E.Dreyfus, 1875, libre de droit)
À suivre : quelques notions de résistances des matériaux. (et après, promis, on commencera à affiner tout ça pour produire du métal utilisable...)
freebird- Pilier du forum
- Nombre de messages : 1765
Age : 56
Localisation : Lot 46
Date d'inscription : 28/12/2013
Re: DE RE METALLICA
Je bous d'impatience, je me consume littéralement....mon désir impérieux de connaître la suite est ardent, car je vais enfin savoir comment étaient faits tous ces beaux canons et ces douces Winchester's qui bercent mes rêves les plus récurrents..... 

Non nobis Domine, non nobis, sed Nomini Tuo da Gloriam.
http://winchester-lsg.forumotion.com/
http://prehistoire-xixeme.forumactif.org/
CLOSDELIF- Pilier du forum
- Nombre de messages : 22791
Age : 72
Localisation : 81
Date d'inscription : 03/09/2009
Re: DE RE METALLICA
En tout cas pour publier un beau sujet comme celui-là,,,,il faut le fer.......
Résiste et mords

Paul-Emmanuel- Futur pilier
- Nombre de messages : 965
Age : 60
Localisation : belgique
Date d'inscription : 31/08/2013
Re: DE RE METALLICA
Si je peux ajouter un article dans la marge , je vous présente des forges du St Maurice ,
http://fr.wikipedia.org/wiki/Forges_du_Saint-Maurice
L'établissement d'un haut fourneau en territoire colonial au XVIII e .
http://fr.wikipedia.org/wiki/Forges_du_Saint-Maurice
Une aventure difficile ou une quinzaine d' entreprises se sont relayées de 1730 à 1883 .
On en avait même fait un téléroman... malheureusement pas très réussi , mais on se souviendra
de la musique d'ouverture , composée par André Gagnon
https://www.youtube.com/watch?v=AnFZeJCefTU
https://www.youtube.com/watch?v=lNgJQ5BHHEA
http://fr.wikipedia.org/wiki/Forges_du_Saint-Maurice
L'établissement d'un haut fourneau en territoire colonial au XVIII e .
http://fr.wikipedia.org/wiki/Forges_du_Saint-Maurice
Une aventure difficile ou une quinzaine d' entreprises se sont relayées de 1730 à 1883 .
On en avait même fait un téléroman... malheureusement pas très réussi , mais on se souviendra
de la musique d'ouverture , composée par André Gagnon
https://www.youtube.com/watch?v=AnFZeJCefTU
https://www.youtube.com/watch?v=lNgJQ5BHHEA
Tourblanche- Pilier du forum
- Nombre de messages : 1901
Age : 72
Date d'inscription : 16/03/2011
Re: DE RE METALLICA
Encore une note en marge
Qu' est-ce que le " fer " ?
Aujourd'hui le fer est une espèce en voie de disparition . Ce que nous du XXI e siècle appelons fer est en fait
de l' acier , un alliage contenant une quantité plus ou moins grande de carbone . Au Québec on utilise la nomenclature
de nos voisins du Sud ( AISI/SAE ) et l' acier est identifié par un code de base de quatre chiffres deux donnent le pourcentage de carbone et les deux autres des les additifs à l' alliage , on y reviendra plus tard.
Les artians et les restaurateurs d' artéfacts sont souvent à la recherche de ce " fer" d' autrefois , qui se forgeait si bien .
Ce que nous appelons fer forgé devrait en fait s' appeler acier ouvré .
Le fer d' autrefois avait un " nerf " une fibre comme le bois . On peut le voir sur des articles du XVIII e siècle ,
des clotures , des bittes d' amarrage et des échelles sur les quais , les ancres et leur chaine etc



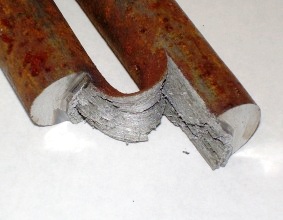
Ça c' est le vrai fer forgé d' avant Bessemer . On imagine le plaisir de travailler une telle matière .... quand on en trouve .
On comprend mieux pourquoi des canons de pistolets à rouet ont été convertis au silex

http://www.littlegun.be/arme%20belge/technique/a%20technique%20damas%20fr.htm
et encore à la percussion
Si l' acier Bessemer ne se forge pas aussi bien , par contre ..... il se coule et se moule !
on verra bientôt l'intéret de la chose

Qu' est-ce que le " fer " ?
Aujourd'hui le fer est une espèce en voie de disparition . Ce que nous du XXI e siècle appelons fer est en fait
de l' acier , un alliage contenant une quantité plus ou moins grande de carbone . Au Québec on utilise la nomenclature
de nos voisins du Sud ( AISI/SAE ) et l' acier est identifié par un code de base de quatre chiffres deux donnent le pourcentage de carbone et les deux autres des les additifs à l' alliage , on y reviendra plus tard.
Les artians et les restaurateurs d' artéfacts sont souvent à la recherche de ce " fer" d' autrefois , qui se forgeait si bien .
Ce que nous appelons fer forgé devrait en fait s' appeler acier ouvré .
Le fer d' autrefois avait un " nerf " une fibre comme le bois . On peut le voir sur des articles du XVIII e siècle ,
des clotures , des bittes d' amarrage et des échelles sur les quais , les ancres et leur chaine etc



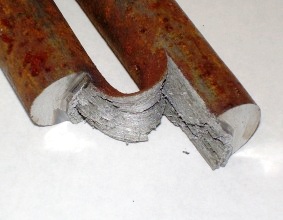
Ça c' est le vrai fer forgé d' avant Bessemer . On imagine le plaisir de travailler une telle matière .... quand on en trouve .
On comprend mieux pourquoi des canons de pistolets à rouet ont été convertis au silex

http://www.littlegun.be/arme%20belge/technique/a%20technique%20damas%20fr.htm
et encore à la percussion
Si l' acier Bessemer ne se forge pas aussi bien , par contre ..... il se coule et se moule !

on verra bientôt l'intéret de la chose


Tourblanche- Pilier du forum
- Nombre de messages : 1901
Age : 72
Date d'inscription : 16/03/2011
Re: DE RE METALLICA
c'est justement pour répondre à toutes ces questions que Verchères et moi avons souhaité démarrer cette série d'articles, pour que nous ayons tous les mêmes infos quand nous discutons du matériau de base de nos armes, que ce soit dans le cadre d'une restauration, ou pour discuter du bien fondé d'un rechargement.
Pour ce qui est du vocabulaire utilisé ici, j'en ai dis quelque mots dès le départ, j'emploie celui de la fin du XIXe siècle, ou l'acier n'est qu'une forme un peu particulière de fer.
Et nous verrons par la suite qu'il existe une grande variété de fer (et d'acier) selon comment il est obtenu à partir des deux méthodes de réduction directe et indirecte.
Et nous découvrirons aussi que la mention "acier fondu" sur une arme n'a rien, mais alors rien à voir avec le fait que la pièce ait été coulée...
Par contre, pour que ça reste abordable mais appuyé sur des sources sérieuses, ça prend un peu de temps à écrire. Pas d'impatience.
Pour ce qui est du vocabulaire utilisé ici, j'en ai dis quelque mots dès le départ, j'emploie celui de la fin du XIXe siècle, ou l'acier n'est qu'une forme un peu particulière de fer.
Et nous verrons par la suite qu'il existe une grande variété de fer (et d'acier) selon comment il est obtenu à partir des deux méthodes de réduction directe et indirecte.
Et nous découvrirons aussi que la mention "acier fondu" sur une arme n'a rien, mais alors rien à voir avec le fait que la pièce ait été coulée...

Par contre, pour que ça reste abordable mais appuyé sur des sources sérieuses, ça prend un peu de temps à écrire. Pas d'impatience.
freebird- Pilier du forum
- Nombre de messages : 1765
Age : 56
Localisation : Lot 46
Date d'inscription : 28/12/2013
Re: DE RE METALLICA
Ah ! Le vocabulaire ... Le "fer" des un n' est pas le fer des autres ... et l' acier " fondu " aussi je suppose ?
( Quand on fait la navette entre le XVII et le XXI e , on utilise les " " en quantités industrielles )
Surtout un mot comme fer , qui a pris une valeur symbolique avec les siècle .
Aujourd'hui un tabouret en acier est moins cher qu'un en bois , Mais jusqu' au XVII e le moindre objet de métal
coutait très cher Toutes les opérations étaient faites à la main , sans autre source d'énergie ( essence , vapeur , électricité )
que la force humaine . C'était la même situation pour les textiles d' ailleurs .

( Quand on fait la navette entre le XVII et le XXI e , on utilise les " " en quantités industrielles )
Surtout un mot comme fer , qui a pris une valeur symbolique avec les siècle .
Aujourd'hui un tabouret en acier est moins cher qu'un en bois , Mais jusqu' au XVII e le moindre objet de métal
coutait très cher Toutes les opérations étaient faites à la main , sans autre source d'énergie ( essence , vapeur , électricité )
que la force humaine . C'était la même situation pour les textiles d' ailleurs .
Tourblanche- Pilier du forum
- Nombre de messages : 1901
Age : 72
Date d'inscription : 16/03/2011
Re: DE RE METALLICA
Depuis la fin du moyen âge, précisons tout de même que de nombreux martinets étaient mûs par la force hydraulique....Tourblanche a écrit:Ah ! Le vocabulaire ... Le "fer" des un n' est pas le fer des autres ... et l' acier " fondu " aussi je suppose ?![]()
( Quand on fait la navette entre le XVII et le XXI e , on utilise les " " en quantités industrielles )
Surtout un mot comme fer , qui a pris une valeur symbolique avec les siècle .
Aujourd'hui un tabouret en acier est moins cher qu'un en bois , Mais jusqu' au XVII e le moindre objet de métal
coutait très cher Toutes les opérations étaient faites à la main , sans autre source d'énergie ( essence , vapeur , électricité )
que la force humaine . C'était la même situation pour les textiles d' ailleurs .

Non nobis Domine, non nobis, sed Nomini Tuo da Gloriam.
http://winchester-lsg.forumotion.com/
http://prehistoire-xixeme.forumactif.org/
CLOSDELIF- Pilier du forum
- Nombre de messages : 22791
Age : 72
Localisation : 81
Date d'inscription : 03/09/2009
Re: DE RE METALLICA
CLOSDELIF a écrit:
Depuis la fin du moyen âge, précisons tout de même que de nombreux martinets étaient mûs par la force hydraulique....

.... Et que l'on s'est toujours aidé de la gravité.
Les process de production du fer ont toujours fonctionné de l'amont vers l'aval, je parle des sites de production ou il y a de la pente bien sûr.
Du minerai, du bois, de la pente et de l'eau, c'était l'idéal

On aura l'occasion d'en reparler

cd ram- Pilier du forum
- Nombre de messages : 1016
Age : 74
Localisation : Isère
Date d'inscription : 10/10/2013
Re: DE RE METALLICA
la différence de vocabulaire entre fer et acier est importante ici si l'on veut se référer aux sources primaires, c'est à dire aux textes d'époques, que ce soit de techniques métallurgiques, ou des règlements d'armements. Quand par exemple, nous verrons, plus tard, que le canon du pistolet 1777 est fait de "bon fer roulé", il sera important d'avoir lu ce qui précède, et ce qui va suivre
(ou que le canon du Chassepot était fait "d'acier puddlé finement laminé au plus près des cotes"...)
Quant à l'acier fondu, il n'y a pour le coup aucune ambiguïté quand on prend la peine de revenir aux sources de la technique. Je réitère donc mon appel à la patience, ça s'écrit, mais le sujet est vaste, donc, ça prend du temps...

Quant à l'acier fondu, il n'y a pour le coup aucune ambiguïté quand on prend la peine de revenir aux sources de la technique. Je réitère donc mon appel à la patience, ça s'écrit, mais le sujet est vaste, donc, ça prend du temps...

freebird- Pilier du forum
- Nombre de messages : 1765
Age : 56
Localisation : Lot 46
Date d'inscription : 28/12/2013
Re: DE RE METALLICA
Allez, vous pensiez que c'était fini (ou qu'on avait jeté l'éponge...
), raté, revoilà la suite des aventures de la métallurgie pour hoplophile.
En attendant de reprendre le cours historique de cette série d'articles, voici venir quelques interventions pédagogiques pas drôle, afin de définir le vocabulaire spécifique à la métallurgie qui sera utilisé par la suite.
Propriété des métaux.
Fusibilité
Capacité à passer à l’état liquide sous l’effet de la chaleur. Caractérisé d’après la température de fusion. Plus cette température est basse, plus le corps est dit fusible.
Fer : 1530°
Acier : 1300° à 1500°
Fontes : 1150° à 1300°
Cuivre : 1080°
Aluminium : 650°
Plomb : 330°
Étain : 235°
Fluidité
Capacité d’un métal à l’état liquide à occuper l’espace dans lequel il est coulé. Plus un métal liquide est chauffé, plus il devient fluide. Certains éléments d’alliage rendent les métaux plus fluides (ex : le silicium et le phosphore pour la fonte)
Malléabilité à chaud
La fusion de la glace, par exemple, est dite brusque parce que ce corps, sous l’action de la chaleur, passe directement de l’état solide à l’état liquide.
La plupart des métaux, au contraire, lorsqu’ils sont chauffés, passent avant de fondre par un état intermédiaire plus ou moins pâteux. Ils pourront donc à chaud subir des déformations plastiques sous l’effet de chocs ou de pression. Ils sont alors dits malléables à chaud.
Malléabilité à froid
Propriété d’un corps de se déformer à froid sous l’action de choc ou de pression. La malléabilité est d’autant plus grande que les chocs ou la pression nécessaires sont faibles.
Lorsque la malléabilité à froid est très grande, les corps sont dits plastiques.
Sous l’effet des déformations à froid, la malléabilité des corps non plastiques diminue sous l’effet de l’écrouissage.
Soudabilité
Propriété qui permet de lier deux corps du même type sous l’action de la chaleur, parfois combiné à des chocs ou une pression.
Ductilité
Propriété permettant à un métal d’être étiré ou tréfilé. Pour cela, le métal doit être à la fois malléable et résistant. (On peut toutefois tréfiler un métal manquant de résistance en le poussant à travers la filière au lieu de le tirer...)
Ténacité
Propriété d’un corps à résister aux efforts de déformation lente (traction, compression, cisaillement, flexion, torsion)
Élasticité
Propriété d’un corps à se déformer sous l’effet d’une force et de revenir à son état initial lorsque l’action de cette force cesse. On parle alors de déformation élastique. Il existe une limite élastique, au delà de laquelle le métal ne reprend plus sa forme initiale (ou casse...)
Dureté
Caractérise la résistance à la pénétration d’un corps par un autre. Elle se mesure par comparaison entre différents matériaux.
La trempe augmente la dureté des aciers, le recuit la diminue. L’écrouissage augmente la dureté de la pièce. (En surface pour les pièces épaisses)
Résilience
La résilience est la résistance opposée par un matériau à un effort brusque ou à un choc.
Elle est mesurée par l’énergie nécessaire à provoquer la rupture d’une pièce.
Trempe et écrouissage diminuent la résilience des métaux.
Le recuit l’augmente.
Je sais, c'est moins drôle que le bas fourneau ou la forge (quand on y arrivera...), mais ces notions seront toutes utiles pour comprendre la suite (voire pour parler de rechargement par exemple, pourquoi recuire les douilles? et est-ce que les plonger dans l'eau les trempe?
La prochaine fois, Verchères nous parlera de RDM

En attendant de reprendre le cours historique de cette série d'articles, voici venir quelques interventions pédagogiques pas drôle, afin de définir le vocabulaire spécifique à la métallurgie qui sera utilisé par la suite.
Propriété des métaux.
Fusibilité
Capacité à passer à l’état liquide sous l’effet de la chaleur. Caractérisé d’après la température de fusion. Plus cette température est basse, plus le corps est dit fusible.
Fer : 1530°
Acier : 1300° à 1500°
Fontes : 1150° à 1300°
Cuivre : 1080°
Aluminium : 650°
Plomb : 330°
Étain : 235°
Fluidité
Capacité d’un métal à l’état liquide à occuper l’espace dans lequel il est coulé. Plus un métal liquide est chauffé, plus il devient fluide. Certains éléments d’alliage rendent les métaux plus fluides (ex : le silicium et le phosphore pour la fonte)
Malléabilité à chaud
La fusion de la glace, par exemple, est dite brusque parce que ce corps, sous l’action de la chaleur, passe directement de l’état solide à l’état liquide.
La plupart des métaux, au contraire, lorsqu’ils sont chauffés, passent avant de fondre par un état intermédiaire plus ou moins pâteux. Ils pourront donc à chaud subir des déformations plastiques sous l’effet de chocs ou de pression. Ils sont alors dits malléables à chaud.
Malléabilité à froid
Propriété d’un corps de se déformer à froid sous l’action de choc ou de pression. La malléabilité est d’autant plus grande que les chocs ou la pression nécessaires sont faibles.
Lorsque la malléabilité à froid est très grande, les corps sont dits plastiques.
Sous l’effet des déformations à froid, la malléabilité des corps non plastiques diminue sous l’effet de l’écrouissage.
Soudabilité
Propriété qui permet de lier deux corps du même type sous l’action de la chaleur, parfois combiné à des chocs ou une pression.
Ductilité
Propriété permettant à un métal d’être étiré ou tréfilé. Pour cela, le métal doit être à la fois malléable et résistant. (On peut toutefois tréfiler un métal manquant de résistance en le poussant à travers la filière au lieu de le tirer...)
Ténacité
Propriété d’un corps à résister aux efforts de déformation lente (traction, compression, cisaillement, flexion, torsion)
Élasticité
Propriété d’un corps à se déformer sous l’effet d’une force et de revenir à son état initial lorsque l’action de cette force cesse. On parle alors de déformation élastique. Il existe une limite élastique, au delà de laquelle le métal ne reprend plus sa forme initiale (ou casse...)
Dureté
Caractérise la résistance à la pénétration d’un corps par un autre. Elle se mesure par comparaison entre différents matériaux.
La trempe augmente la dureté des aciers, le recuit la diminue. L’écrouissage augmente la dureté de la pièce. (En surface pour les pièces épaisses)
Résilience
La résilience est la résistance opposée par un matériau à un effort brusque ou à un choc.
Elle est mesurée par l’énergie nécessaire à provoquer la rupture d’une pièce.
Trempe et écrouissage diminuent la résilience des métaux.
Le recuit l’augmente.
***
Je sais, c'est moins drôle que le bas fourneau ou la forge (quand on y arrivera...), mais ces notions seront toutes utiles pour comprendre la suite (voire pour parler de rechargement par exemple, pourquoi recuire les douilles? et est-ce que les plonger dans l'eau les trempe?

La prochaine fois, Verchères nous parlera de RDM

freebird- Pilier du forum
- Nombre de messages : 1765
Age : 56
Localisation : Lot 46
Date d'inscription : 28/12/2013
Résistance des matériaux (RDM)
On attend d'un métal qu'il résiste aux contraintes d'utilisation. Mais elles sont variées, et celui qui résiste bien à l'une ne sera pas forcément aussi bon vis-à-vis d'une autre...
.
Traction, compression, cisaillement, flexion, choc, chaleur, fatigue... On se limitera ici à une présentation générique du comportement des matériaux face aux contraintes usuellement rencontrées dans les armes à feu : surtout traction et compression.
Choc, chaleur et fatigue aussi, quoique pour ces facteurs plus difficiles à cerner, on se contente souvent d'une appréciation du genre "bon", "pas bon". Alors que flexion et cisaillement se calculent usuellement à partir des caractéristiques de traction - compression.
.
En fait de traction /compression on privilégie la traction, plus facile à étudier ; le comportement en compression est d'ailleurs voisin (compression et flexion ne sont généralement testées que pour fonte, bois et béton ; et cisaillement pour la fonte).
Attention, si les fers et aciers ont des résistances voisines entre traction et compression, c'est un cas particulier. Par exemple, la fonte résiste 6 fois mieux à la compression qu'à la traction ; à l'inverse, le bois en long supporte le double en traction...
LES ESSAIS DE TRACTION portent sur des barreaux de forme spéciale. Ils dessinent une courbe d'allure assez universelle, mais dont les proportions, pentes et détails diffèrent beaucoup selon le métal.
À gauche la courbe typique d'un acier doux, à droite celle d'un acier dur. Verticalement, l'intensité de la force de traction ; horizontalement, l'allongement consécutif à cet effort.
.
OA : d'abord un allongement proportionnel à l'effort, comme un ressort, avec retour à la longueur initiale si l'effort cesse : on est en déformation élastique. La pente de la droite OA dépend du matériau ; plus exactement de E, son module d'élasticité longitudinale ou module de Young (plus il est élevé, plus la droite est verticale, moins le métal s'allonge).
.
AB : avec certains métaux, en particulier l'acier doux, un palier de plasticité marque la fin de la zone élastique. Subitement, sans même augmenter l'effort, le métal s'allonge par à-coups. On sent bien, en pliant à la main un fer ordinaire, qu'à un certain moment " ça part tout seul ", irrégulièrement. Les aciers plus durs ne présentent pas ce palier de plasticité.
.
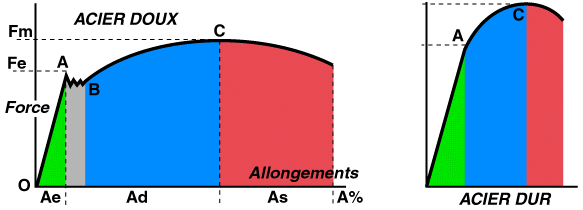
.
À partir du point A les déformations sont permanentes. Il marque donc la limite élastique, et la force Fe nécessaire détermine Re (ou Rp), résistance élastique du matériau.
Devant la difficulté à caractériser une déformation permanente nulle, on se réfère souvent à une déformation très faible, mais quantifiable (0.2 %, voire 0.1 %).
.
BC : sous un effort supérieur, l'allongement continue, mais il n'est plus proportionnel, la courbe s'aplatit progressivement puis commence à redescendre (la déformation se poursuit même si l'effort diminue).
Après C "ça part tout seul", la pièce s'amincit sur une zone de striction, et casse.
.
En C on a atteint la charge de rupture, et la force Fm nécessaire pour y parvenir détermine Rt (ou Rr, ou Rm), résistance de rupture du matériau.
ALLONGEMENT :
Le graphique montre une corrélation entre allongement et effort, l'un permettant de déduire l'autre (sauf durant le palier de plasticité et au moment de la rupture).
On peut ainsi substituer la notion d'allongement-limite à celle d'effort-limite, offrant une approche alternative parfois intéressante (p.ex. étude de l'éclatement des canons).
A (ou A%) est l'allongement avant rupture en valeur relative, caractéristique usuelle des métaux. C'est la somme de 3 allongements successifs : élastique Ae, de déformation Ad et de striction As (les mécanismes travaillent généralement en zone élastique, et Ae_maxi se calcule aisément à partir de la limite élastique et du module de Young).
EFFORTS REPETITIFS (fatigue et écrouissement) :
En dessous du point A, si l'effort diminue et cesse la pièce retrouve ses dimensions originelles en suivant à rebours la ligne OA (fig. 1). Et ceci autant de fois qu'on veut, quoiqu'un très grand nombre d'opérations puisse causer une fatigue du métal, provoquant des ruptures imprévisibles. La fatigue est d'autant plus rapide que l'effort s'approche de la limite élastique, et quasi-nulle s'il ne dépasse jamais la limite de fatigue (valeur impossible à extrapoler de Re ou Rt, l'expérimentation est nécessaire).
.
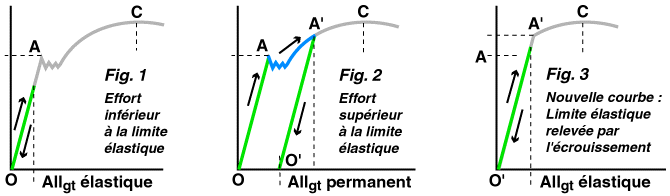
.
Entre A et C, une interruption de l'effort (p. ex. en A') voit la pièce revenir jusqu'en O', suivant un trajet différent (fig. 2) : une ligne droite d'angle déterminé par le module de Young, donc parallèle à la ligne OA. Il subsiste alors une déformation permanente.
En réitérant l'effort (fig. 3) la courbe va monter en ligne droite jusqu'en A', marquant ainsi une nouvelle limite élastique, supérieure à l'ancien point A. La déformation précédente a écroui le métal, augmentant sa résistance élastique (phénomène de déplacement de la limite élastique). C'est tantôt gênant, car le métal devient moins malléable, tantôt positif, car il devient plus résistant (élastiquement parlant, car la charge de rupture ne change pas). On provoque parfois délibérément un écrouissement à la fabrication (martelage des canons en acier, mandrinage des canons en bronze), ou à la maintenance (" battue " du tranchant des faux, pour le durcir localement). Et il se produit à l'usage lorsque le métal est déformé répétitivement (les douilles des cartouches).
Après C, même si l'effort cessait avant rupture la pièce serait à priori perdue, car une striction aurait commencé, altérant la structure du métal.
RESISTANCE AU CHOC (RESILIENCE) :
Un acier dur peut résister à une force progressive importante, et se briser net sous un choc déterminant une force de percussion moindre mais très brève (de l'ordre de 0.01 s). La mesure de cette force étant difficile, on caractérise la résilience par le travail dépensé pour rompre le barreau d'essai.
La montée en pression dans un canon n'est pas assez brutale pour être pleinement considérée comme un choc ; mais... quand même un peu ! Par contre, un brutal rattrapage des jeux dans le mécanisme de culasse relèverait assurément du choc.
LA TEMPERATURE altère la résistance des métaux, qui diminue à chaud. À partir de 500° les aciers perdent toute élasticité et se déforment inexorablement sous la contrainte (fluage).
Par grand froid, au dessous de - 20° à - 30°, c'est la résistance au choc qui diminue.
DURETE BRINELL :
Sous une charge élevée, un petit objet dur (p. ex. une bille d'acier trempé) s'enfonce légèrement dans le métal, et la taille de l'empreinte reflète la dureté superficielle du métal. Des normes fixent pour les divers métaux la taille de la bille, la force et sa durée d'application (pour l'acier, usuellement une bille de Ø 10 mm et 3 tonnes durant 15 s).
Des formules de calcul ou des tables prédéfinies indiquent alors la dureté Brinell (HB) en fonction des dimensions de l'empreinte. On utilise aussi un cône en diamant ou une pointe pyramidale (essais Rockwell et Vickers).
.
Des tables donnent une équivalence approximative entre dureté et charge de rupture, du moins pour l'acier (pour les autres métaux c'est moins net). L'essai de dureté, simple et peu coûteux, ne nécessite pas de barreau calibré comme l'essai de traction. Il peut ainsi s'exécuter sur une pièce finie et donner approximativement sa résistance réelle, alors que l'essai de traction ne donne que celle du métal initial.
D'autant que la pièce testée reste éventuellement utilisable : durant la guerre de 14 et pour pallier à la mauvaise qualité des aciers disponibles, tous les obus de 75 étaient testés à la bille en plusieurs points. Ceci permit de supprimer les éclatements au départ du coup, qui faisaient des ravages.
LES TRAITEMENTS THERMIQUES modifient largement les caractéristiques mécaniques, en les élevant (trempe de l'acier) ou en les abaissant (recuit).
Sauf mention explicite, les essais mécaniques se réfèrent à un métal sans traitement particulier. Les procédés d'élaboration n'étant pas sans conséquences, cet état "normalisé" est codifié ; en général il est plutôt proche de l'état recuit (fortement chauffé pendant un certain temps, et refroidi lentement), c'est à dire doux.
.
Les pièces manufacturées sont inévitablement durcies par un certain écrouissement résultant de la mise en forme et de l'usinage. Des traitements thermiques peuvent éventuellement les adoucir ou les durcir encore plus ; on y viendra plus tard...
LA CHARGE PRATIQUE sera généralement basée sur la résistance élastique, car on attend que la pièce serve plusieurs fois. Mais le métal n'est pas forcément très régulier et les calculs d'effort peuvent être imparfaits, aussi prévoit-on un certain coefficient de sécurité, noté s (ou k).
Les résistances se mesurent en kg / mm² (tout comme le module de Young) ; la résistance élastique Re divisée par le coefficient de sécurité s donne le taux de charge pratique, toujours en kg / mm², qui sera la contrainte maximale admissible en service.
On rencontre certes diverses unités, kgf / mm², hbar (hectobars), dN / mm². Mais elles reviennent au même et ne sont que la manifestation d'acrobaties destinées à satisfaire aux lubies successives des physiciens, sans devoir changer les valeurs numériques inscrites un peu partout (en RDM, la différence entre 9.81 et 10 est négligeable).
.
Traction, compression, cisaillement, flexion, choc, chaleur, fatigue... On se limitera ici à une présentation générique du comportement des matériaux face aux contraintes usuellement rencontrées dans les armes à feu : surtout traction et compression.
Choc, chaleur et fatigue aussi, quoique pour ces facteurs plus difficiles à cerner, on se contente souvent d'une appréciation du genre "bon", "pas bon". Alors que flexion et cisaillement se calculent usuellement à partir des caractéristiques de traction - compression.
.
En fait de traction /compression on privilégie la traction, plus facile à étudier ; le comportement en compression est d'ailleurs voisin (compression et flexion ne sont généralement testées que pour fonte, bois et béton ; et cisaillement pour la fonte).
Attention, si les fers et aciers ont des résistances voisines entre traction et compression, c'est un cas particulier. Par exemple, la fonte résiste 6 fois mieux à la compression qu'à la traction ; à l'inverse, le bois en long supporte le double en traction...
LES ESSAIS DE TRACTION portent sur des barreaux de forme spéciale. Ils dessinent une courbe d'allure assez universelle, mais dont les proportions, pentes et détails diffèrent beaucoup selon le métal.
À gauche la courbe typique d'un acier doux, à droite celle d'un acier dur. Verticalement, l'intensité de la force de traction ; horizontalement, l'allongement consécutif à cet effort.
.
OA : d'abord un allongement proportionnel à l'effort, comme un ressort, avec retour à la longueur initiale si l'effort cesse : on est en déformation élastique. La pente de la droite OA dépend du matériau ; plus exactement de E, son module d'élasticité longitudinale ou module de Young (plus il est élevé, plus la droite est verticale, moins le métal s'allonge).
.
AB : avec certains métaux, en particulier l'acier doux, un palier de plasticité marque la fin de la zone élastique. Subitement, sans même augmenter l'effort, le métal s'allonge par à-coups. On sent bien, en pliant à la main un fer ordinaire, qu'à un certain moment " ça part tout seul ", irrégulièrement. Les aciers plus durs ne présentent pas ce palier de plasticité.
.
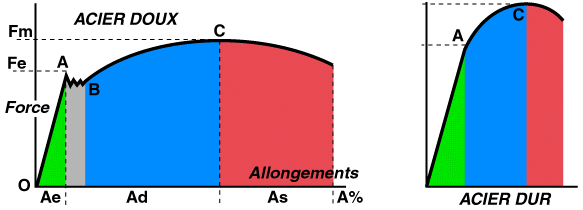
.
À partir du point A les déformations sont permanentes. Il marque donc la limite élastique, et la force Fe nécessaire détermine Re (ou Rp), résistance élastique du matériau.
Devant la difficulté à caractériser une déformation permanente nulle, on se réfère souvent à une déformation très faible, mais quantifiable (0.2 %, voire 0.1 %).
.
BC : sous un effort supérieur, l'allongement continue, mais il n'est plus proportionnel, la courbe s'aplatit progressivement puis commence à redescendre (la déformation se poursuit même si l'effort diminue).
Après C "ça part tout seul", la pièce s'amincit sur une zone de striction, et casse.
.
En C on a atteint la charge de rupture, et la force Fm nécessaire pour y parvenir détermine Rt (ou Rr, ou Rm), résistance de rupture du matériau.
ALLONGEMENT :
Le graphique montre une corrélation entre allongement et effort, l'un permettant de déduire l'autre (sauf durant le palier de plasticité et au moment de la rupture).
On peut ainsi substituer la notion d'allongement-limite à celle d'effort-limite, offrant une approche alternative parfois intéressante (p.ex. étude de l'éclatement des canons).
A (ou A%) est l'allongement avant rupture en valeur relative, caractéristique usuelle des métaux. C'est la somme de 3 allongements successifs : élastique Ae, de déformation Ad et de striction As (les mécanismes travaillent généralement en zone élastique, et Ae_maxi se calcule aisément à partir de la limite élastique et du module de Young).
EFFORTS REPETITIFS (fatigue et écrouissement) :
En dessous du point A, si l'effort diminue et cesse la pièce retrouve ses dimensions originelles en suivant à rebours la ligne OA (fig. 1). Et ceci autant de fois qu'on veut, quoiqu'un très grand nombre d'opérations puisse causer une fatigue du métal, provoquant des ruptures imprévisibles. La fatigue est d'autant plus rapide que l'effort s'approche de la limite élastique, et quasi-nulle s'il ne dépasse jamais la limite de fatigue (valeur impossible à extrapoler de Re ou Rt, l'expérimentation est nécessaire).
.
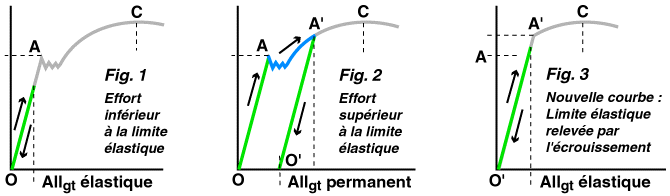
.
Entre A et C, une interruption de l'effort (p. ex. en A') voit la pièce revenir jusqu'en O', suivant un trajet différent (fig. 2) : une ligne droite d'angle déterminé par le module de Young, donc parallèle à la ligne OA. Il subsiste alors une déformation permanente.
En réitérant l'effort (fig. 3) la courbe va monter en ligne droite jusqu'en A', marquant ainsi une nouvelle limite élastique, supérieure à l'ancien point A. La déformation précédente a écroui le métal, augmentant sa résistance élastique (phénomène de déplacement de la limite élastique). C'est tantôt gênant, car le métal devient moins malléable, tantôt positif, car il devient plus résistant (élastiquement parlant, car la charge de rupture ne change pas). On provoque parfois délibérément un écrouissement à la fabrication (martelage des canons en acier, mandrinage des canons en bronze), ou à la maintenance (" battue " du tranchant des faux, pour le durcir localement). Et il se produit à l'usage lorsque le métal est déformé répétitivement (les douilles des cartouches).
Après C, même si l'effort cessait avant rupture la pièce serait à priori perdue, car une striction aurait commencé, altérant la structure du métal.
RESISTANCE AU CHOC (RESILIENCE) :
Un acier dur peut résister à une force progressive importante, et se briser net sous un choc déterminant une force de percussion moindre mais très brève (de l'ordre de 0.01 s). La mesure de cette force étant difficile, on caractérise la résilience par le travail dépensé pour rompre le barreau d'essai.
La montée en pression dans un canon n'est pas assez brutale pour être pleinement considérée comme un choc ; mais... quand même un peu ! Par contre, un brutal rattrapage des jeux dans le mécanisme de culasse relèverait assurément du choc.
LA TEMPERATURE altère la résistance des métaux, qui diminue à chaud. À partir de 500° les aciers perdent toute élasticité et se déforment inexorablement sous la contrainte (fluage).
Par grand froid, au dessous de - 20° à - 30°, c'est la résistance au choc qui diminue.
DURETE BRINELL :
Sous une charge élevée, un petit objet dur (p. ex. une bille d'acier trempé) s'enfonce légèrement dans le métal, et la taille de l'empreinte reflète la dureté superficielle du métal. Des normes fixent pour les divers métaux la taille de la bille, la force et sa durée d'application (pour l'acier, usuellement une bille de Ø 10 mm et 3 tonnes durant 15 s).
Des formules de calcul ou des tables prédéfinies indiquent alors la dureté Brinell (HB) en fonction des dimensions de l'empreinte. On utilise aussi un cône en diamant ou une pointe pyramidale (essais Rockwell et Vickers).
.
Des tables donnent une équivalence approximative entre dureté et charge de rupture, du moins pour l'acier (pour les autres métaux c'est moins net). L'essai de dureté, simple et peu coûteux, ne nécessite pas de barreau calibré comme l'essai de traction. Il peut ainsi s'exécuter sur une pièce finie et donner approximativement sa résistance réelle, alors que l'essai de traction ne donne que celle du métal initial.
D'autant que la pièce testée reste éventuellement utilisable : durant la guerre de 14 et pour pallier à la mauvaise qualité des aciers disponibles, tous les obus de 75 étaient testés à la bille en plusieurs points. Ceci permit de supprimer les éclatements au départ du coup, qui faisaient des ravages.
LES TRAITEMENTS THERMIQUES modifient largement les caractéristiques mécaniques, en les élevant (trempe de l'acier) ou en les abaissant (recuit).
Sauf mention explicite, les essais mécaniques se réfèrent à un métal sans traitement particulier. Les procédés d'élaboration n'étant pas sans conséquences, cet état "normalisé" est codifié ; en général il est plutôt proche de l'état recuit (fortement chauffé pendant un certain temps, et refroidi lentement), c'est à dire doux.
.
Les pièces manufacturées sont inévitablement durcies par un certain écrouissement résultant de la mise en forme et de l'usinage. Des traitements thermiques peuvent éventuellement les adoucir ou les durcir encore plus ; on y viendra plus tard...
LA CHARGE PRATIQUE sera généralement basée sur la résistance élastique, car on attend que la pièce serve plusieurs fois. Mais le métal n'est pas forcément très régulier et les calculs d'effort peuvent être imparfaits, aussi prévoit-on un certain coefficient de sécurité, noté s (ou k).
Les résistances se mesurent en kg / mm² (tout comme le module de Young) ; la résistance élastique Re divisée par le coefficient de sécurité s donne le taux de charge pratique, toujours en kg / mm², qui sera la contrainte maximale admissible en service.
On rencontre certes diverses unités, kgf / mm², hbar (hectobars), dN / mm². Mais elles reviennent au même et ne sont que la manifestation d'acrobaties destinées à satisfaire aux lubies successives des physiciens, sans devoir changer les valeurs numériques inscrites un peu partout (en RDM, la différence entre 9.81 et 10 est négligeable).
Aciers et métaux à canons
Les caractéristiques mécaniques usuelles sont la charge de rupture et la dureté HB (sur les documents récents), qui ne sont pourtant pas les plus utiles pour calculer un mécanisme...
La limite élastique, le module de Young et l'allongement à la rupture demandent parfois un peu plus de recherche ; quant à la limite de fatigue et la résilience, c'est parfois difficile à trouver !
Ci-dessous, un tableau APPROXIMATIF.
D'une part, à taux de carbone égal, les valeurs diffèrent un peu d'un document à l'autre. C'est à la rigueur imputable à l'amélioration des appareils de test, et à l'évolution des normes.
D'autre part les "dénominations modernes" sont approximatives, avec des teneurs en carbone variables. À moins qu'elles n'aient évolué avec le temps, ce qui nécessiterait d'en dresser l'évolution chronologique (car dans les documents anciens, les aciers sont rarement spécifiés par leur taux de carbone, mais plus souvent par l'appréciation "dur", "demi-dur", etc.)
Enfin, les "dénominations antiques" sont évasives, et furent souvent plus compliquées, avec des qualificatifs ("fer fort"), et surtout des provenances ("fer fort de Triffouilli les Oies"). Provenances pas forcément hors de propos, car elles caractérisaient minerai, combustible et mode opératoire, et donc le type et la proportion des impuretés. Lesquelles pouvaient altérer ou au contraire améliorer les qualités du métal ; à une époque où la composition des métaux était mal connue, on pouvait difficilement faire mieux.
Ce tableau concerne les métaux à l'état "normal", c'est à dire "doux" ou "recuit".
.
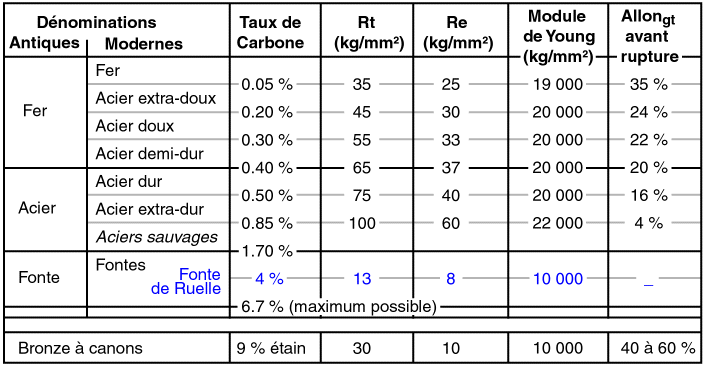
.
On constate que le module de Young diffère très peu entre l'acier doux et dur, ce qui signifie que sous un faible effort (inférieur à Re) l'acier dur ne se montrera pas plus rigide. Par contre la fonte et le bronze s'allongeront 2 fois plus (une fois dépassé Re la fonte cassera d'ailleurs très vite, alors que le bronze s'allongera beaucoup, mais alors en déformation permanente).
Les Aciers Sauvages correspondent à une plage imprécise (entre 0.85 % à 1.2 % en limite basse, et 1.7 % à 2 % en limite haute). Aciers à priori ultra-durs, mais réputés inutilisables, car trop difficiles à maîtriser. Cependant, certaines traditions métallurgiques y parvenaient, semble-t-il...
La Fonte de Ruelle est un exemple : caractéristiques citées en 1909 pour la fonte auparavant utilisée à Ruelle (canons de Marine).
Le Bronze à Canons n'a pas une composition très stricte. Elle peut monter à 10 % d'étain, voire 11 %, sans grandes modifications des propriétés.
Les métaux modernes les plus usuels :
À l'évidence ce sont les boulons ; avec une classe de résistance souvent poinçonnée dessus (deux nombres séparés d'un point). Le premier, à multiplier par 10, indique la charge de rupture minimale ; le second donne la limite élastique en % de cette charge de rupture.
Par exemple, classe 6.8 : rupture 60 kg/mm², limite élastique 80 % de 60 kg = 48 kg/mm².
Ou 8.8 : rupture 80 kg, élasticité 80 x 0.8 = 64 kg/mm², voire 10.9 (100 kg / 90 kg).
Notons qu'à partir de la classe 8.8 la boulonnerie est généralement traitée thermiquement.
La limite élastique, le module de Young et l'allongement à la rupture demandent parfois un peu plus de recherche ; quant à la limite de fatigue et la résilience, c'est parfois difficile à trouver !
Ci-dessous, un tableau APPROXIMATIF.
D'une part, à taux de carbone égal, les valeurs diffèrent un peu d'un document à l'autre. C'est à la rigueur imputable à l'amélioration des appareils de test, et à l'évolution des normes.
D'autre part les "dénominations modernes" sont approximatives, avec des teneurs en carbone variables. À moins qu'elles n'aient évolué avec le temps, ce qui nécessiterait d'en dresser l'évolution chronologique (car dans les documents anciens, les aciers sont rarement spécifiés par leur taux de carbone, mais plus souvent par l'appréciation "dur", "demi-dur", etc.)
Enfin, les "dénominations antiques" sont évasives, et furent souvent plus compliquées, avec des qualificatifs ("fer fort"), et surtout des provenances ("fer fort de Triffouilli les Oies"). Provenances pas forcément hors de propos, car elles caractérisaient minerai, combustible et mode opératoire, et donc le type et la proportion des impuretés. Lesquelles pouvaient altérer ou au contraire améliorer les qualités du métal ; à une époque où la composition des métaux était mal connue, on pouvait difficilement faire mieux.
Ce tableau concerne les métaux à l'état "normal", c'est à dire "doux" ou "recuit".
.
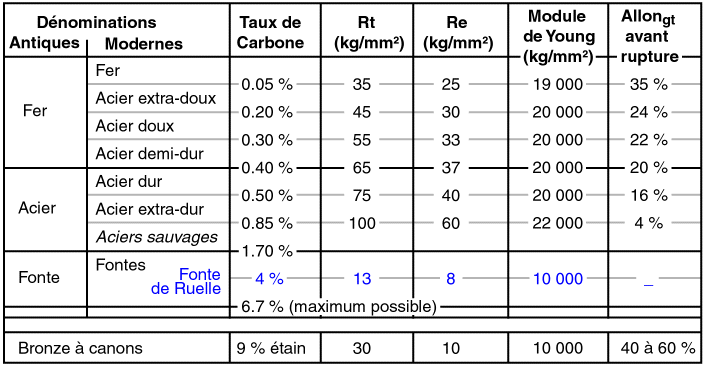
.
On constate que le module de Young diffère très peu entre l'acier doux et dur, ce qui signifie que sous un faible effort (inférieur à Re) l'acier dur ne se montrera pas plus rigide. Par contre la fonte et le bronze s'allongeront 2 fois plus (une fois dépassé Re la fonte cassera d'ailleurs très vite, alors que le bronze s'allongera beaucoup, mais alors en déformation permanente).
Les Aciers Sauvages correspondent à une plage imprécise (entre 0.85 % à 1.2 % en limite basse, et 1.7 % à 2 % en limite haute). Aciers à priori ultra-durs, mais réputés inutilisables, car trop difficiles à maîtriser. Cependant, certaines traditions métallurgiques y parvenaient, semble-t-il...
La Fonte de Ruelle est un exemple : caractéristiques citées en 1909 pour la fonte auparavant utilisée à Ruelle (canons de Marine).
Le Bronze à Canons n'a pas une composition très stricte. Elle peut monter à 10 % d'étain, voire 11 %, sans grandes modifications des propriétés.
Les métaux modernes les plus usuels :
À l'évidence ce sont les boulons ; avec une classe de résistance souvent poinçonnée dessus (deux nombres séparés d'un point). Le premier, à multiplier par 10, indique la charge de rupture minimale ; le second donne la limite élastique en % de cette charge de rupture.
Par exemple, classe 6.8 : rupture 60 kg/mm², limite élastique 80 % de 60 kg = 48 kg/mm².
Ou 8.8 : rupture 80 kg, élasticité 80 x 0.8 = 64 kg/mm², voire 10.9 (100 kg / 90 kg).
Notons qu'à partir de la classe 8.8 la boulonnerie est généralement traitée thermiquement.
De la loupe au fer.
Allez, poursuivons notre œuvre métallurgique, et reprenons l'aventure historique de la fabrication du fer pendant que Verchère rassemble ses forces pour nous instruire sur les traitements thermiques et l'influence du taux de carbone sur les caractéristiques de l'acier...
De la loupe au fer.
À la sortie du bas fourneau (voir épisodes précédents), on obtient une éponge de fer, la loupe. Le métal pâteux s’est plus ou moins aggloméré, et est mêlé de résidus de charbon et de scorie.
Profitant de la chaleur résiduelle de la loupe, celle-ci est cinglée, c’est à dire battue sans brutalité pour resserrer les particules de fer et expulser les impuretés. Jusqu’au XVIe siècle, cette première opération se fera à la main à l’aide de masse de bois dur afin d’éviter de pulvériser l’éponge de fer, encore très hétérogène.
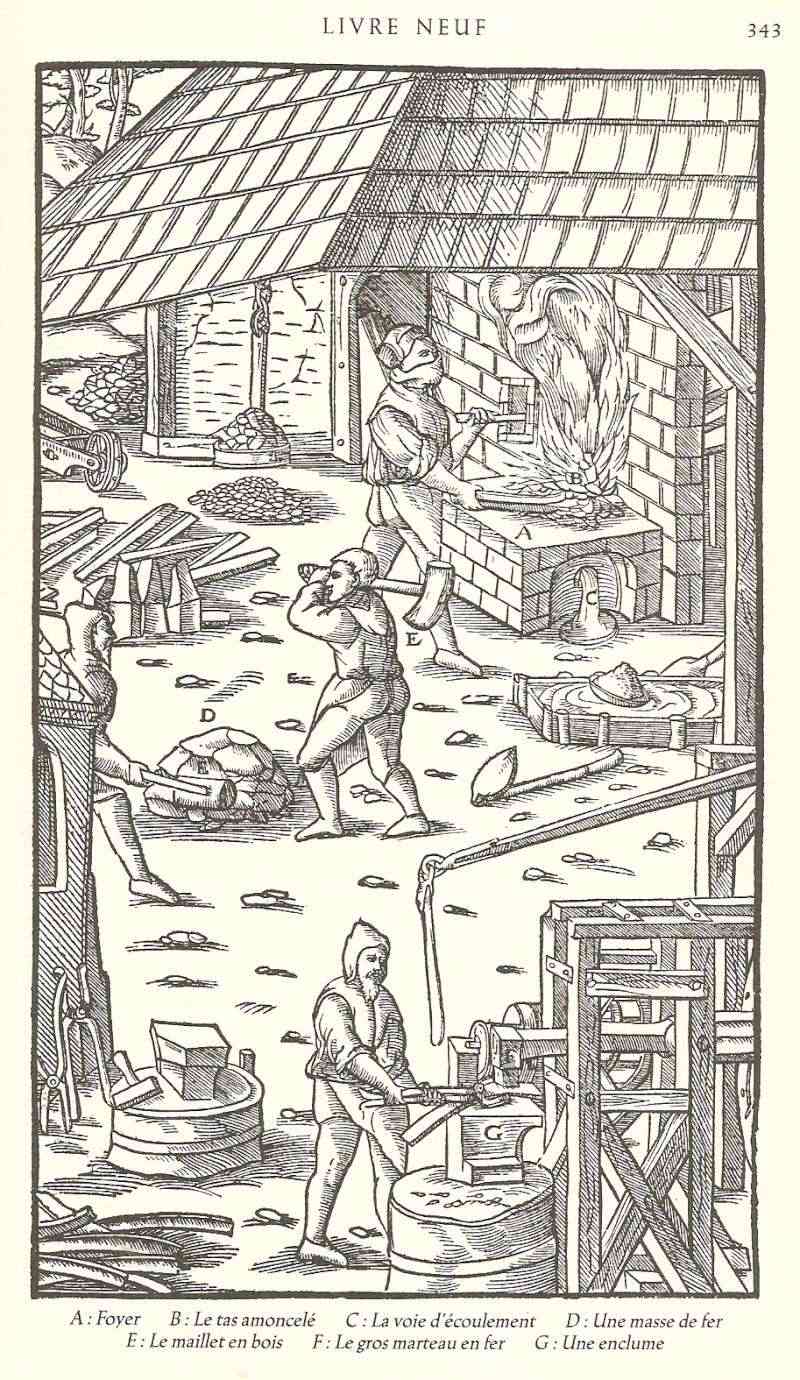
De Re Metallica, Agricola, XVIe
Une fois compactée, la masse va devoir être soudée et homogénéisée, ce qui est accompli par plusieurs chaudes dans un bas foyer (à l’origine, vraisemblablement le creuset du bas fourneau lui-même, puis dans un feu spécifique, jusqu’à la forge catalane, dernier bas fourneau historique, qui associera à nouveau fourneau de réduction et foyer d’affinage).
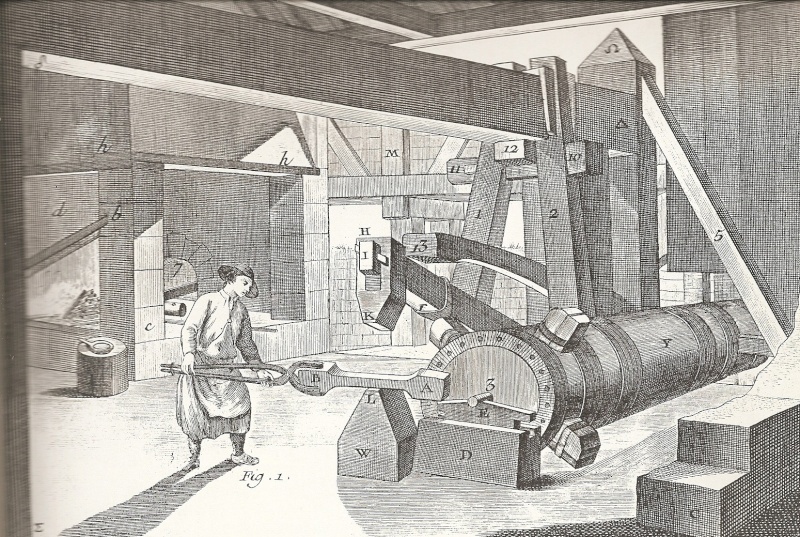
Encyclopédie Diderot et d'Alembert, XVIIIe
La masse est portée à la température dite du « rouge-blanc », plus communément appelée blanc soudant ou blanc suant, et martelée à nouveau pour en souder toutes les parties. Les scories, liquides à cette température, sont expulsées par les chocs.
Ces opérations se faisaient à la main tant que les bas fourneaux donnaient des loupes de quelques kilogrammes à quelques dizaines de kilogrammes, mais on passera au Moyen-Âge à l’utilisation de la force hydraulique pour animer des martinets, marteaux géants qui permettront de traiter des loupes de plus grandes tailles.
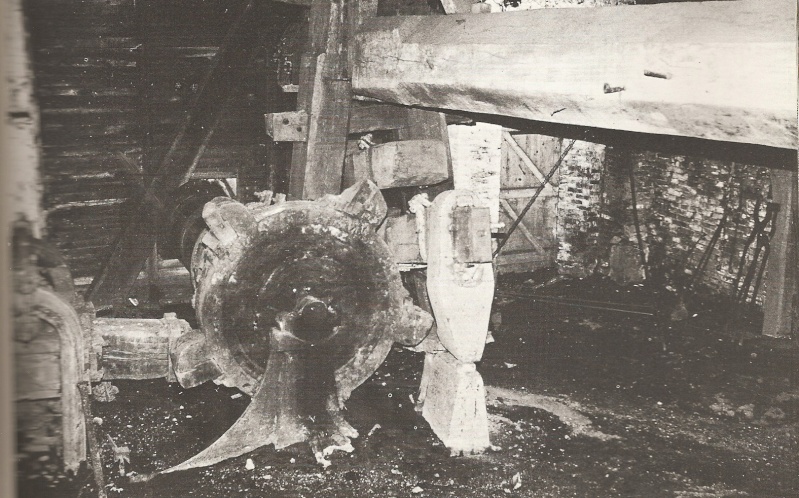
La grande forge, C. Sütterlin
Cette réorganisation des forges sonnera le glas des exploitations « artisanales », au plus près du minerai, et donnera les bases de la sidérurgie. Toutefois, elles s’implanteront principalement dans des zones riches à la fois en minerai, en bois et en eaux vives, car, nous l’avons déjà vu, il vaut mieux transporter le fer fini, à forte valeur ajoutée, que des tombereaux de minerai ou de combustible.
La loupe compactée est découpée en portions qui sont ensuite battues, étirées, repliées et soudées à chaud pour rendre le métal aussi homogène que possible. Toutefois, il reste toujours une proportion non négligeable de scories présentes, ce qui explique la structure fibreuse de ce matériau communément appelé « fer forgé »* (wrought iron) et que l’on désigne de nos jours sous le vocable « vieux fer ».
Le fer forgé possède un taux de carbone très faible, une structure fibreuse, assez semblable au fil du bois, des inclusions de scories (silice), et se travaille à haute température (plus de 1100°). Il se soude très facilement à lui même à chaud, et cette opération bien réalisée forme un ensemble homogène (ou, plus précisément, la soudure ne forme pas une ligne plus hétérogène que le reste de la matière...)
Il supporte mal d’être travaillé « au rouge » et tend dans ce cas à se séparer en fibres et à perdre sa cohésion. Par contre, il se travaille bien à froid, au marteau, et le travail des armures en particulier se réalise de cette manière. Le martelage à froid a tendance à resserrer les fibres du fer et à le durcir par écrouissage, propriétés qui sera utilisée pour réaliser les premiers outils tranchants en fer, métal par ailleurs particulièrement mou et ductile. Les pièces ainsi écrouies peuvent retrouver leur structure d’origine par une chauffe au rouge et un refroidissement lent : le recuit.
(*Le vocable fer forgé ne devrait normalement désigner que le matériau ainsi obtenu par étirage, repliage et soudure répétée. Au fil du temps, il en est venu à désigner tout objet d’acier doux plus ou moins martelé à chaud, ce qui est une impropriété)
Pour les photos, je vous laisse remonter au post de Tourblanche qui nous avait trouvé de belles illustrations de fer forgé.
Du fer à l’acier
Toutefois, si la théorie veut que la réduction directe donne du fer, la pratique enseigne que le métal réduit, mis en présence de carbone à une température avoisinant 800° à 1000°, va absorber une partie de ce carbone et se transformer en acier. C’est le principe de la carburation. (De manière inverse, l’acier chauffé au rouge et soumis à un courant d’air va subir une perte de carbone, qui se combine à l’oxygène, comme vu précédemment. On a alors une décarburation. Ces deux principes sont très importants dans la genèse de l’acier par affinage)
La présence de carbone dans le fer donne à celui-ci des caractéristiques totalement différentes et autorise une gamme de traitement thermique beaucoup plus étendue.
La loupe cinglée et battue présente donc en plus de sa structure fibreuse, une présence hétérogène de carbone : il existe dans la masse des endroits plus ou moins carburés.
Pour en tirer profit, le forgeron étire le métal en barre, appelées verges, qu’il chauffe ensuite au rouge cerise clair avant de le refroidir brutalement. La barre prend donc une trempe aléatoire, selon le degré de carburation de ses différentes parties. On la brise alors à froid et on peut trier le métal par l’aspect de sa cassure (le grain) et sa dureté. Selon le produit recherché, on peut ensuite agglomérer par soudure les parties semblables, ce qui donnera du fer (non trempable) et des aciers hétérogènes de différentes nuances.
Comme on obtient malgré tout beaucoup plus de fer que d’acier convenablement carburé, celui-ci restera longtemps très cher et utilisé avec parcimonie (sans parler de l’aura mystique entourant la « magie » de sa transformation).
Pendant très longtemps, la majorité des outils tranchants seront réalisés en fer, par ailleurs beaucoup plus facile à travailler, seul le tranchant étant aciéré par la soudure d’une mise d’acier qui seule prenait la trempe.

Hache de fer forgé à mise d'acier rapportée, collection personnelle
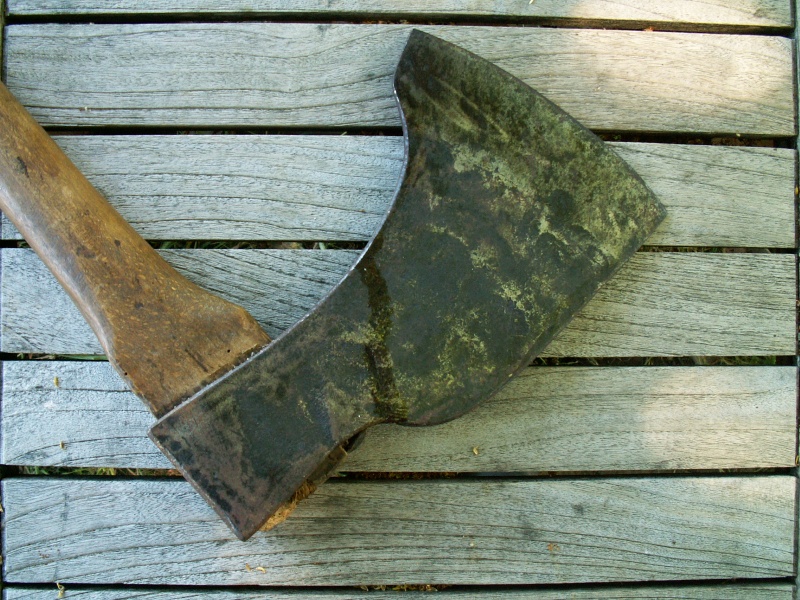
Hache de fer forgé à mise d'acier rapportée, collection personnelle
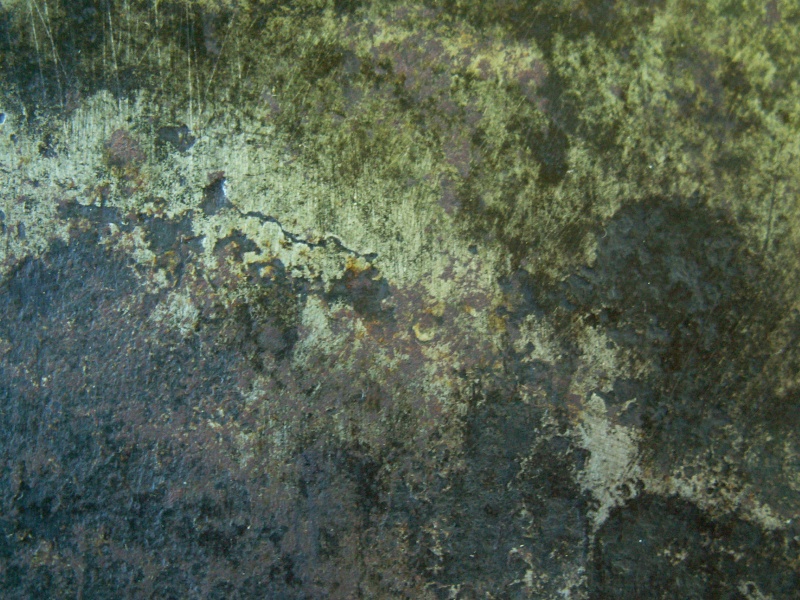
Détail, différence de texture entre les deux zones et ligne de soudure

Hache de fer forgé à mise d'acier rapportée, collection personnelle

Détail
Par le biais de l’observation, les forgerons apprendront à maîtriser le processus de réduction pour obtenir « à volonté » une plus ou moins grande quantité d’acier (et à éviter l’apparition de fonte, qui pendant longtemps, en occident, est restée un rebut.)
Ils apprendront aussi assez vite à aciérer le fer par une chauffe longue dans du charbon. Le carbone diffuse lentement dans le métal chauffé au rouge et protégé de l’oxygène, créant une carburation plus élevée en périphérie de la pièce que dans le cœur. Ce procédé donne des qualités intéressantes pour certaines applications, puisqu’il permet d’obtenir une pièce dure à l’extérieur, résistante, tout en conservant une bonne solidité globale au choc et à l’étirement, la résilience.
C’est à partir de ce procédé que sera élaborée la cémentation. Ce sera, du moins en occident, la principale source d’acier de qualité jusqu’au XVIIIe siècle (et l’invention de l’acier fondu en 1760, mais ceci est une autre histoire). La cémentation consiste à carburer à chaud des pièces finies ou du fer en lingot en le mettant en présence d’un cément, un corps comportant du carbone et des nitrates (le charbon est un cément, mais ce n’est pas le plus efficace. On retrouve là d’autres sources de mystères, avec les secrets de forgeron quant à la composition desdits céments : corne broyée, cendre d’os, charbon de bois...)
L’acier corroyé.
Des barres de fer sont enfermées dans une caisse étanche au milieu d’une grande quantité de cément et mises à chauffer au rouge dans un fourneau pendant plusieurs heures. Comme vu précédemment, le fer chauffé vers 800-900° est avide de carbone qui migre lentement dans le métal et transforme celui-ci en acier. Toutefois, l’extérieur de la barre reste plus carburé que le centre, le matériau reste donc hétérogène. Il convient pour répartir le carbone de manière plus régulière dans la masse de procéder à une autre opération. Les barres sont donc étirées et soudées entre elles pour améliorer l’homogénéité du matériau, en réalisant une sorte de mille-feuilles d’acier. (Cette méthode se retrouve appliquée également dans la réalisation des aciers feuilletés japonais et dans le « Damas »). Cet acier corroyé est dit à une marque. Si la barre obtenue est repliée et ressoudée une seconde fois, ce qui améliore encore la régularité de l’acier, elle est dite à deux marques. C’est ce matériau qui sert de base à la fabrication des outils taillants, et en particulier des armes blanches. Certaines régions, par la qualité de leur minerai, auront longtemps une excellente réputation et fourniront l’ensemble du territoire en métal pour la fabrication des couteaux et des épées (dont les lames ne sont pas en fer aciéré par une mise d’acier rapportée mais en acier corroyé.) C’est également en acier corroyé que seront longtemps faits les ressorts.
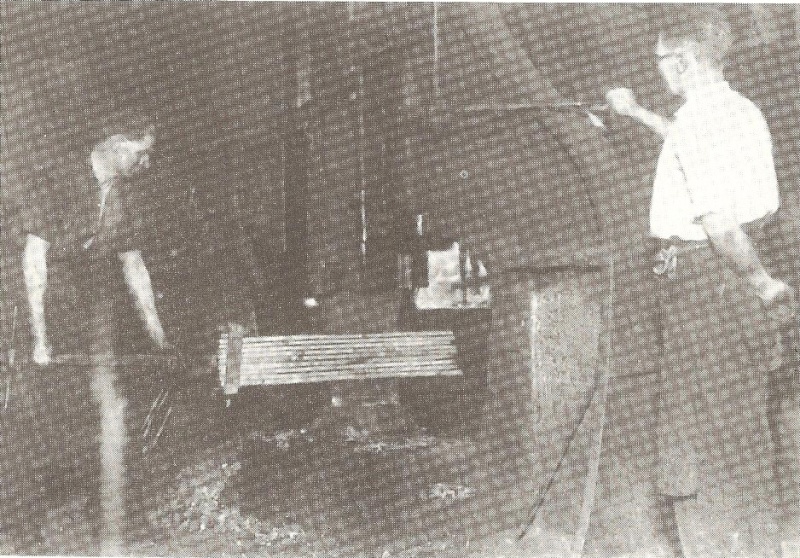
Ironworking, de W.K.V.Gale, shire edition
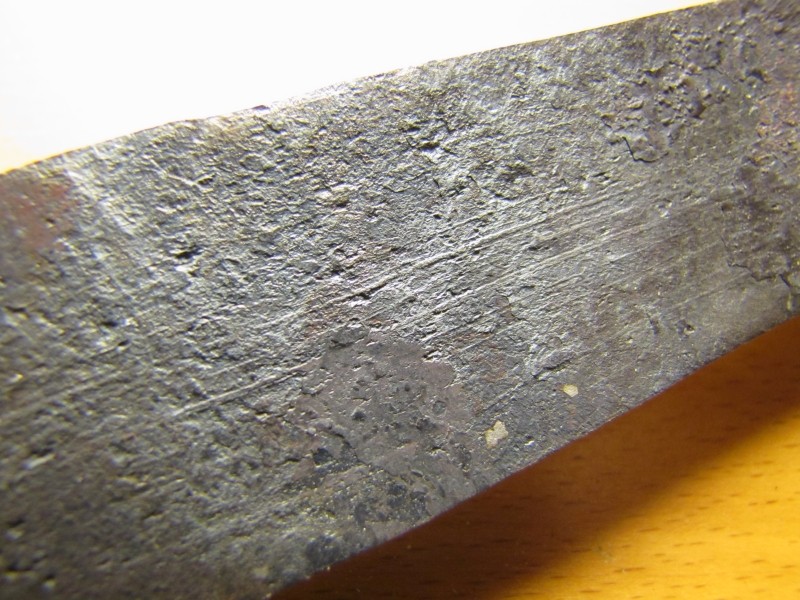
shear steel, de BladesmithForum.
Pour s’y retrouver dans les sources anglo-saxonnes, l’acier cémenté se nomme « blister steel », à cause des marques d’oxydation laissées à la surface du métal par la chauffe prolongée (c’est l’acier poule en France). Une fois corroyé, il prend le nom de « shear steel » (acier à ciseaux)
La cémentation des pièces finies
Il peut être intéressant de former une pièce en fer, qui se travaille aisément au marteau, et de l’aciérer ensuite pour lui donner une plus grande dureté de surface. Nous avons vu que pour les outils taillants, on soudait une mise d’acier sur le corps de fer. Très vite, on va utiliser la cémentation pour aciérer des pièces finies et non plus fabriquer de l’acier comme matière première. Dans le domaine qui nous intéresse, c’est en particulier le procédé qui sera utilisé pour fabriquer les chiens des armes à silex et à percussion, ainsi que les batteries des platines à silex (dans ce dernier cas, il est également possible de réaliser une mise rapportée en acier soudé).
Les pièces sont chauffées dans la même boîte à cémentation au milieu de la poudre à perlimpimpin locale et trempées en sortie de chauffe, ce qu’on appelle trempe en paquet. Le résultat, outre le durcissement de surface recherché, qui permet par exemple de faire des étincelles (batterie), ou de tenir un cran d’armé solide (chien) est une coloration par oxydation hétérogène de la surface, le jaspage.
Toutefois, s’agissant de pièces massives et non plus de fines barres, le durcissement potentiellement obtenu reste superficiel. Si le procédé convient parfaitement à un chien de révolver par exemple, dont les crans d’armé et demi-armé doivent résister à l’usure tout en permettant à la pièce de résister à des chocs répétés, on comprendra aisément qu’une alme de couteau ne pourrait être durable, le premier affilage ayant raison de la couche trempée et exposant le cœur resté doux.
De la loupe au fer.
À la sortie du bas fourneau (voir épisodes précédents), on obtient une éponge de fer, la loupe. Le métal pâteux s’est plus ou moins aggloméré, et est mêlé de résidus de charbon et de scorie.
Profitant de la chaleur résiduelle de la loupe, celle-ci est cinglée, c’est à dire battue sans brutalité pour resserrer les particules de fer et expulser les impuretés. Jusqu’au XVIe siècle, cette première opération se fera à la main à l’aide de masse de bois dur afin d’éviter de pulvériser l’éponge de fer, encore très hétérogène.
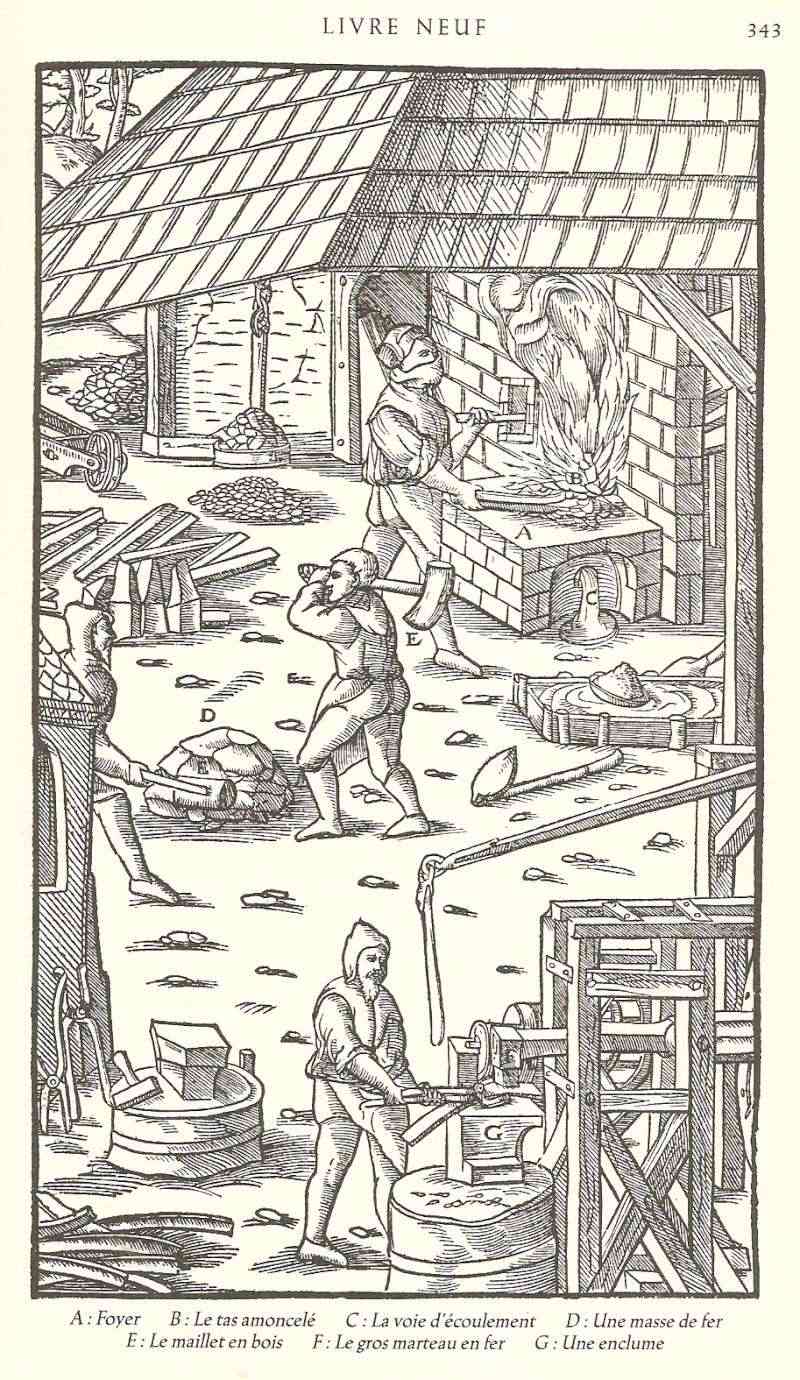
De Re Metallica, Agricola, XVIe
Une fois compactée, la masse va devoir être soudée et homogénéisée, ce qui est accompli par plusieurs chaudes dans un bas foyer (à l’origine, vraisemblablement le creuset du bas fourneau lui-même, puis dans un feu spécifique, jusqu’à la forge catalane, dernier bas fourneau historique, qui associera à nouveau fourneau de réduction et foyer d’affinage).
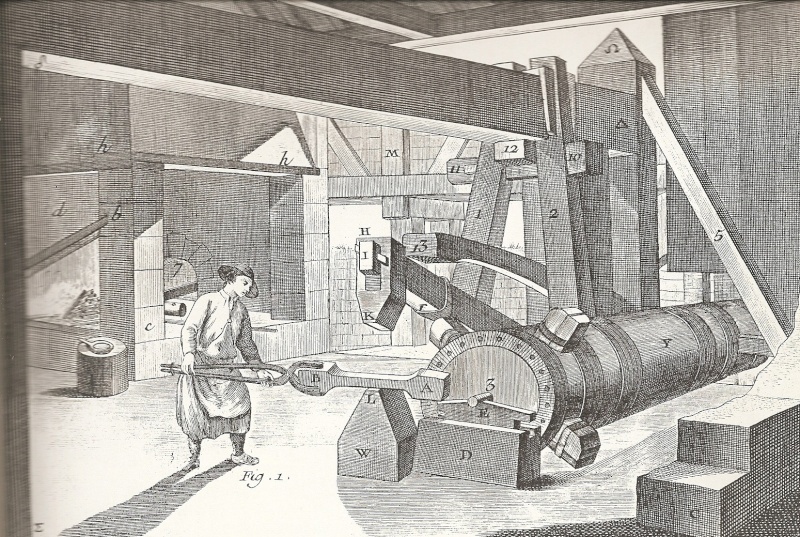
Encyclopédie Diderot et d'Alembert, XVIIIe
La masse est portée à la température dite du « rouge-blanc », plus communément appelée blanc soudant ou blanc suant, et martelée à nouveau pour en souder toutes les parties. Les scories, liquides à cette température, sont expulsées par les chocs.
Ces opérations se faisaient à la main tant que les bas fourneaux donnaient des loupes de quelques kilogrammes à quelques dizaines de kilogrammes, mais on passera au Moyen-Âge à l’utilisation de la force hydraulique pour animer des martinets, marteaux géants qui permettront de traiter des loupes de plus grandes tailles.
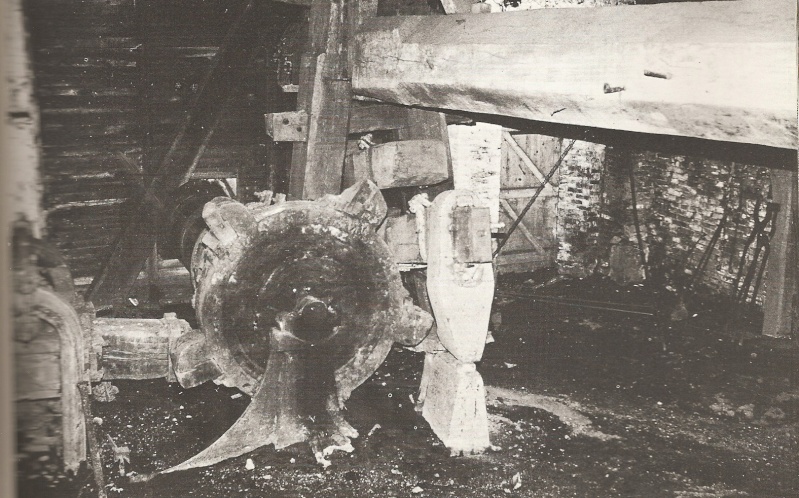
La grande forge, C. Sütterlin
Cette réorganisation des forges sonnera le glas des exploitations « artisanales », au plus près du minerai, et donnera les bases de la sidérurgie. Toutefois, elles s’implanteront principalement dans des zones riches à la fois en minerai, en bois et en eaux vives, car, nous l’avons déjà vu, il vaut mieux transporter le fer fini, à forte valeur ajoutée, que des tombereaux de minerai ou de combustible.
La loupe compactée est découpée en portions qui sont ensuite battues, étirées, repliées et soudées à chaud pour rendre le métal aussi homogène que possible. Toutefois, il reste toujours une proportion non négligeable de scories présentes, ce qui explique la structure fibreuse de ce matériau communément appelé « fer forgé »* (wrought iron) et que l’on désigne de nos jours sous le vocable « vieux fer ».
Le fer forgé possède un taux de carbone très faible, une structure fibreuse, assez semblable au fil du bois, des inclusions de scories (silice), et se travaille à haute température (plus de 1100°). Il se soude très facilement à lui même à chaud, et cette opération bien réalisée forme un ensemble homogène (ou, plus précisément, la soudure ne forme pas une ligne plus hétérogène que le reste de la matière...)
Il supporte mal d’être travaillé « au rouge » et tend dans ce cas à se séparer en fibres et à perdre sa cohésion. Par contre, il se travaille bien à froid, au marteau, et le travail des armures en particulier se réalise de cette manière. Le martelage à froid a tendance à resserrer les fibres du fer et à le durcir par écrouissage, propriétés qui sera utilisée pour réaliser les premiers outils tranchants en fer, métal par ailleurs particulièrement mou et ductile. Les pièces ainsi écrouies peuvent retrouver leur structure d’origine par une chauffe au rouge et un refroidissement lent : le recuit.
(*Le vocable fer forgé ne devrait normalement désigner que le matériau ainsi obtenu par étirage, repliage et soudure répétée. Au fil du temps, il en est venu à désigner tout objet d’acier doux plus ou moins martelé à chaud, ce qui est une impropriété)
Pour les photos, je vous laisse remonter au post de Tourblanche qui nous avait trouvé de belles illustrations de fer forgé.
Du fer à l’acier
Toutefois, si la théorie veut que la réduction directe donne du fer, la pratique enseigne que le métal réduit, mis en présence de carbone à une température avoisinant 800° à 1000°, va absorber une partie de ce carbone et se transformer en acier. C’est le principe de la carburation. (De manière inverse, l’acier chauffé au rouge et soumis à un courant d’air va subir une perte de carbone, qui se combine à l’oxygène, comme vu précédemment. On a alors une décarburation. Ces deux principes sont très importants dans la genèse de l’acier par affinage)
La présence de carbone dans le fer donne à celui-ci des caractéristiques totalement différentes et autorise une gamme de traitement thermique beaucoup plus étendue.
La loupe cinglée et battue présente donc en plus de sa structure fibreuse, une présence hétérogène de carbone : il existe dans la masse des endroits plus ou moins carburés.
Pour en tirer profit, le forgeron étire le métal en barre, appelées verges, qu’il chauffe ensuite au rouge cerise clair avant de le refroidir brutalement. La barre prend donc une trempe aléatoire, selon le degré de carburation de ses différentes parties. On la brise alors à froid et on peut trier le métal par l’aspect de sa cassure (le grain) et sa dureté. Selon le produit recherché, on peut ensuite agglomérer par soudure les parties semblables, ce qui donnera du fer (non trempable) et des aciers hétérogènes de différentes nuances.
Comme on obtient malgré tout beaucoup plus de fer que d’acier convenablement carburé, celui-ci restera longtemps très cher et utilisé avec parcimonie (sans parler de l’aura mystique entourant la « magie » de sa transformation).
Pendant très longtemps, la majorité des outils tranchants seront réalisés en fer, par ailleurs beaucoup plus facile à travailler, seul le tranchant étant aciéré par la soudure d’une mise d’acier qui seule prenait la trempe.

Hache de fer forgé à mise d'acier rapportée, collection personnelle
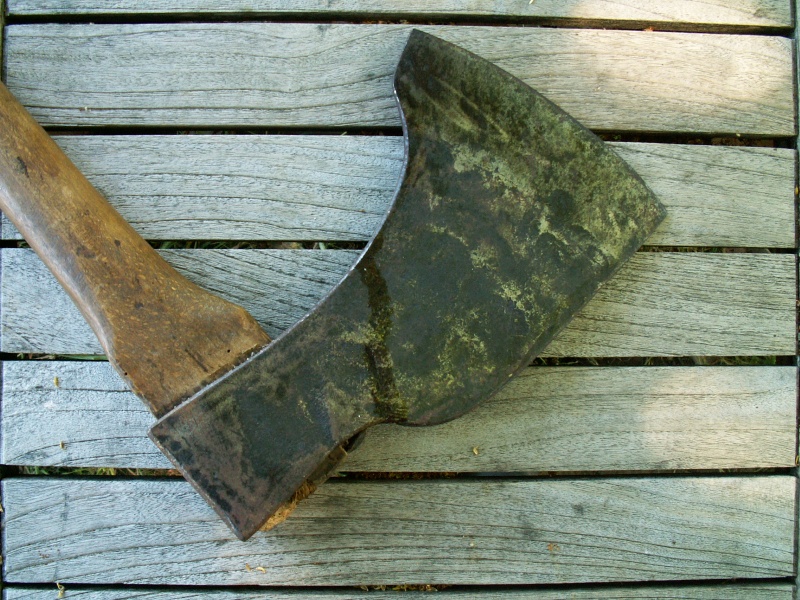
Hache de fer forgé à mise d'acier rapportée, collection personnelle
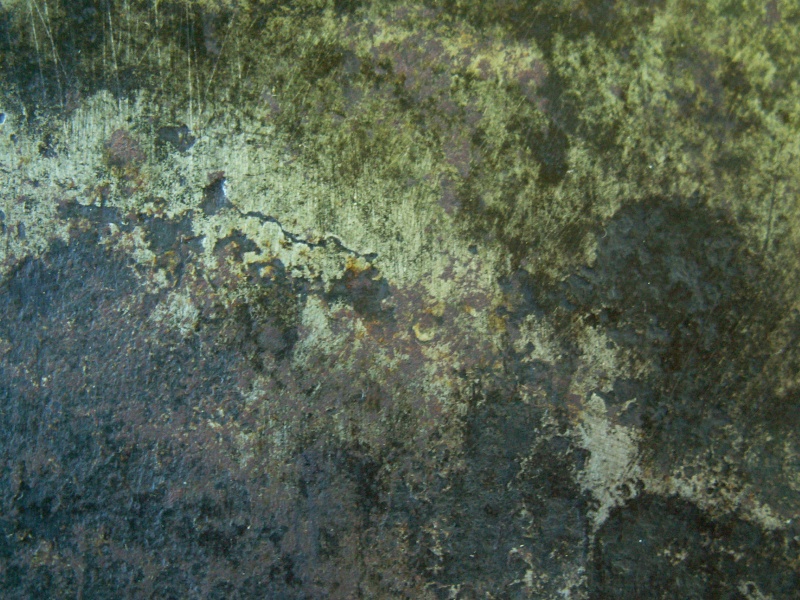
Détail, différence de texture entre les deux zones et ligne de soudure

Hache de fer forgé à mise d'acier rapportée, collection personnelle

Détail
Par le biais de l’observation, les forgerons apprendront à maîtriser le processus de réduction pour obtenir « à volonté » une plus ou moins grande quantité d’acier (et à éviter l’apparition de fonte, qui pendant longtemps, en occident, est restée un rebut.)
Ils apprendront aussi assez vite à aciérer le fer par une chauffe longue dans du charbon. Le carbone diffuse lentement dans le métal chauffé au rouge et protégé de l’oxygène, créant une carburation plus élevée en périphérie de la pièce que dans le cœur. Ce procédé donne des qualités intéressantes pour certaines applications, puisqu’il permet d’obtenir une pièce dure à l’extérieur, résistante, tout en conservant une bonne solidité globale au choc et à l’étirement, la résilience.
C’est à partir de ce procédé que sera élaborée la cémentation. Ce sera, du moins en occident, la principale source d’acier de qualité jusqu’au XVIIIe siècle (et l’invention de l’acier fondu en 1760, mais ceci est une autre histoire). La cémentation consiste à carburer à chaud des pièces finies ou du fer en lingot en le mettant en présence d’un cément, un corps comportant du carbone et des nitrates (le charbon est un cément, mais ce n’est pas le plus efficace. On retrouve là d’autres sources de mystères, avec les secrets de forgeron quant à la composition desdits céments : corne broyée, cendre d’os, charbon de bois...)
L’acier corroyé.
Des barres de fer sont enfermées dans une caisse étanche au milieu d’une grande quantité de cément et mises à chauffer au rouge dans un fourneau pendant plusieurs heures. Comme vu précédemment, le fer chauffé vers 800-900° est avide de carbone qui migre lentement dans le métal et transforme celui-ci en acier. Toutefois, l’extérieur de la barre reste plus carburé que le centre, le matériau reste donc hétérogène. Il convient pour répartir le carbone de manière plus régulière dans la masse de procéder à une autre opération. Les barres sont donc étirées et soudées entre elles pour améliorer l’homogénéité du matériau, en réalisant une sorte de mille-feuilles d’acier. (Cette méthode se retrouve appliquée également dans la réalisation des aciers feuilletés japonais et dans le « Damas »). Cet acier corroyé est dit à une marque. Si la barre obtenue est repliée et ressoudée une seconde fois, ce qui améliore encore la régularité de l’acier, elle est dite à deux marques. C’est ce matériau qui sert de base à la fabrication des outils taillants, et en particulier des armes blanches. Certaines régions, par la qualité de leur minerai, auront longtemps une excellente réputation et fourniront l’ensemble du territoire en métal pour la fabrication des couteaux et des épées (dont les lames ne sont pas en fer aciéré par une mise d’acier rapportée mais en acier corroyé.) C’est également en acier corroyé que seront longtemps faits les ressorts.
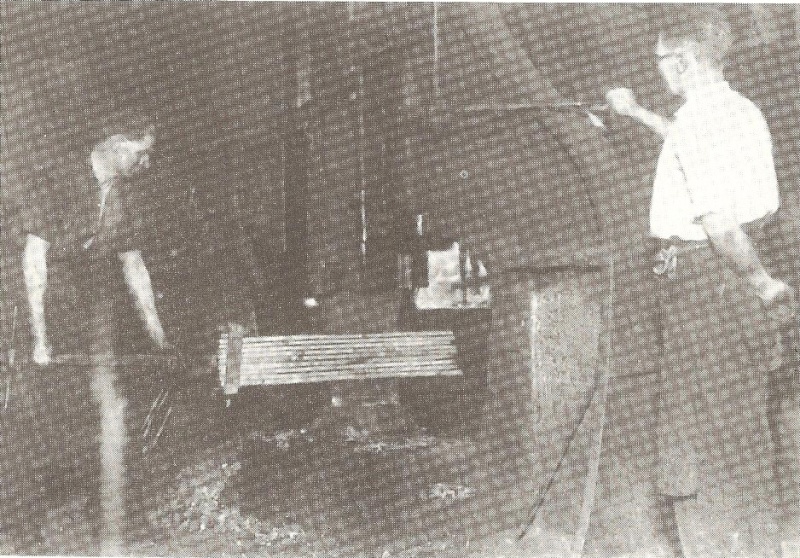
Ironworking, de W.K.V.Gale, shire edition
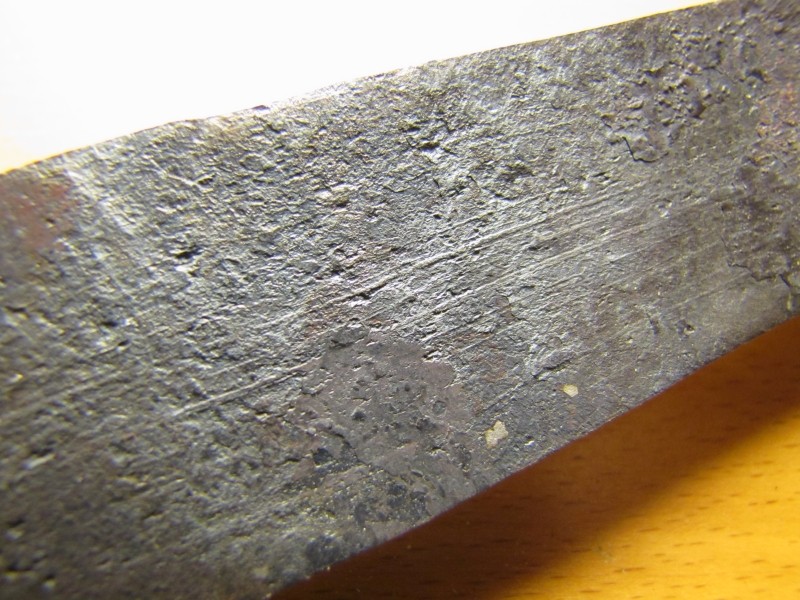
shear steel, de BladesmithForum.
Pour s’y retrouver dans les sources anglo-saxonnes, l’acier cémenté se nomme « blister steel », à cause des marques d’oxydation laissées à la surface du métal par la chauffe prolongée (c’est l’acier poule en France). Une fois corroyé, il prend le nom de « shear steel » (acier à ciseaux)
La cémentation des pièces finies
Il peut être intéressant de former une pièce en fer, qui se travaille aisément au marteau, et de l’aciérer ensuite pour lui donner une plus grande dureté de surface. Nous avons vu que pour les outils taillants, on soudait une mise d’acier sur le corps de fer. Très vite, on va utiliser la cémentation pour aciérer des pièces finies et non plus fabriquer de l’acier comme matière première. Dans le domaine qui nous intéresse, c’est en particulier le procédé qui sera utilisé pour fabriquer les chiens des armes à silex et à percussion, ainsi que les batteries des platines à silex (dans ce dernier cas, il est également possible de réaliser une mise rapportée en acier soudé).
Les pièces sont chauffées dans la même boîte à cémentation au milieu de la poudre à perlimpimpin locale et trempées en sortie de chauffe, ce qu’on appelle trempe en paquet. Le résultat, outre le durcissement de surface recherché, qui permet par exemple de faire des étincelles (batterie), ou de tenir un cran d’armé solide (chien) est une coloration par oxydation hétérogène de la surface, le jaspage.
Toutefois, s’agissant de pièces massives et non plus de fines barres, le durcissement potentiellement obtenu reste superficiel. Si le procédé convient parfaitement à un chien de révolver par exemple, dont les crans d’armé et demi-armé doivent résister à l’usure tout en permettant à la pièce de résister à des chocs répétés, on comprendra aisément qu’une alme de couteau ne pourrait être durable, le premier affilage ayant raison de la couche trempée et exposant le cœur resté doux.
freebird- Pilier du forum
- Nombre de messages : 1765
Age : 56
Localisation : Lot 46
Date d'inscription : 28/12/2013
Re: DE RE METALLICA
L'aventure continue. Entrons maintenant dans la "semi-modernitude" de l'affinage de la fonte de haut fourneau, qui va nous faire voyager de la renaissance à la fin du XIXe siècle...
De la fonte au fer
À partir de la technique de réduction en bas fourneau, nous avons vu apparaître le haut-fourneau, qui donne de la fonte. Sans les moyens de la transformer en fer, le bas fourneau aurait perduré. Mais des techniques d’affinage permettant la décarburation de la fonte ont donné à la méthode indirecte l’essor qui allait propulser la sidérurgie vers de nouveaux sommets.
L’affinage au petit foyer
La fonte possède les caractéristiques qui sont les siennes en raison du fort taux de carbone qu’elle contient. Si on ne l’utilise pas pour mouler des objets, il est possible de la transformer en fer, qui peut lui être forgé ou usiné, et pour cela, il conviendra d’en retirer le carbone. À l’inverse de la réduction, il va falloir oxyder à chaud la masse de fonte, c’est-à-dire lui fournir une quantité d’oxygène suffisante pour qu’elle se combine avec le carbone pour former du CO2, nous laissant avec du fer (mais de manière maîtrisée, sinon, on se retrouve avec de l’oxyde de fer, et toutes les opérations n’ont servi à rien).
Pour y parvenir, on chauffe dans un foyer rempli de charbon de bois des gueuses de fonte. Deux soufflets envoient un jet d’air oblique vers le fond du creuset. La température augmente dans le tas de combustible, la fonte rougit, puis fond. Elle ruisselle alors entre les charbons incandescents et traverse le vent de la tuyère pour s’amasser au fond du creuset où elle se trouve toujours exposée au souffle de l’air à cause de la disposition oblique de la tuyère. Le carbone brûle et la silice, qui se trouve toujours présente dans la fonte, s’unit à divers éléments présents dans le combustible ou rajoutés (potasse, chaux, etc...) pour former des silicates, un laitier semblable à celui rencontré lors de la réduction. Ce laitier doit être souvent soutiré par un trou prévu dans un des flancs du creuset, afin de ne pas entraver l’oxydation du carbone. En même temps que celui-ci, une grande partie des composés plus ou moins indésirables de la fonte (phosphore, soufre, manganèse,...) sont également brûlés.

foyer à la Comtoise, Le fer, la fonte et l'acier, 1875
Ce foyer est à rapprocher de la gravure de l'encyclopédie publiée dans l'article précédent et qui présentait un arrangement similaire
Au fur et à mesure que la fonte perd de son carbone, sa température de fusion augmente et le métal devient pâteux. Il faut alors procéder au soulèvement, qui consiste à lever la masse pâteuse à l’aide d’une barre de métal, le ringard, pour la présenter au vent des soufflets et parfaire l’oxydation du carbone et du silicium. Une fois l’opération jugée satisfaisante, la masse est rassemblée grâce au ringard en une éponge de fer qui n’est pas sans rappeler celle obtenue en sortie du bas fourneau. Cette loupe sera ensuite cinglée sous un martinet et transformée en barre selon le même procédé que celui vu précédemment.
Le combustible employé dans cette méthode est le charbon de bois, exclusivement, et la qualité des fers obtenus dépend de celle des fontes qui y sont traitées, en général également obtenues au charbon de bois. Ce fut pendant longtemps la source des fers les plus recherchés, appelés « fer au bois ». Ces fers étaient ceux qui servaient à l’élaboration des meilleurs aciers de cémentation et corroyés (lames, ressorts de véhicules)
On voit également que les quantités traitées à chaque opération sont nécessairement modestes, de l’ordre d’une centaine de kilos à chaque fois, pour environ six heures de chauffe.
Cette méthode, qui comportait de nombreuses variantes selon les régions, fut la seule employée pour la transformation de la fonte jusque vers 1790, où fut introduit progressivement en France l’affinage à la houille.
Mazéage et puddlage
La houille, le charbon « de terre », avait commencé à être utilisée assez tôt en Angleterre où, dès le XVIIe siècle, l’essor de la métallurgie avait mis à mal les stocks de bois que le royaume entendait bien conserver pour garder la maîtrise des mers (ce pour quoi il faut des bateaux...)
Ce n’est à la fin du XVIIIe siècle que ce combustible commencera à être utilisé en France, où il ne prendra réellement son essor que durant le XIXe siècle. Toutefois, les hauts-fourneaux tourneront encore principalement au bois, en France, jusque au milieu du XIXe siècle.
L’affinage à la houille (ou au coke, qui est du charbon de la meilleure qualité dont on a distillé le maximum d’éléments indésirables, comme on le fait pour passer du bois au charbon de bois) demande une méthodologie particulière, car il ne doit pas y avoir contact entre le combustible et le métal lors de l’affinage final, pour éviter le transfert d’impuretés qui ruineraient la qualité des fers obtenus.
On procède en deux étapes : d’abord un raffinage de la fonte, le mazéage ou finage, puis l’affinage proprement dit où la fonte fine est transformée en fer.
Le mazéage consiste à chauffer sur un lit de coke dont le feu est alimenté par le vent puissant de deux souffleries ou plus des gueuses de fontes de première coulée. Celles-ci vont fondre, la chaleur et le jet d’oxygène va brûler une partie du carbone, le soufre et le phosphore, fortement indésirables, jusqu’à liquéfaction complète des gueuses. Celles-ci sont ensuite coulées en plaque très fine sur une surface métallique et refroidies, ce qui donne de la fonte blanche, très fine et très cassante. Ce procédé était dénommé la finerie, d’après l’anglais finery, et donnait la fonte fine (fine metal). Cette fonte avait perdu une bonne partie de son carbone et la quasi-totalité du soufre et du phosphore, et devait ensuite passer dans les fours à puddler.
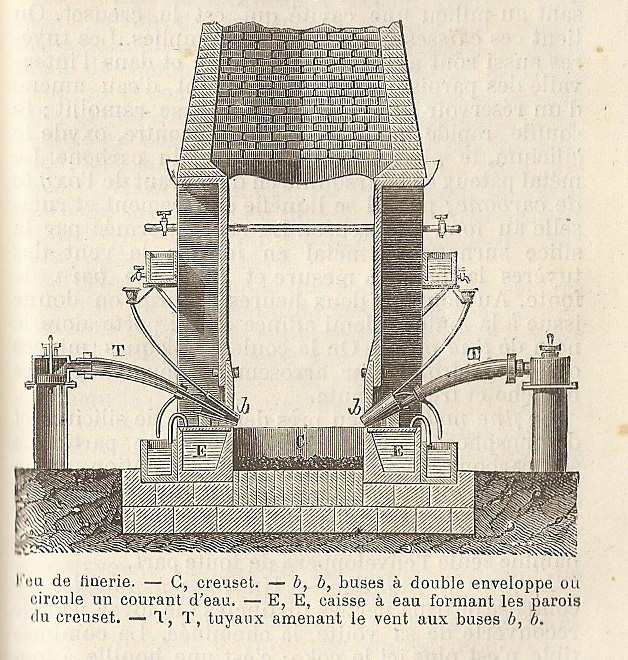
foyer de mazéage,Le fer, la fonte et l'acier, 1875
Pour pouvoir utiliser la houille (abondante et bon marché) comme combustible dans l’affinage, on utilise à partir de 1784 en Angleterre (méthode introduite en France au début de la Restauration) des fours à réverbère où la fonte et le combustible n’étaient pas en contact.
Ces fours ne sont pas en eux-mêmes une nouveauté, on les utilisait déjà depuis le début du XVIIIe pour réchauffer les barres de fer étirée avant de les couper en verges. La nouveauté consiste à s’en servir pour l’affinage de la fonte et la production de fer.
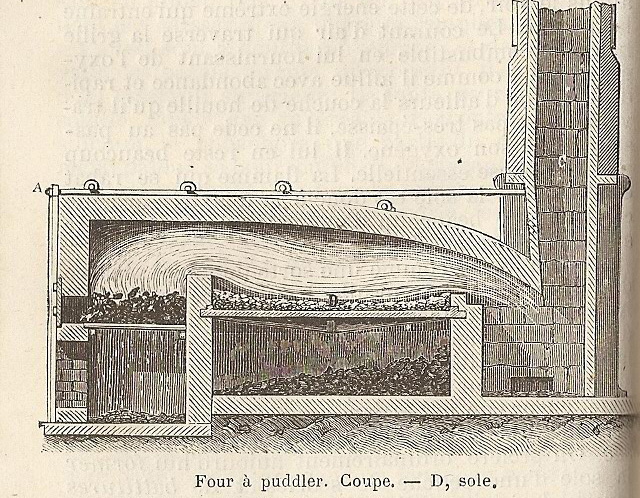
four à puddler en coupe, "Le fer, la fonte et l'acier", 1875
Le four à puddler se compose de trois zones : le foyer, la sole, recouverte de sa voûte, et la cheminée. Le combustible utilisé n’est plus le coke, comme précédemment, mais de la houille ordinaire répandue en couche peu épaisse sur une large grille. Le tirage de la cheminée, haute de 6 à 10 mètres, suffit à assurer une combustion intense et à générer de très forte chaleur. La flamme du foyer est rabattue par la voûte et vient lécher la sole. Comme la couche de houille est peu épaisse, l’oxygène de l’air qui assure la combustion n’est pas entièrement brûlé et l’atmosphère dans la chambre de chauffe est par conséquent très oxydante (chaleur + oxygène)
La sole est formée d’une couche de scories et de battitures (oxyde de fer). Ce dernier cédera lors de l’opération son oxygène au carbone de la fonte et l’opération en sera activée. Par-dessus cette couche est chargé un mélange de fonte fine et de fonte de coulée (ou de la fonte de coulée seule, selon la qualité du minerai d’origine) par une porte latérale donnant directement dans la chambre de chauffe.
La masse de fonte est très rapidement portée au rouge blanc (1350° environ) et commence à fondre et à ruisseler sur la sole. La fusion est facilitée par l’action du ringard qui brise les morceaux de fonte en fragments plus petits. Quand l’ensemble est fondu, il se produit une flamme bleue au-dessus de la masse qu’agite le « puddleur » : c’est le monoxyde de carbone de la décarburation qui brûle. L’ouvrier agite en permanence le bain de fusion à l’aide d’un ringard courbe, le rabot. (l’opération est extrêmement pénible, car la masse est lourde – de l’ordre de 180 à 200 kg par fournée – et la porte à demi ouverte l’expose à une chaleur intense).
Au fur et à mesure que l’opération avance, la masse devient pâteuse (la température de fusion augmente quand le pourcentage de carbone diminue). Le fer a tendance à s’agglomérer en masses distinctes au milieu du lit de scories en fusion. L’ouvrier les rassemble alors à l’aide du ringard en boule d’une trentaine de kg, qu’il pousse en bout de sole avant d’en former une suivante, jusqu’à avoir 6 à 8 massets qui devront être cinglés et corroyés.
Vers le dernier quart du XIXe siècle, des essais seront tentés pour mécaniser le puddlage (la manipulation du métal et la formation des massets). Nous verrons par la suite que d’autres techniques d’affinage rendront obsolètes ce progrès avant qu’il ne se soit développé.
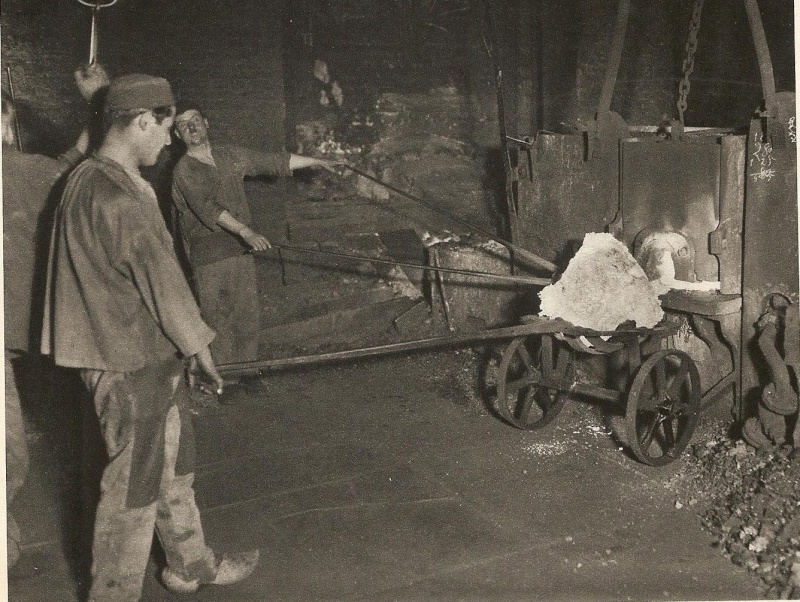
sortie du masset du four à puddler, "la France au travail", 1932
Lors du puddlage, l’oxygène de l’air de tirage et celui contenu dans l’oxyde de fer brûle le carbone de la fonte en même temps que la quasi-totalité du silicium, du soufre et du phosphore qu’elle pourrait contenir. Lorsque la manœuvre est bien exécutée, il ne reste que des traces infimes de ces impuretés et la presque totalité du carbone a disparu.
On passe ensuite au cinglage des massets, au XVIIIe siècle grâce aux martinets hydrauliques, puis à l’aide de marteaux pilon à vapeur.
Au XIXe siècle, on utilisera aussi un appareil semblable à une gigantesque pince, appelé le « squeezer », et que les ouvriers français avaient rebaptisé le crocodile.
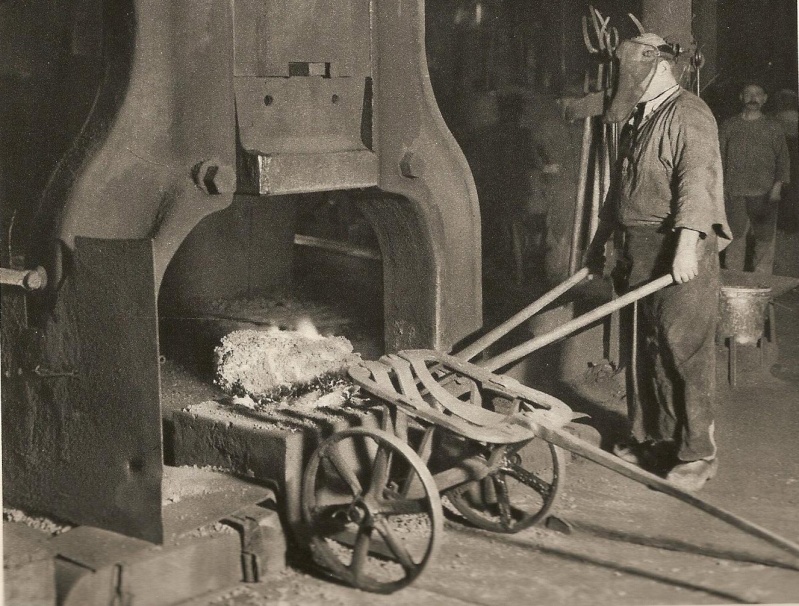
cinglage du masset au marteau pilon, "la France au travail", 1932
Noter que le masset est très proche en taille et en structure à la loupe issue du bas fourneau ou au masset issu de l'affinage au petit foyer: le matériau obtenu au bout de la chaîne reste du fer forgé.
Les lingots cinglés, débarrassés des scories et compactés, seront ensuite passés au laminoir pour être étirés.Le laminoir apparait au XVIIIe siècle, et ne constitue au début qu'une préparation du lingot avant l'étirage ou le platinage au marteau. Il deviendra le principal outil de préparation des fers bruts au cours du XIXe siècle.
En sortie de laminoir, le fer est dit brut. Il a des défauts, des pailles, et ne peut convenir qu’à des usages assez grossiers. Pour le transformer en fer marchand, les barres laminées sont coupées à la cisaille mécanique en plaquettes d’une trentaine de centimètres de longueur avec lesquelles on forme des paquets, reliés au fil de fer, qui seront ensuite soudés à chaud pour donner un matériau aux caractéristiques reproductibles. On retrouve le travail de corroyage vu en sortie de bas-fourneau. Les fers de la meilleure qualité sont alors cémentés avant corroyage pour donner l’acier corroyé (shear steel)

croquis d'un laminoir vers 1875.
L’acier puddlé
Tout comme un bas fourneau bien mené peut donner de l’acier et non du fer sous réserve que la décarburation du métal réduit soit incomplète, le puddlage offre les mêmes possibilités. L’ouvrier doit à l’œil et au « toucher » sentir la masse de métal en fusion devenir pâteuse et arrêter l’opération avant décarburation complète. L’ajout en cours de fonte de scories, de battitures, d’oxyde de manganèse, de sel marin et de flurorure de calcium permet la disparition des impuretés (silicium, phosphore, souffre) avant disparition complète du carbone. L’acier obtenu est ensuite étiré et corroyé comme le fer. Toutefois, pour obtenir de l’acier par cette méthode, il est impératif de partir de fontes d’excellente qualité, contenant très peu de phosphore et de soufre, elles-mêmes issues de minerai très purs, ce qui limite les capacités de production d’acier et explique la prépondérance du fer dans le gros œuvre jusqu’à l’avènement des convertisseurs.
Les rails des premiers chemins de fer (vers 1830) étaient tous en fer puddlé. Leur usure était rapide, et ils seront par la suite réalisés en acier puddlé cémenté, avant que n’entrent en action les convertisseurs, mais comme dirait Conan, ceci est une autre histoire...
La tour Eiffel, comme d’innombrables ouvrages d’art de la fin du XIXe siècle, est entièrement réalisée en fer puddlé !
À l'issue du prochain article, qui vous présentera les merveilles de l'acier fondu, ce qu'il est et ce qu'il n'est pas, ainsi que l’avènement des convertisseurs, nous survolerons quelques chiffres de productions des différents métaux au fil des siècles...
(édition: rajout d'une illustration.)
De la fonte au fer
À partir de la technique de réduction en bas fourneau, nous avons vu apparaître le haut-fourneau, qui donne de la fonte. Sans les moyens de la transformer en fer, le bas fourneau aurait perduré. Mais des techniques d’affinage permettant la décarburation de la fonte ont donné à la méthode indirecte l’essor qui allait propulser la sidérurgie vers de nouveaux sommets.
L’affinage au petit foyer
La fonte possède les caractéristiques qui sont les siennes en raison du fort taux de carbone qu’elle contient. Si on ne l’utilise pas pour mouler des objets, il est possible de la transformer en fer, qui peut lui être forgé ou usiné, et pour cela
Pour y parvenir, on chauffe dans un foyer rempli de charbon de bois des gueuses de fonte. Deux soufflets envoient un jet d’air oblique vers le fond du creuset. La température augmente dans le tas de combustible, la fonte rougit, puis fond. Elle ruisselle alors entre les charbons incandescents et traverse le vent de la tuyère pour s’amasser au fond du creuset où elle se trouve toujours exposée au souffle de l’air à cause de la disposition oblique de la tuyère. Le carbone brûle et la silice, qui se trouve toujours présente dans la fonte, s’unit à divers éléments présents dans le combustible ou rajoutés (potasse, chaux, etc...) pour former des silicates, un laitier semblable à celui rencontré lors de la réduction. Ce laitier doit être souvent soutiré par un trou prévu dans un des flancs du creuset, afin de ne pas entraver l’oxydation du carbone. En même temps que celui-ci, une grande partie des composés plus ou moins indésirables de la fonte (phosphore, soufre, manganèse,...) sont également brûlés.

foyer à la Comtoise, Le fer, la fonte et l'acier, 1875
Ce foyer est à rapprocher de la gravure de l'encyclopédie publiée dans l'article précédent et qui présentait un arrangement similaire
Au fur et à mesure que la fonte perd de son carbone, sa température de fusion augmente et le métal devient pâteux. Il faut alors procéder au soulèvement, qui consiste à lever la masse pâteuse à l’aide d’une barre de métal, le ringard, pour la présenter au vent des soufflets et parfaire l’oxydation du carbone et du silicium. Une fois l’opération jugée satisfaisante, la masse est rassemblée grâce au ringard en une éponge de fer qui n’est pas sans rappeler celle obtenue en sortie du bas fourneau. Cette loupe sera ensuite cinglée sous un martinet et transformée en barre selon le même procédé que celui vu précédemment.
Le combustible employé dans cette méthode est le charbon de bois, exclusivement, et la qualité des fers obtenus dépend de celle des fontes qui y sont traitées, en général également obtenues au charbon de bois. Ce fut pendant longtemps la source des fers les plus recherchés, appelés « fer au bois ». Ces fers étaient ceux qui servaient à l’élaboration des meilleurs aciers de cémentation et corroyés (lames, ressorts de véhicules)
On voit également que les quantités traitées à chaque opération sont nécessairement modestes, de l’ordre d’une centaine de kilos à chaque fois, pour environ six heures de chauffe.
Cette méthode, qui comportait de nombreuses variantes selon les régions, fut la seule employée pour la transformation de la fonte jusque vers 1790, où fut introduit progressivement en France l’affinage à la houille.
Mazéage et puddlage
La houille, le charbon « de terre », avait commencé à être utilisée assez tôt en Angleterre où, dès le XVIIe siècle, l’essor de la métallurgie avait mis à mal les stocks de bois que le royaume entendait bien conserver pour garder la maîtrise des mers (ce pour quoi il faut des bateaux...)
Ce n’est à la fin du XVIIIe siècle que ce combustible commencera à être utilisé en France, où il ne prendra réellement son essor que durant le XIXe siècle. Toutefois, les hauts-fourneaux tourneront encore principalement au bois, en France, jusque au milieu du XIXe siècle.
L’affinage à la houille (ou au coke, qui est du charbon de la meilleure qualité dont on a distillé le maximum d’éléments indésirables, comme on le fait pour passer du bois au charbon de bois) demande une méthodologie particulière, car il ne doit pas y avoir contact entre le combustible et le métal lors de l’affinage final, pour éviter le transfert d’impuretés qui ruineraient la qualité des fers obtenus.
On procède en deux étapes : d’abord un raffinage de la fonte, le mazéage ou finage, puis l’affinage proprement dit où la fonte fine est transformée en fer.
Le mazéage consiste à chauffer sur un lit de coke dont le feu est alimenté par le vent puissant de deux souffleries ou plus des gueuses de fontes de première coulée. Celles-ci vont fondre, la chaleur et le jet d’oxygène va brûler une partie du carbone, le soufre et le phosphore, fortement indésirables, jusqu’à liquéfaction complète des gueuses. Celles-ci sont ensuite coulées en plaque très fine sur une surface métallique et refroidies, ce qui donne de la fonte blanche, très fine et très cassante. Ce procédé était dénommé la finerie, d’après l’anglais finery, et donnait la fonte fine (fine metal). Cette fonte avait perdu une bonne partie de son carbone et la quasi-totalité du soufre et du phosphore, et devait ensuite passer dans les fours à puddler.
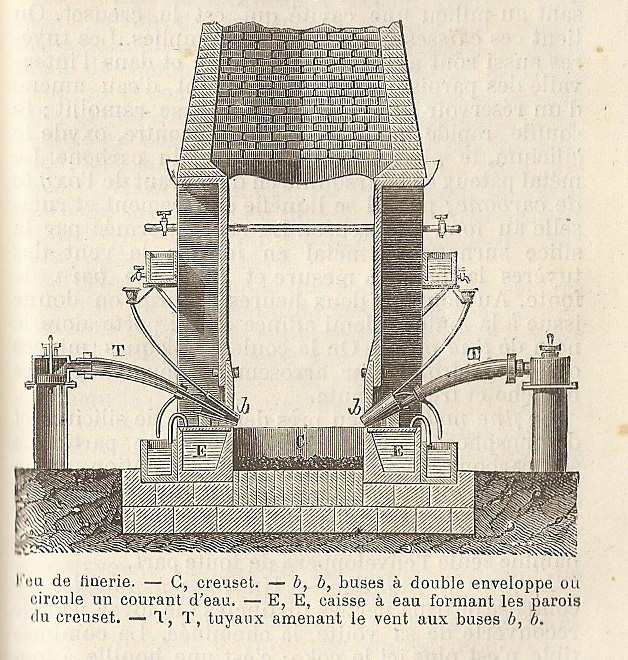
foyer de mazéage,Le fer, la fonte et l'acier, 1875
Pour pouvoir utiliser la houille (abondante et bon marché) comme combustible dans l’affinage, on utilise à partir de 1784 en Angleterre (méthode introduite en France au début de la Restauration) des fours à réverbère où la fonte et le combustible n’étaient pas en contact.
Ces fours ne sont pas en eux-mêmes une nouveauté, on les utilisait déjà depuis le début du XVIIIe pour réchauffer les barres de fer étirée avant de les couper en verges. La nouveauté consiste à s’en servir pour l’affinage de la fonte et la production de fer.
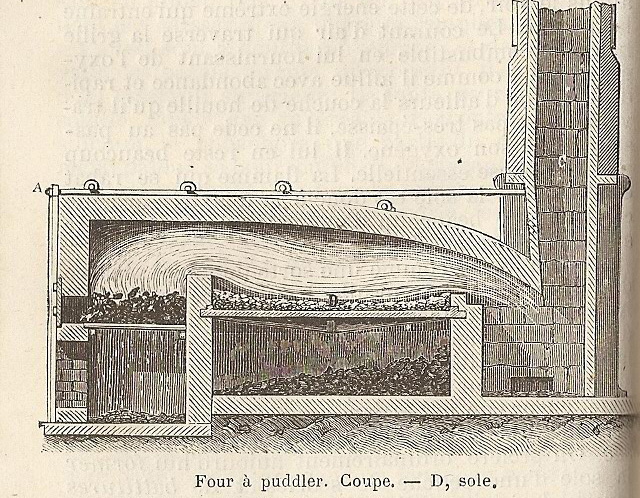
four à puddler en coupe, "Le fer, la fonte et l'acier", 1875
Le four à puddler se compose de trois zones : le foyer, la sole, recouverte de sa voûte, et la cheminée. Le combustible utilisé n’est plus le coke, comme précédemment, mais de la houille ordinaire répandue en couche peu épaisse sur une large grille. Le tirage de la cheminée, haute de 6 à 10 mètres, suffit à assurer une combustion intense et à générer de très forte chaleur. La flamme du foyer est rabattue par la voûte et vient lécher la sole. Comme la couche de houille est peu épaisse, l’oxygène de l’air qui assure la combustion n’est pas entièrement brûlé et l’atmosphère dans la chambre de chauffe est par conséquent très oxydante (chaleur + oxygène)
La sole est formée d’une couche de scories et de battitures (oxyde de fer). Ce dernier cédera lors de l’opération son oxygène au carbone de la fonte et l’opération en sera activée. Par-dessus cette couche est chargé un mélange de fonte fine et de fonte de coulée (ou de la fonte de coulée seule, selon la qualité du minerai d’origine) par une porte latérale donnant directement dans la chambre de chauffe.
La masse de fonte est très rapidement portée au rouge blanc (1350° environ) et commence à fondre et à ruisseler sur la sole. La fusion est facilitée par l’action du ringard qui brise les morceaux de fonte en fragments plus petits. Quand l’ensemble est fondu, il se produit une flamme bleue au-dessus de la masse qu’agite le « puddleur » : c’est le monoxyde de carbone de la décarburation qui brûle. L’ouvrier agite en permanence le bain de fusion à l’aide d’un ringard courbe, le rabot. (l’opération est extrêmement pénible, car la masse est lourde – de l’ordre de 180 à 200 kg par fournée – et la porte à demi ouverte l’expose à une chaleur intense).
Au fur et à mesure que l’opération avance, la masse devient pâteuse (la température de fusion augmente quand le pourcentage de carbone diminue). Le fer a tendance à s’agglomérer en masses distinctes au milieu du lit de scories en fusion. L’ouvrier les rassemble alors à l’aide du ringard en boule d’une trentaine de kg, qu’il pousse en bout de sole avant d’en former une suivante, jusqu’à avoir 6 à 8 massets qui devront être cinglés et corroyés.
Vers le dernier quart du XIXe siècle, des essais seront tentés pour mécaniser le puddlage (la manipulation du métal et la formation des massets). Nous verrons par la suite que d’autres techniques d’affinage rendront obsolètes ce progrès avant qu’il ne se soit développé.
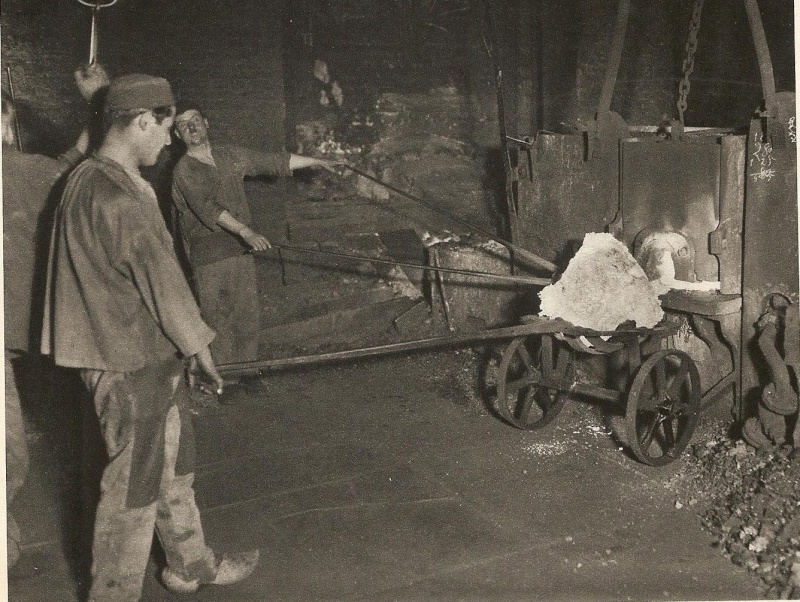
sortie du masset du four à puddler, "la France au travail", 1932
Lors du puddlage, l’oxygène de l’air de tirage et celui contenu dans l’oxyde de fer brûle le carbone de la fonte en même temps que la quasi-totalité du silicium, du soufre et du phosphore qu’elle pourrait contenir. Lorsque la manœuvre est bien exécutée, il ne reste que des traces infimes de ces impuretés et la presque totalité du carbone a disparu.
On passe ensuite au cinglage des massets, au XVIIIe siècle grâce aux martinets hydrauliques, puis à l’aide de marteaux pilon à vapeur.
Au XIXe siècle, on utilisera aussi un appareil semblable à une gigantesque pince, appelé le « squeezer », et que les ouvriers français avaient rebaptisé le crocodile.
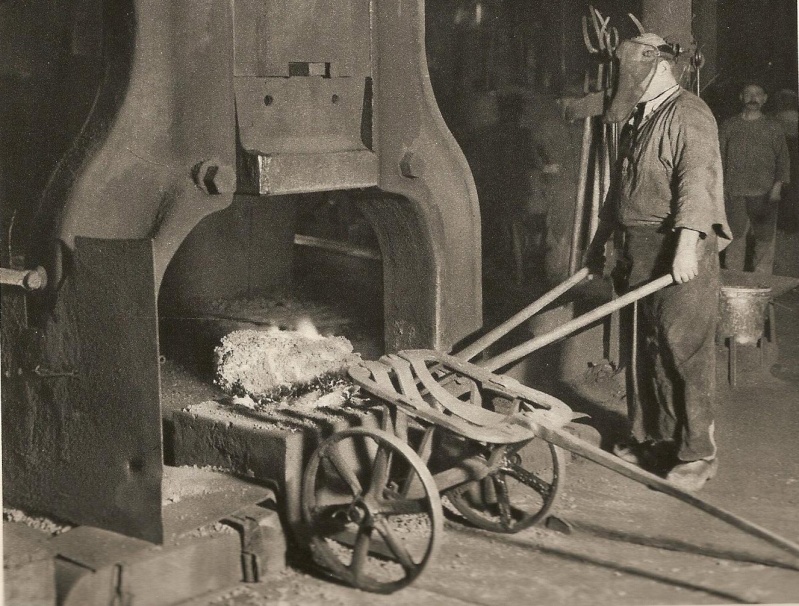
cinglage du masset au marteau pilon, "la France au travail", 1932
Noter que le masset est très proche en taille et en structure à la loupe issue du bas fourneau ou au masset issu de l'affinage au petit foyer: le matériau obtenu au bout de la chaîne reste du fer forgé.
Les lingots cinglés, débarrassés des scories et compactés, seront ensuite passés au laminoir pour être étirés.Le laminoir apparait au XVIIIe siècle, et ne constitue au début qu'une préparation du lingot avant l'étirage ou le platinage au marteau. Il deviendra le principal outil de préparation des fers bruts au cours du XIXe siècle.
En sortie de laminoir, le fer est dit brut. Il a des défauts, des pailles, et ne peut convenir qu’à des usages assez grossiers. Pour le transformer en fer marchand, les barres laminées sont coupées à la cisaille mécanique en plaquettes d’une trentaine de centimètres de longueur avec lesquelles on forme des paquets, reliés au fil de fer, qui seront ensuite soudés à chaud pour donner un matériau aux caractéristiques reproductibles. On retrouve le travail de corroyage vu en sortie de bas-fourneau. Les fers de la meilleure qualité sont alors cémentés avant corroyage pour donner l’acier corroyé (shear steel)

croquis d'un laminoir vers 1875.
L’acier puddlé
Tout comme un bas fourneau bien mené peut donner de l’acier et non du fer sous réserve que la décarburation du métal réduit soit incomplète, le puddlage offre les mêmes possibilités. L’ouvrier doit à l’œil et au « toucher » sentir la masse de métal en fusion devenir pâteuse et arrêter l’opération avant décarburation complète. L’ajout en cours de fonte de scories, de battitures, d’oxyde de manganèse, de sel marin et de flurorure de calcium permet la disparition des impuretés (silicium, phosphore, souffre) avant disparition complète du carbone. L’acier obtenu est ensuite étiré et corroyé comme le fer. Toutefois, pour obtenir de l’acier par cette méthode, il est impératif de partir de fontes d’excellente qualité, contenant très peu de phosphore et de soufre, elles-mêmes issues de minerai très purs, ce qui limite les capacités de production d’acier et explique la prépondérance du fer dans le gros œuvre jusqu’à l’avènement des convertisseurs.
Les rails des premiers chemins de fer (vers 1830) étaient tous en fer puddlé. Leur usure était rapide, et ils seront par la suite réalisés en acier puddlé cémenté, avant que n’entrent en action les convertisseurs, mais comme dirait Conan, ceci est une autre histoire...
La tour Eiffel, comme d’innombrables ouvrages d’art de la fin du XIXe siècle, est entièrement réalisée en fer puddlé !
À l'issue du prochain article, qui vous présentera les merveilles de l'acier fondu, ce qu'il est et ce qu'il n'est pas, ainsi que l’avènement des convertisseurs, nous survolerons quelques chiffres de productions des différents métaux au fil des siècles...
(édition: rajout d'une illustration.)
freebird- Pilier du forum
- Nombre de messages : 1765
Age : 56
Localisation : Lot 46
Date d'inscription : 28/12/2013
Re: DE RE METALLICA
un mois déjà... devant votre silence assourdissant, je continue la publication, encore quelques articles et nous pourrons commencer à relier le métal brut et les armes qui l'utilisaient...
L'acier au creuset
Des débuts de la métallurgie du fer jusqu’à la fin du XVIIIe siècle, l’acier n’était disponible que sous deux formes :
– l’acier naturel : obtenu au bas fourneau en maîtrisant la décarburation de la masse de fer en réduction, ou lors de l’affinage de la fonte, au petit foyer ou par puddlage, en arrêtant l’opération également avant décarburation. Cet acier était inégalement carburé, fibreux, incluait des scories : c’était un matériau hétérogène.
(l'acier naturel s'obtenait également dans des forges d’affinage spéciales, dite « renardières », de dimensions plus réduites que les foyers d’affinage normaux afin de mieux contrôler le travail. Elles servaient à recycler les déchets des divers ateliers : extrémité des gueuses de fonte, scories ferreuses de l’affinerie, battitures du marteau et des martinets*, déchets de fer divers ; avec ces matières on obtenait plutôt de l’acier, mais assez irrégulier quoique le poste ait été réputé comme nécessitant la plus grande expérience. Les forges achetaient donc l’acier nécessaire à leurs outils, même quand elles disposaient d’une renardière.)
– l’acier cémenté : obtenu à partir de fer corroyé de la meilleure qualité possible (fer au bois), selon la méthode de cémentation au four, et rendu plus homogène par corroyage, c’était ce matériau qui était utilisé pour tous les usages « nobles » : ressort, outils taillant de qualité, armes blanches.
Mais même ce dernier matériau était encore imparfait dès que l’on voulait en tirer des qualités techniques poussées, en particulier dans la fabrication des ressorts d’horlogerie. C’est pour cet usage que fut inventé en 1760 (même s’il existait depuis longtemps sous une forme presque identique en Orient) le procédé de l’acier fondu, à Sheffield.
Il ne s’agit pas d’une méthode de production particulière, mais d’un procédé assurant l’homogénéité parfaite de la répartition du carbone dans le métal.
Il s’agit, pour simplifier, de faire fondre au four, dans un creuset hermétique en graphite, des morceaux d’acier obtenu par l’une des méthodes précédentes afin d’en assurer le mélange intime et la régularité.
les températures très élevées nécessaires à faire fondre de l'acier impliquent une grande consommation de combustibles, et les creusets destinés à contenir le métal en fusion coûtent également très cher et ne survivent en général pas à l'opération, ce qui explique que cette méthode, bien qu'elle procure un matériau de tout premier ordre, restera cantonnée à des productions relativement modeste, le métal de construction restant longtemps le fer puddlé.
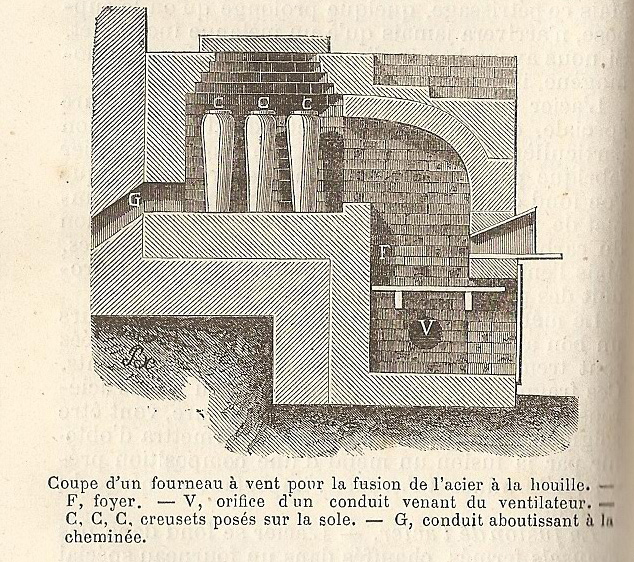
vue en coupe d'un fourneau à creusets, vers 1875.
Les meilleurs aciers fondus sont obtenus à partir de fers au bois cémentés et triés. Les barres cémentées sont trempées et brisées à froid. L’aspect de la cassure permet de trier le métal par type, plus ou moins dur, et par là, plus ou moins riche en carbone. On fond ensuite, selon le résultat recherché, des morceaux du même type, ce qui permet d’obtenir à la fois un matériau homogène, mais aussi d’une dureté et d’une trempabilité prévisible.
Il est théoriquement possible de mélanger du fer pur et de la fonte, qui en se mélangeant donneront de l'acier. Mais la qualité du résultat n'était pas à la hauteur des attentes de ce procédé (mais nous le retrouverons utilisé dans la recarburation du fer obtenu par le procédé Bessemer)
Puis on coule le métal fondu dans une lingotière sur laquelle est aussitôt posé un lourds bouchon de fonte afin d'éviter au maximum les problèmes de dégazages et de retassures (bulles d'air au coeur de la matière). Le lingot refroidi pourra être forgé ou usiné (et en général, les deux...)
Pour l’anecdote, Huntsman, inventeur du procédé, essaiera d’abord de le garder secret. Mais celui-ci fut vite éventé et son nouvel acier sera proposé aux ouvriers couteliers de Sheffield, qui le refuseront, car trop difficile à travailler. Et c’est en France que cet acier trouvera son premier essor, dans la coutellerie, tant et si bien que les ouvriers de Sheffield pétitionneront le parlement britannique pour qu’il en interdise l’export. Ce qui sera refusé.
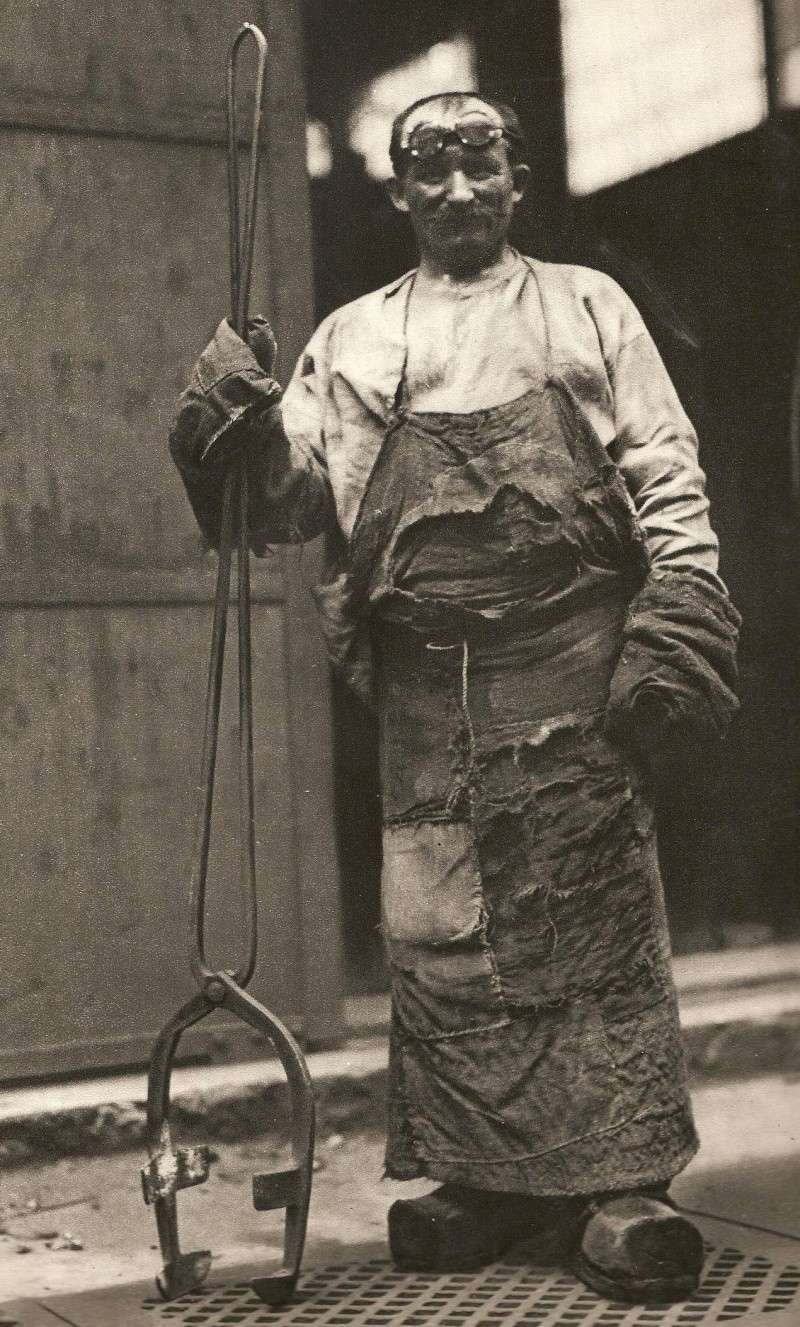
L'arracheur de creuset, vers 1932, debout au dessus de l'ouverture supérieur du fourneau, par lequel il va sortir le creuset avant la coulée.

le coulage de l'acier dans la lingotière. Le creuset contient entre 20 et 30 kilogrammes d'acier, et le jet de métal fondu ne doit en aucun cas toucher les parois de la lingotière pendant la coulée.
Nous abordons maintenant une question de vocabulaire importante : l’acier fondu, en anglais « cast steel » ou « crucible steel », est également nommé « acier au creuset », et vers la fin XIXe et le début du XXe, « acier au creuset véritable » (ce qui pourrait laisser penser que l’avènement d’autres sources d’acier homogène à ces périodes avait tenté faussaires et vendeurs de vessie pour des lanternes)
Souvent, les pièces finies réalisées à partir de ce matériau spécifique sont marquées ainsi, ce qui est un signe de qualité (du matériau de base, pas forcément de la pièce). Et dans tous les cas, ce marquage s’applique à la méthode de production de l’acier, et non à la façon dont a été produite la pièce.
Ainsi, tous les outils et armes marqués « acier fondu » sont fabriqués, par différentes méthodes, forgeage ou usinage, en acier au creuset, mais en aucun cas ce marquage ne veut dire que la pièce a été coulée. Le coulage de pièces en acier, dit « microfusion », n’interviendra que tardivement dans le cours du XXe siècle.
Il y aura effectivement apparition de méthode de production de pièces de quincaillerie par moulage selon le procédé de la fonte malléable, et ce procédé sera appliqué aux armes à feu, mais ces pièces ne sont pas, à proprement parler, en acier, et elles ne sont jamais marquées « acier fondu ».
Il est très fréquent dans la littérature récente de voir utiliser à tort les termes « acier fondu » pour caractériser une pièce en « acier moulé », ou « acier coulé », cette dernière expression étant en général entachée d’une image de qualité médiocre, alors que les termes « acier fondu » portent justement une réputation inverse.
La fonte malléable.
Selon un procédé inverse de la cémentation des fers pour en faire de l’acier, il est possible de décarburer des objets coulés en fonte à leur forme définitive. La fonte se transforme alors en un métal proche de l’acier, mais sans homogénéité, qui se nommait fonte malléable ou fonte aciérée.
On utilisait pour cela de la limaille de fer (par migration du carbone de la fonte au fer = inverse de la cémentation) ou de l’hématite rouge, un oxyde fer pulvérisé (qui brûlait le carbone comme lors d’un affinage). La pièce est décarburée en surface, ce qui ôte à la fonte son caractère fragile et sa dureté. La fonte malléable peut s’usiner facilement et s’écrase sous le marteau au lieu de se briser.
Mais, à taux de carbone identique, la fonte aciérée n’a pas la structure cristalline resserrée donnée à l’acier par le forgeage, et ses caractéristiques mécaniques restent inférieures (même usinée dans la masse, une pièce en acier a toujours été forgée, laminée ou étirée à un moment ou un autre). De plus, si le travail est bâclé ce n’est pas de la fonte aciérée … mais de la fonte ordinaire !
Dès 1875, on trouve des critiques acerbes sur l’usage grandissant de ce matériau dans la quincaillerie et la serrurerie, où la rapidité de fabrication l’emporte (déjà) sur la qualité des pièces finies.
À bientôt pour la découverte des procédés de conversion liquide qui allaient révolutionner la métallurgie...
L'acier au creuset
Des débuts de la métallurgie du fer jusqu’à la fin du XVIIIe siècle, l’acier n’était disponible que sous deux formes :
– l’acier naturel : obtenu au bas fourneau en maîtrisant la décarburation de la masse de fer en réduction, ou lors de l’affinage de la fonte, au petit foyer ou par puddlage, en arrêtant l’opération également avant décarburation. Cet acier était inégalement carburé, fibreux, incluait des scories : c’était un matériau hétérogène.
(l'acier naturel s'obtenait également dans des forges d’affinage spéciales, dite « renardières », de dimensions plus réduites que les foyers d’affinage normaux afin de mieux contrôler le travail. Elles servaient à recycler les déchets des divers ateliers : extrémité des gueuses de fonte, scories ferreuses de l’affinerie, battitures du marteau et des martinets*, déchets de fer divers ; avec ces matières on obtenait plutôt de l’acier, mais assez irrégulier quoique le poste ait été réputé comme nécessitant la plus grande expérience. Les forges achetaient donc l’acier nécessaire à leurs outils, même quand elles disposaient d’une renardière.)
– l’acier cémenté : obtenu à partir de fer corroyé de la meilleure qualité possible (fer au bois), selon la méthode de cémentation au four, et rendu plus homogène par corroyage, c’était ce matériau qui était utilisé pour tous les usages « nobles » : ressort, outils taillant de qualité, armes blanches.
Mais même ce dernier matériau était encore imparfait dès que l’on voulait en tirer des qualités techniques poussées, en particulier dans la fabrication des ressorts d’horlogerie. C’est pour cet usage que fut inventé en 1760 (même s’il existait depuis longtemps sous une forme presque identique en Orient) le procédé de l’acier fondu, à Sheffield.
Il ne s’agit pas d’une méthode de production particulière, mais d’un procédé assurant l’homogénéité parfaite de la répartition du carbone dans le métal.
Il s’agit, pour simplifier, de faire fondre au four, dans un creuset hermétique en graphite, des morceaux d’acier obtenu par l’une des méthodes précédentes afin d’en assurer le mélange intime et la régularité.
les températures très élevées nécessaires à faire fondre de l'acier impliquent une grande consommation de combustibles, et les creusets destinés à contenir le métal en fusion coûtent également très cher et ne survivent en général pas à l'opération, ce qui explique que cette méthode, bien qu'elle procure un matériau de tout premier ordre, restera cantonnée à des productions relativement modeste, le métal de construction restant longtemps le fer puddlé.
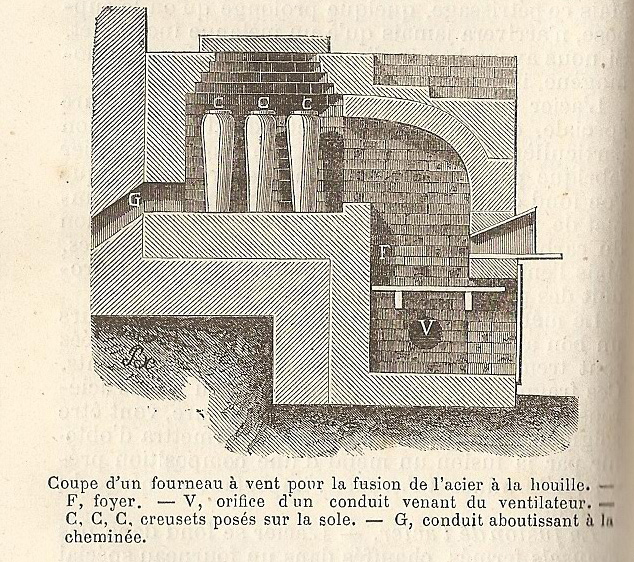
vue en coupe d'un fourneau à creusets, vers 1875.
Les meilleurs aciers fondus sont obtenus à partir de fers au bois cémentés et triés. Les barres cémentées sont trempées et brisées à froid. L’aspect de la cassure permet de trier le métal par type, plus ou moins dur, et par là, plus ou moins riche en carbone. On fond ensuite, selon le résultat recherché, des morceaux du même type, ce qui permet d’obtenir à la fois un matériau homogène, mais aussi d’une dureté et d’une trempabilité prévisible.
Il est théoriquement possible de mélanger du fer pur et de la fonte, qui en se mélangeant donneront de l'acier. Mais la qualité du résultat n'était pas à la hauteur des attentes de ce procédé (mais nous le retrouverons utilisé dans la recarburation du fer obtenu par le procédé Bessemer)
Puis on coule le métal fondu dans une lingotière sur laquelle est aussitôt posé un lourds bouchon de fonte afin d'éviter au maximum les problèmes de dégazages et de retassures (bulles d'air au coeur de la matière). Le lingot refroidi pourra être forgé ou usiné (et en général, les deux...)
Pour l’anecdote, Huntsman, inventeur du procédé, essaiera d’abord de le garder secret. Mais celui-ci fut vite éventé et son nouvel acier sera proposé aux ouvriers couteliers de Sheffield, qui le refuseront, car trop difficile à travailler. Et c’est en France que cet acier trouvera son premier essor, dans la coutellerie, tant et si bien que les ouvriers de Sheffield pétitionneront le parlement britannique pour qu’il en interdise l’export. Ce qui sera refusé.
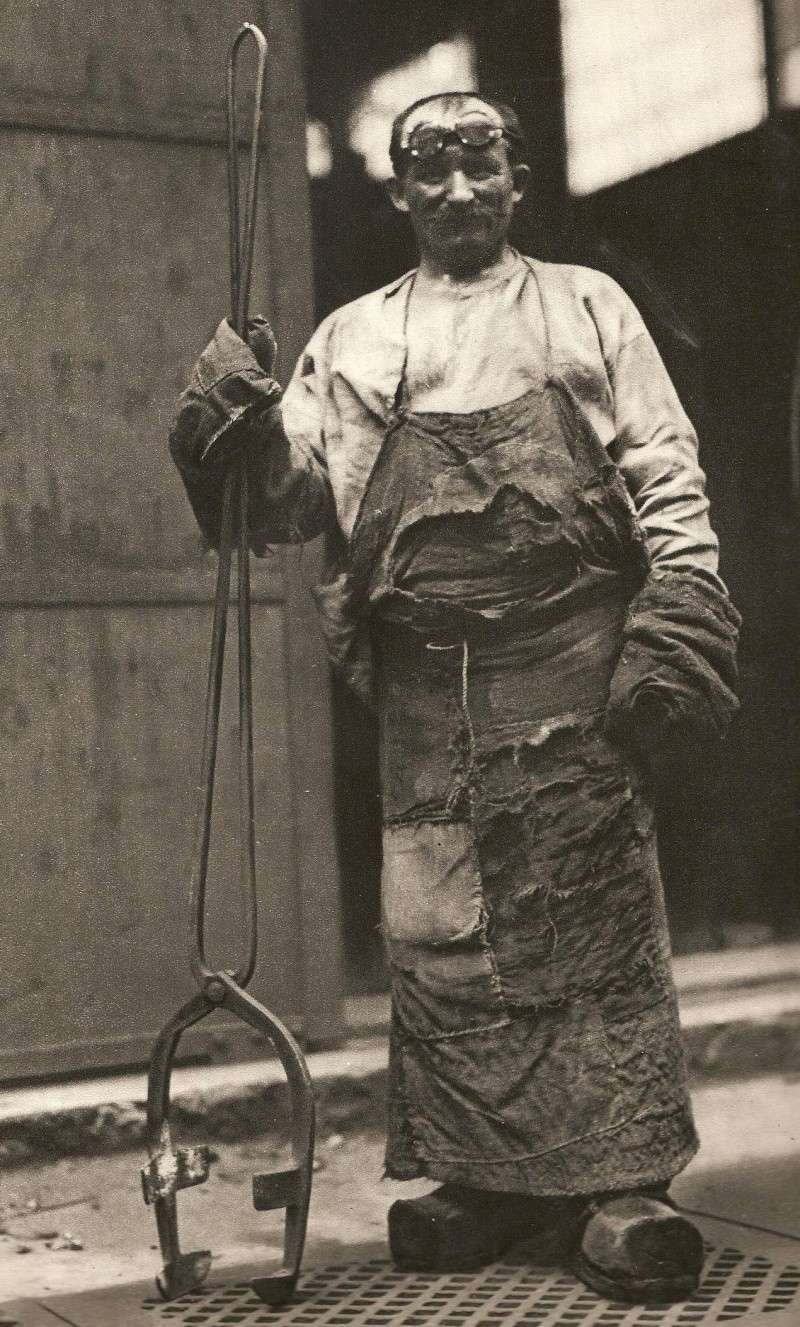
L'arracheur de creuset, vers 1932, debout au dessus de l'ouverture supérieur du fourneau, par lequel il va sortir le creuset avant la coulée.

le coulage de l'acier dans la lingotière. Le creuset contient entre 20 et 30 kilogrammes d'acier, et le jet de métal fondu ne doit en aucun cas toucher les parois de la lingotière pendant la coulée.
Nous abordons maintenant une question de vocabulaire importante : l’acier fondu, en anglais « cast steel » ou « crucible steel », est également nommé « acier au creuset », et vers la fin XIXe et le début du XXe, « acier au creuset véritable » (ce qui pourrait laisser penser que l’avènement d’autres sources d’acier homogène à ces périodes avait tenté faussaires et vendeurs de vessie pour des lanternes)
Souvent, les pièces finies réalisées à partir de ce matériau spécifique sont marquées ainsi, ce qui est un signe de qualité (du matériau de base, pas forcément de la pièce). Et dans tous les cas, ce marquage s’applique à la méthode de production de l’acier, et non à la façon dont a été produite la pièce.
Ainsi, tous les outils et armes marqués « acier fondu » sont fabriqués, par différentes méthodes, forgeage ou usinage, en acier au creuset, mais en aucun cas ce marquage ne veut dire que la pièce a été coulée. Le coulage de pièces en acier, dit « microfusion », n’interviendra que tardivement dans le cours du XXe siècle.
Il y aura effectivement apparition de méthode de production de pièces de quincaillerie par moulage selon le procédé de la fonte malléable, et ce procédé sera appliqué aux armes à feu, mais ces pièces ne sont pas, à proprement parler, en acier, et elles ne sont jamais marquées « acier fondu ».
Il est très fréquent dans la littérature récente de voir utiliser à tort les termes « acier fondu » pour caractériser une pièce en « acier moulé », ou « acier coulé », cette dernière expression étant en général entachée d’une image de qualité médiocre, alors que les termes « acier fondu » portent justement une réputation inverse.
La fonte malléable.
Selon un procédé inverse de la cémentation des fers pour en faire de l’acier, il est possible de décarburer des objets coulés en fonte à leur forme définitive. La fonte se transforme alors en un métal proche de l’acier, mais sans homogénéité, qui se nommait fonte malléable ou fonte aciérée.
On utilisait pour cela de la limaille de fer (par migration du carbone de la fonte au fer = inverse de la cémentation) ou de l’hématite rouge, un oxyde fer pulvérisé (qui brûlait le carbone comme lors d’un affinage). La pièce est décarburée en surface, ce qui ôte à la fonte son caractère fragile et sa dureté. La fonte malléable peut s’usiner facilement et s’écrase sous le marteau au lieu de se briser.
Mais, à taux de carbone identique, la fonte aciérée n’a pas la structure cristalline resserrée donnée à l’acier par le forgeage, et ses caractéristiques mécaniques restent inférieures (même usinée dans la masse, une pièce en acier a toujours été forgée, laminée ou étirée à un moment ou un autre). De plus, si le travail est bâclé ce n’est pas de la fonte aciérée … mais de la fonte ordinaire !
Dès 1875, on trouve des critiques acerbes sur l’usage grandissant de ce matériau dans la quincaillerie et la serrurerie, où la rapidité de fabrication l’emporte (déjà) sur la qualité des pièces finies.
À bientôt pour la découverte des procédés de conversion liquide qui allaient révolutionner la métallurgie...
Dernière édition par freebird le Ven 15 Aoû 2014, 16:04, édité 1 fois
freebird- Pilier du forum
- Nombre de messages : 1765
Age : 56
Localisation : Lot 46
Date d'inscription : 28/12/2013
Re: DE RE METALLICA
Super....On continue à s'instruire !!!!!
Non nobis Domine, non nobis, sed Nomini Tuo da Gloriam.
http://winchester-lsg.forumotion.com/
http://prehistoire-xixeme.forumactif.org/
CLOSDELIF- Pilier du forum
- Nombre de messages : 22791
Age : 72
Localisation : 81
Date d'inscription : 03/09/2009
Re: DE RE METALLICA
freebird a écrit:un mois déjà... devant votre silence assourdissant, je continue la publication
Sujet suivi avec ferveur...
Si tout un chacun lit vos très bons & très abordables documents avec le même intérêt que moi, toute intervention non pertinente paraitrait "polluer" ce post d'un plus haut intérêt!
Dans l'impatiente attente de la suite...
Et merci encore!
Pâtre- Pilier du forum
- Nombre de messages : 7508
Age : 53
Localisation : Besançon (25)
Date d'inscription : 20/11/2013
Re: DE RE METALLICA
+1
Devant tant de savoir, intervenir sans le "savoir" ne pourrai être considéré que futilité...
Super post très instructif...
ZR
Devant tant de savoir, intervenir sans le "savoir" ne pourrai être considéré que futilité...
Super post très instructif...

ZR
Invité- Invité
Re: DE RE METALLICA
Oui, bien sûr, que dire sinon encourager les "maîtres"......
Je pense que c'est à la fin du "cours" qu'on pose les questions non
Si on était complètement "largués" on pourrait intervenir dès maintenant bien sûr, mais "on" s'accroche et les exposés sont clairs et illustrés.....
Je pense que c'est à la fin du "cours" qu'on pose les questions non

Si on était complètement "largués" on pourrait intervenir dès maintenant bien sûr, mais "on" s'accroche et les exposés sont clairs et illustrés.....

Non nobis Domine, non nobis, sed Nomini Tuo da Gloriam.
http://winchester-lsg.forumotion.com/
http://prehistoire-xixeme.forumactif.org/
CLOSDELIF- Pilier du forum
- Nombre de messages : 22791
Age : 72
Localisation : 81
Date d'inscription : 03/09/2009
Re: DE RE METALLICA
Ah ah, petits chenapans, vous pensiez que les deux cinglés avaient décroché? Que nenni, mais la partie suivante était ardue à rendre sans passer trop vite ou se perdre dans de sombres détails. J'ai mis longtemps à la rédiger et Verchère plus longtemps encore à la réécrire entièrement
. Devant l'ampleur de nos proses conjointes, l'article sera publié en plusieurs fois. Bon courage, nous plongeons dans la modernité... vers 1850...)
Au milieu du XIXe siècle, les hauts fourneaux étaient bien au point et permettaient de produire d’importantes quantités de fonte. Mais l’affinage, qu’il soit conduit au foyer ou au four à puddler constituait encore un goulet d’étranglement, et coûtait fort cher.
C’est en cherchant à améliorer la conduite des fours à réverbère pour obtenir de l’acier en fondant ensemble du fer et de la fonte que Bessemer, un Anglais, eut l’idée d’un nouveau procédé qui portera son nom.
Le convertisseur Bessemer.
Le procédé Bessemer, présenté avant d’être complètement au point en 1856, fut introduit en France par James Jackson en 1858.
Le convertisseur permet un affinage en phase liquide. Pour cela, pendant que la fonte se décarbure, elle est maintenue en fusion : le métal reste liquide durant toute l’opération, alors que le puddlage s’opère à l’état pâteux. En effet, les composés indésirables sont brûlés dans un jet d’air sous pression injecté à travers la masse de fonte, ce qui génère une chaleur suffisante pour élever la température du bain (élévation nécessaire car le point de fusion augmente à mesure que le taux de carbone diminue). Mais il faut procéder rapidement.
Le convertisseur est une énorme cornue de métal tapissée d’un revêtement réfractaire « acide » en sable damé (silice).
Il peut basculer sur un axe central et reçoit au fond de nombreuses tuyères d’un diamètre de quelques centimètres chacune.

Coupe d'une cornue Bessemer, in "le fer, la fonte et l'acier, Dreyfus, 1875
Deux cubilots surplombent la cornue, le premier fournissant la fonte à décarburer. La cornue, préchauffée au bois ou au coke, est remplie de fonte liquide (1300°), puis redressée et une forte soufflerie envoie un jet d’air sous pression qui va traverser la masse de fonte liquide.
Le fer étant prédominant, le courant d’air l’oxyde en FeO, qui est aussitôt réduit par le silicium.
C’est donc en définitive le silicium qui brûle en premier ; et qui fournit d’ailleurs le plus de chaleur (le bain peut atteindre 1700°, afin de couler vers 1600° un métal affiné fondant à environ 1500°).
Le silicium s’oxyde en silice, qui s’unit à l’oxyde de fer et surtout à l’oxyde manganèse pour former une scorie acide, et le bec du convertisseur projette des étincelles rouges (période « des étincelles », ou « de silicothermie »).
Une fois le silicium épuisé, c’est le manganèse qui réduit l’oxyde de fer, donnant du MnO.
L’échauffement du bain permet alors au carbone de réduire le FeO en CO, qui se dégage au bec du convertisseur et y brûle en CO2 (période « de décarburation »).
La flamme diminue avec la teneur en CO et disparaît lorsque le carbone est à 0.10 %.
En s’arrêtant plus tôt on obtiendrait un acier doux, mais de teneur incertaine. En s’arrêtant trop tard, la production de FeO continue mais il n’y a plus rien pour le réduire : on gaspille du fer, et le métal obtenu est mélangé d’oxyde.
Généralement on décarbure donc au maximum raisonnable (0.10 %), pour recarburer ensuite de la valeur désirée, à l’aide d’additifs préparés séparément.
Le procédé n’élimine ni le phosphore (qui ne peut se fixer sur une scorie acide), ni le soufre. Par ailleurs, la production de FeO étant continue, celui qui est produit à la fin n’est pas réduit ; le métal en fusion contient aussi une grande quantité de gaz dissous, apportés par le soufflage (principalement oxygène, azote et hydrogène).
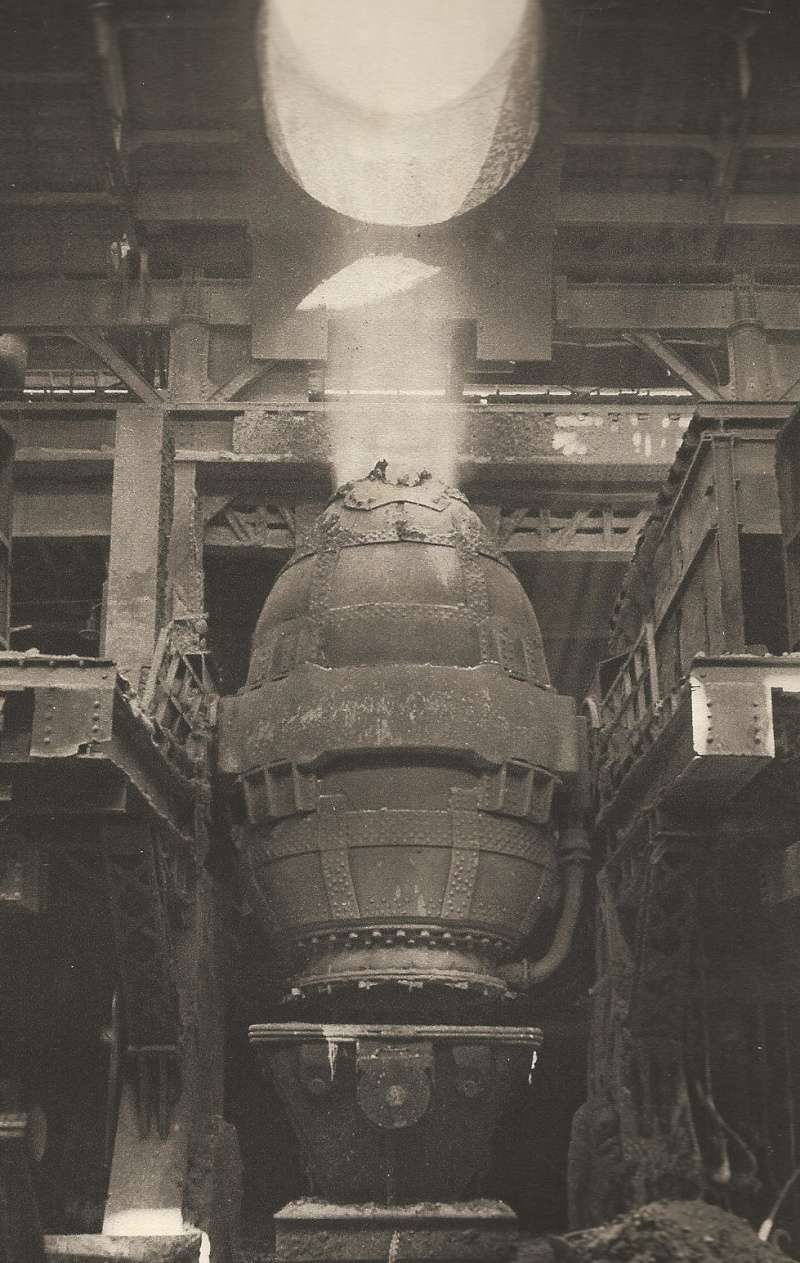
Une cornue Bessemer pendant l'affinage, période des étincelles.
Affublé de tous ces défauts, le métal serait un fer impur quasi-inutilisable !
Pour ajuster le taux de carbone et obtenir l’acier désiré, on re-bascule la cornue en position de remplissage et on verse dans le fer liquide le contenu du second cubilot : de la fonte manganésifère de haute qualité, pour environ 7 % du poids de la charge d’origine.
On obtient ainsi un mélange homogène d’acier doux fondu, immédiatement coulé en lingotière(s) par basculement complet de la cornue. Les lingots sont démoulés au plus vite pour traitement à chaud : recoupe éliminant les parties défectueuses du lingot, pilonnage afin de raffermir sa structure, et laminage pour arriver aux produits demi-finis ou finis.
Le procédé Bessemer originel ne produit que du fer ou de l’acier doux, pas d’acier dur ou allié, car l’opération doit être conduite rapidement pour éviter que le métal ne se refroidisse : réduction en 20 minutes ; 30 minutes maxi du chargement à la coulée, et coulée immédiate. Cela ne laisse pas le temps de procéder aux analyses nécessaires pour effectuer les corrections précises indispensables à l’obtention d’aciers fins.
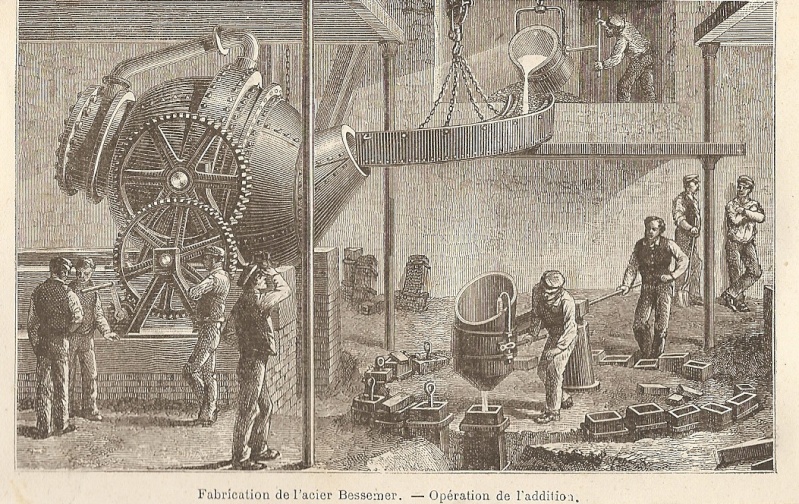
Le procédé Bessemer, l'addition, in "le fer, la fonte et l'acier", Dreyfus, 1875
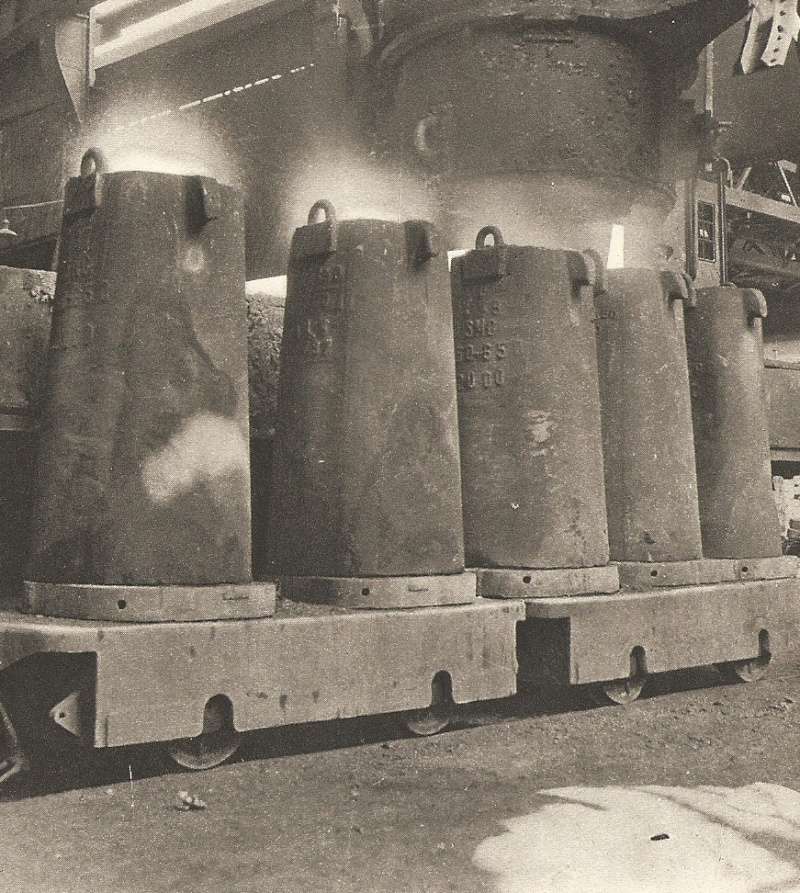
Coulée de la poche dans les lingots.
Restent cependant les problèmes du soufre, du phosphore et des gaz dissous…
Problèmes qui ont été progressivement plus ou moins résolus, au fil des perfectionnements de la technique.
Pour le soufre, présent dans la fonte issue de minerais médiocres, produite avec un mauvais charbon, ou maintes fois refondue, on a trouvé une solution satisfaisante en dé-sulfurant juste avant l’affinage. La charge initiale n’est pas coulée directement dans le convertisseur, mais d’abord dans une poche garnie de revêtement basique et contenant de la « soude Solvay » en grains (en fait, c’est du carbonate de soude CO3Na2). Les sulfures de fer et de manganèse FeS et MnS se transforment en oxydes FeO et MnO, avec production de Na2S et CO2. Avec un rapport soude / fonte de 0.5 à 1 %, on peut éliminer 25 à 50 % du soufre.
L’oxyde de fer FeO créé à la fin du soufflage serait réduit par le carbone durant le refroidissement, mais avec dégagement de CO augmentant l’effervescence du métal. En ajoutant du manganèse et/ou du silicium dans l’additif de re-carburation (fonte spéciale ou ferro-manganèse, ferro-silicium…), la réduction sera effectuée par ces corps et ne produira que du laitier fluide.
Les gaz étant 4 fois moins solubles dans le fer à basse température, ils se dégagent lors du refroidissement en provoquant parfois une forte effervescence très néfaste pour la cohésion du lingot. En vidant le convertisseur dans une poche intermédiaire, on peut « calmer » l’acier par une addition de divers produits fixant les gaz (aluminium en particulier).
Une autre solution est de couler « sous vide » dans la lingotière : en opérant dans une enceinte à faible pression atmosphérique, une bonne partie des gaz s’évacuent durant la chute.
Dans la lingotière, le métal se solidifie « en couches minces », de l’extérieur vers le centre, et du bas vers le haut. Les impûretés sont chassées vers le centre, qui reste liquide plus longtemps, puis remontent. Le haut du lingot est irrégulier, creusé (la « retassure ») et riche en impûretés ; le centre est souvent hétérogène, parfois creux.
Le lingot est donc amputé des parties les plus défectueuses, qui peuvent aller jusqu’à 25 % de son poids. Puis fortement martelé, mais le marteau-pilon ne peut corriger tous les défauts internes : les lingots creux ne seront pas acceptables pour le forgeage de pièces massives.
Quant au phosphore, qui pollue la majorité des minerais européens, il attaque rapidement le revêtement silicieux des cornues pour former des silicates mélangés au métal.
Le procédé Bessemer est donc inutilisable pour toutes les fontes phosphoreuses, et cantonné au traitement des fontes issues d’excellents minerais, plus rares et plus chers.
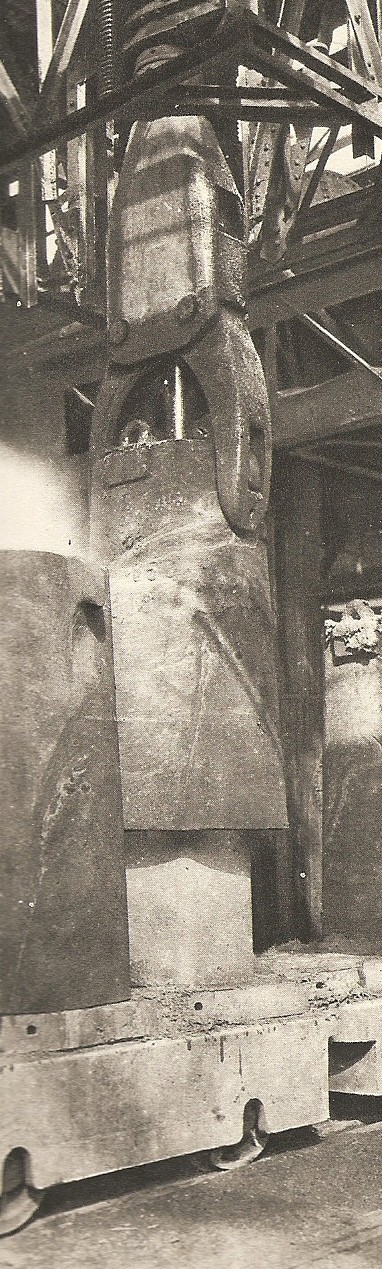
Arrachage d'un lingot
Le convertisseur Thomas, ou Thomas-Gilchrist.
Il fallut une vingtaine d’années pour trouver une solution au problème du phosphore. En 1877 apparaît le convertisseur à revêtement « basique », avec des briques à base de dolomie (mélange de chaux et de magnésie). Mais si le métal est bien déphosphoré par la combinaison du phosphore avec la chaux, le revêtement est vite endommagé. Quand on imagine de verser une grande quantité de chaux en même temps que la charge de fonte liquide, le procédé devient utilisable industriellement ; le premier convertisseur Thomas est installé au Creusot, en novembre 1879.
La réaction commence de même façon qu’au convertisseur Bessemer : le silicium (généralement à basse teneur) disparaît en premier, avec le manganèse, formant un silicate de manganèse et de fer. Puis vient le tour du carbone, qui est brûlé en totalité.
Commence alors la période « du sursoufflage » avec la combustion du phosphore, qui apporte l’essentiel de la chaleur. L’acide phosphorique ainsi produit est fixé par la chaux, formant la fameuse « scorie Thomas », un engrais excellent qui joua un grand rôle dans l’augmentation des rendements agricoles. Contrairement au convertisseur Bessemer, cette scorie doit être évacuée avant la phase finale de désoxydation, car le phosphore repartirait alors dans le bain.
Le taux de phosphore peut ainsi être abaissé à 0.05 % et la température dépassant souvent 1700 ° permet, en présence de la chaux, l’élimination de 50 %du soufre éventuel.
L’addition finale de carbone avec désoxydant (fonte manganésifère ou ferro manganèse carburé) est primordiale, puisque le procédé fait disparaître presque totalement le carbone (préalable indispensable au début de la combustion du phosphore).
(Là, il devrait y avoir une illustration d'une cornue au remplissage, mais je ne retrouve pas le document... je réserve la place
)
Le procédé Thomas fut déterminant, car il permettait de traiter les minerais médiocres formant la grande majorité des ressources. Mais l’acier Thomas restait cependant inférieur à l’acier Bessemer, à cause du phosphore résiduel et de la plus grande quantité d’azote dissous (apporté par le sursoufflage et la température plus élevée).
Diverses améliorations furent ultérieurement apportées (air sur-oxygéné, oxygène pur, oxygène chargé en poudre de chaux, etc.), afin d’amoindrir les divers défauts.
C’est donc le convertisseur Thomas qui va donner à la sidérurgie un remarquable essor, en permettant de très fortes productions d’acier correct (sans plus) à des coûts intéressants.
Le convertisseur Bessemer reste tout de même concurrentiel pour des productions de qualité un peu plus élevée ou de faible volume (1 ou 2 tonnes, volume trop réduit pour un convertisseur Thomas). Par exemple pour la fonderie d’acier (pièces en acier coulé).
Mais ces fameux convertisseurs restent cantonnés à la production en masse d’aciers ordinaires (rails de chemin de fer, poutrelles métalliques, etc.)
Les aciers de qualité restent tributaires du four à puddler, éventuellement de la cémentation. Avec refonte en creuset fermé pour uniformiser et ajuster précisément la teneur du métal (les lingots ainsi obtenus présentent moins de défauts que ceux des convertisseurs, car le métal n’est pas gazé).
À bientôt...

Au milieu du XIXe siècle, les hauts fourneaux étaient bien au point et permettaient de produire d’importantes quantités de fonte. Mais l’affinage, qu’il soit conduit au foyer ou au four à puddler constituait encore un goulet d’étranglement, et coûtait fort cher.
C’est en cherchant à améliorer la conduite des fours à réverbère pour obtenir de l’acier en fondant ensemble du fer et de la fonte que Bessemer, un Anglais, eut l’idée d’un nouveau procédé qui portera son nom.
Le convertisseur Bessemer.
Le procédé Bessemer, présenté avant d’être complètement au point en 1856, fut introduit en France par James Jackson en 1858.
Le convertisseur permet un affinage en phase liquide. Pour cela, pendant que la fonte se décarbure, elle est maintenue en fusion : le métal reste liquide durant toute l’opération, alors que le puddlage s’opère à l’état pâteux. En effet, les composés indésirables sont brûlés dans un jet d’air sous pression injecté à travers la masse de fonte, ce qui génère une chaleur suffisante pour élever la température du bain (élévation nécessaire car le point de fusion augmente à mesure que le taux de carbone diminue). Mais il faut procéder rapidement.
Le convertisseur est une énorme cornue de métal tapissée d’un revêtement réfractaire « acide » en sable damé (silice).
Il peut basculer sur un axe central et reçoit au fond de nombreuses tuyères d’un diamètre de quelques centimètres chacune.

Coupe d'une cornue Bessemer, in "le fer, la fonte et l'acier, Dreyfus, 1875
Deux cubilots surplombent la cornue, le premier fournissant la fonte à décarburer. La cornue, préchauffée au bois ou au coke, est remplie de fonte liquide (1300°), puis redressée et une forte soufflerie envoie un jet d’air sous pression qui va traverser la masse de fonte liquide.
Le fer étant prédominant, le courant d’air l’oxyde en FeO, qui est aussitôt réduit par le silicium.
C’est donc en définitive le silicium qui brûle en premier ; et qui fournit d’ailleurs le plus de chaleur (le bain peut atteindre 1700°, afin de couler vers 1600° un métal affiné fondant à environ 1500°).
Le silicium s’oxyde en silice, qui s’unit à l’oxyde de fer et surtout à l’oxyde manganèse pour former une scorie acide, et le bec du convertisseur projette des étincelles rouges (période « des étincelles », ou « de silicothermie »).
Une fois le silicium épuisé, c’est le manganèse qui réduit l’oxyde de fer, donnant du MnO.
L’échauffement du bain permet alors au carbone de réduire le FeO en CO, qui se dégage au bec du convertisseur et y brûle en CO2 (période « de décarburation »).
La flamme diminue avec la teneur en CO et disparaît lorsque le carbone est à 0.10 %.
En s’arrêtant plus tôt on obtiendrait un acier doux, mais de teneur incertaine. En s’arrêtant trop tard, la production de FeO continue mais il n’y a plus rien pour le réduire : on gaspille du fer, et le métal obtenu est mélangé d’oxyde.
Généralement on décarbure donc au maximum raisonnable (0.10 %), pour recarburer ensuite de la valeur désirée, à l’aide d’additifs préparés séparément.
Le procédé n’élimine ni le phosphore (qui ne peut se fixer sur une scorie acide), ni le soufre. Par ailleurs, la production de FeO étant continue, celui qui est produit à la fin n’est pas réduit ; le métal en fusion contient aussi une grande quantité de gaz dissous, apportés par le soufflage (principalement oxygène, azote et hydrogène).
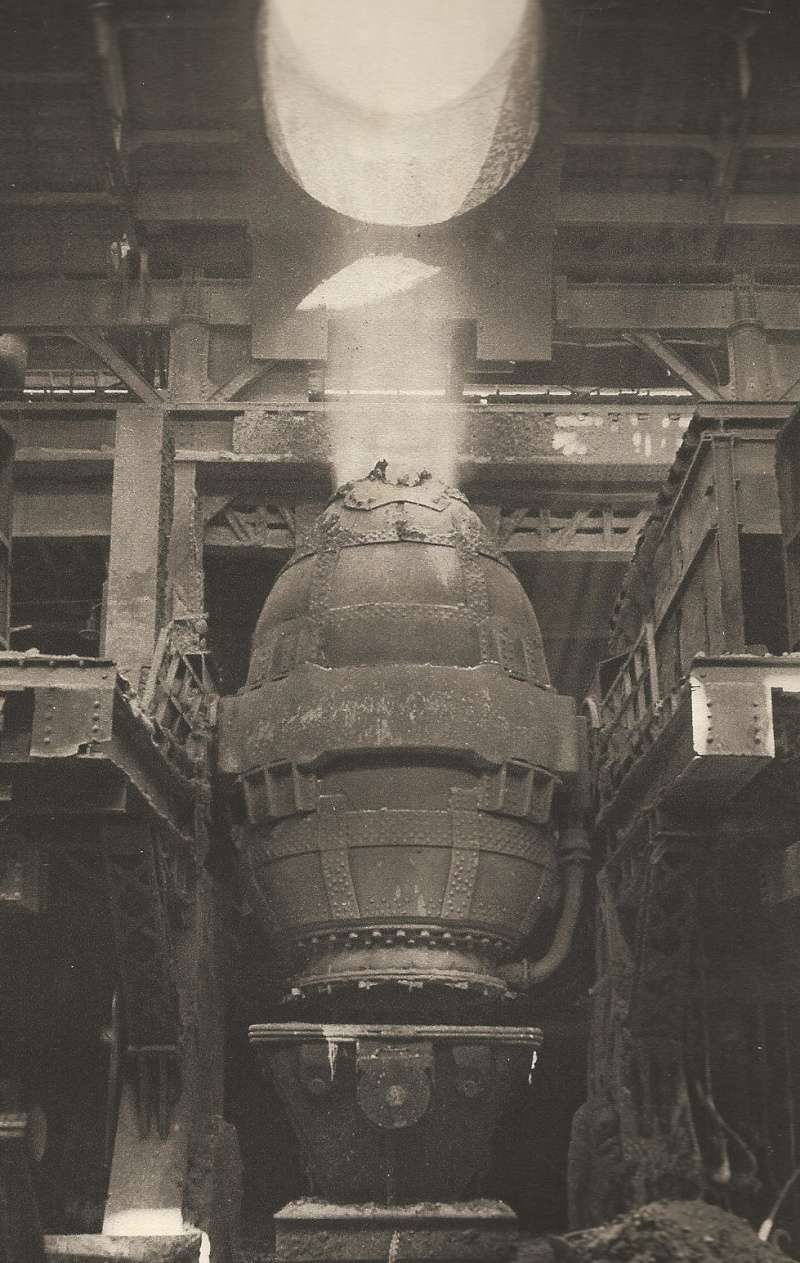
Une cornue Bessemer pendant l'affinage, période des étincelles.
Affublé de tous ces défauts, le métal serait un fer impur quasi-inutilisable !
Pour ajuster le taux de carbone et obtenir l’acier désiré, on re-bascule la cornue en position de remplissage et on verse dans le fer liquide le contenu du second cubilot : de la fonte manganésifère de haute qualité, pour environ 7 % du poids de la charge d’origine.
On obtient ainsi un mélange homogène d’acier doux fondu, immédiatement coulé en lingotière(s) par basculement complet de la cornue. Les lingots sont démoulés au plus vite pour traitement à chaud : recoupe éliminant les parties défectueuses du lingot, pilonnage afin de raffermir sa structure, et laminage pour arriver aux produits demi-finis ou finis.
Le procédé Bessemer originel ne produit que du fer ou de l’acier doux, pas d’acier dur ou allié, car l’opération doit être conduite rapidement pour éviter que le métal ne se refroidisse : réduction en 20 minutes ; 30 minutes maxi du chargement à la coulée, et coulée immédiate. Cela ne laisse pas le temps de procéder aux analyses nécessaires pour effectuer les corrections précises indispensables à l’obtention d’aciers fins.
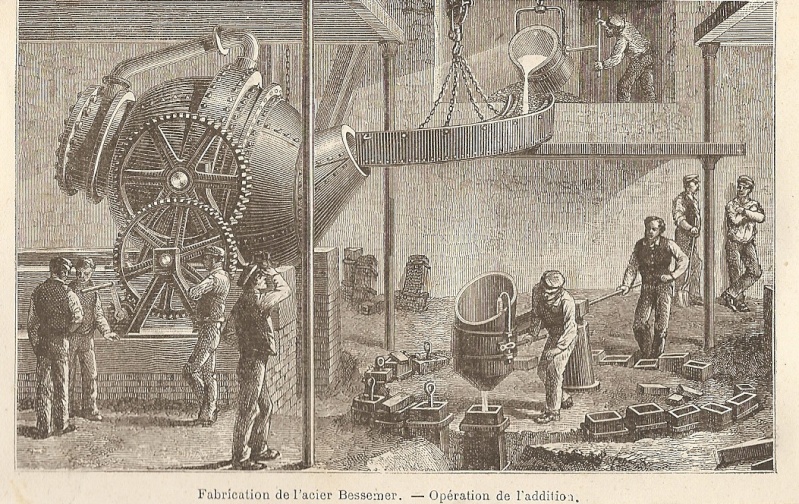
Le procédé Bessemer, l'addition, in "le fer, la fonte et l'acier", Dreyfus, 1875
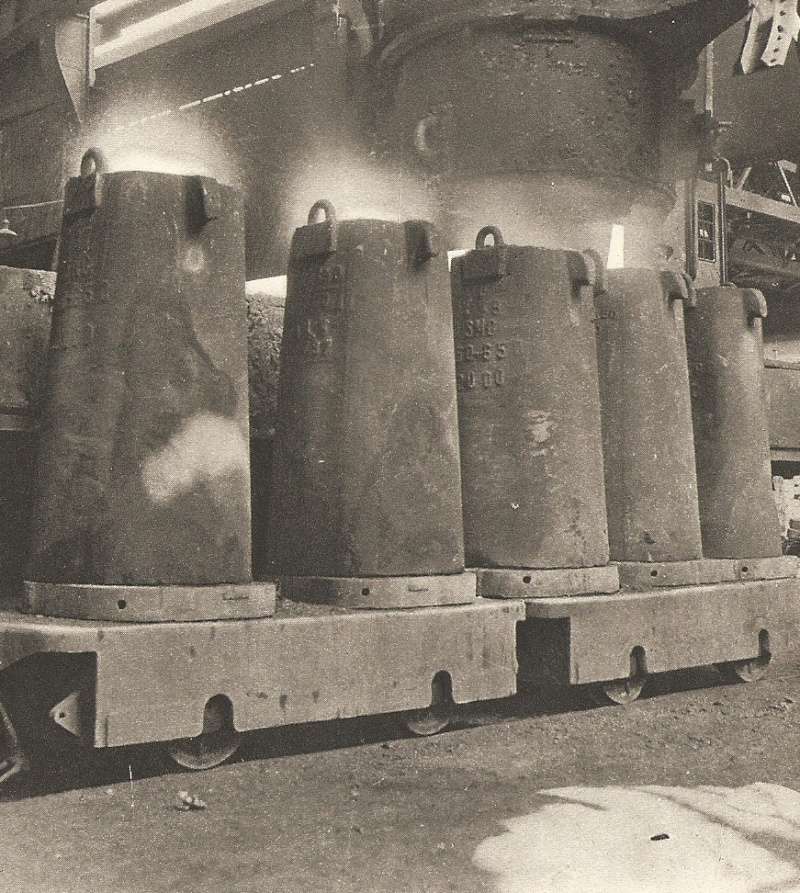
Coulée de la poche dans les lingots.
Restent cependant les problèmes du soufre, du phosphore et des gaz dissous…
Problèmes qui ont été progressivement plus ou moins résolus, au fil des perfectionnements de la technique.
Pour le soufre, présent dans la fonte issue de minerais médiocres, produite avec un mauvais charbon, ou maintes fois refondue, on a trouvé une solution satisfaisante en dé-sulfurant juste avant l’affinage. La charge initiale n’est pas coulée directement dans le convertisseur, mais d’abord dans une poche garnie de revêtement basique et contenant de la « soude Solvay » en grains (en fait, c’est du carbonate de soude CO3Na2). Les sulfures de fer et de manganèse FeS et MnS se transforment en oxydes FeO et MnO, avec production de Na2S et CO2. Avec un rapport soude / fonte de 0.5 à 1 %, on peut éliminer 25 à 50 % du soufre.
L’oxyde de fer FeO créé à la fin du soufflage serait réduit par le carbone durant le refroidissement, mais avec dégagement de CO augmentant l’effervescence du métal. En ajoutant du manganèse et/ou du silicium dans l’additif de re-carburation (fonte spéciale ou ferro-manganèse, ferro-silicium…), la réduction sera effectuée par ces corps et ne produira que du laitier fluide.
Les gaz étant 4 fois moins solubles dans le fer à basse température, ils se dégagent lors du refroidissement en provoquant parfois une forte effervescence très néfaste pour la cohésion du lingot. En vidant le convertisseur dans une poche intermédiaire, on peut « calmer » l’acier par une addition de divers produits fixant les gaz (aluminium en particulier).
Une autre solution est de couler « sous vide » dans la lingotière : en opérant dans une enceinte à faible pression atmosphérique, une bonne partie des gaz s’évacuent durant la chute.
Dans la lingotière, le métal se solidifie « en couches minces », de l’extérieur vers le centre, et du bas vers le haut. Les impûretés sont chassées vers le centre, qui reste liquide plus longtemps, puis remontent. Le haut du lingot est irrégulier, creusé (la « retassure ») et riche en impûretés ; le centre est souvent hétérogène, parfois creux.
Le lingot est donc amputé des parties les plus défectueuses, qui peuvent aller jusqu’à 25 % de son poids. Puis fortement martelé, mais le marteau-pilon ne peut corriger tous les défauts internes : les lingots creux ne seront pas acceptables pour le forgeage de pièces massives.
Quant au phosphore, qui pollue la majorité des minerais européens, il attaque rapidement le revêtement silicieux des cornues pour former des silicates mélangés au métal.
Le procédé Bessemer est donc inutilisable pour toutes les fontes phosphoreuses, et cantonné au traitement des fontes issues d’excellents minerais, plus rares et plus chers.
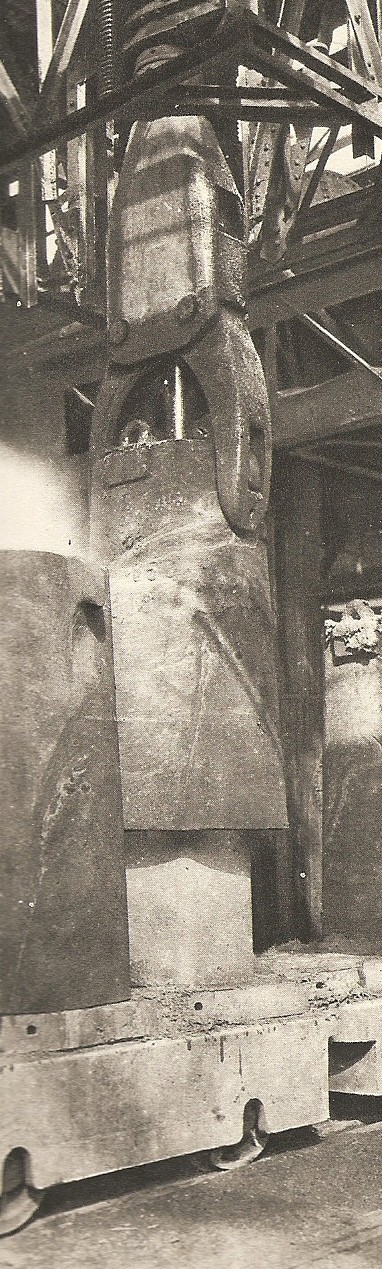
Arrachage d'un lingot
Le convertisseur Thomas, ou Thomas-Gilchrist.
Il fallut une vingtaine d’années pour trouver une solution au problème du phosphore. En 1877 apparaît le convertisseur à revêtement « basique », avec des briques à base de dolomie (mélange de chaux et de magnésie). Mais si le métal est bien déphosphoré par la combinaison du phosphore avec la chaux, le revêtement est vite endommagé. Quand on imagine de verser une grande quantité de chaux en même temps que la charge de fonte liquide, le procédé devient utilisable industriellement ; le premier convertisseur Thomas est installé au Creusot, en novembre 1879.
La réaction commence de même façon qu’au convertisseur Bessemer : le silicium (généralement à basse teneur) disparaît en premier, avec le manganèse, formant un silicate de manganèse et de fer. Puis vient le tour du carbone, qui est brûlé en totalité.
Commence alors la période « du sursoufflage » avec la combustion du phosphore, qui apporte l’essentiel de la chaleur. L’acide phosphorique ainsi produit est fixé par la chaux, formant la fameuse « scorie Thomas », un engrais excellent qui joua un grand rôle dans l’augmentation des rendements agricoles. Contrairement au convertisseur Bessemer, cette scorie doit être évacuée avant la phase finale de désoxydation, car le phosphore repartirait alors dans le bain.
Le taux de phosphore peut ainsi être abaissé à 0.05 % et la température dépassant souvent 1700 ° permet, en présence de la chaux, l’élimination de 50 %du soufre éventuel.
L’addition finale de carbone avec désoxydant (fonte manganésifère ou ferro manganèse carburé) est primordiale, puisque le procédé fait disparaître presque totalement le carbone (préalable indispensable au début de la combustion du phosphore).
(Là, il devrait y avoir une illustration d'une cornue au remplissage, mais je ne retrouve pas le document... je réserve la place

Le procédé Thomas fut déterminant, car il permettait de traiter les minerais médiocres formant la grande majorité des ressources. Mais l’acier Thomas restait cependant inférieur à l’acier Bessemer, à cause du phosphore résiduel et de la plus grande quantité d’azote dissous (apporté par le sursoufflage et la température plus élevée).
Diverses améliorations furent ultérieurement apportées (air sur-oxygéné, oxygène pur, oxygène chargé en poudre de chaux, etc.), afin d’amoindrir les divers défauts.
C’est donc le convertisseur Thomas qui va donner à la sidérurgie un remarquable essor, en permettant de très fortes productions d’acier correct (sans plus) à des coûts intéressants.
Le convertisseur Bessemer reste tout de même concurrentiel pour des productions de qualité un peu plus élevée ou de faible volume (1 ou 2 tonnes, volume trop réduit pour un convertisseur Thomas). Par exemple pour la fonderie d’acier (pièces en acier coulé).
Mais ces fameux convertisseurs restent cantonnés à la production en masse d’aciers ordinaires (rails de chemin de fer, poutrelles métalliques, etc.)
Les aciers de qualité restent tributaires du four à puddler, éventuellement de la cémentation. Avec refonte en creuset fermé pour uniformiser et ajuster précisément la teneur du métal (les lingots ainsi obtenus présentent moins de défauts que ceux des convertisseurs, car le métal n’est pas gazé).
À bientôt...

freebird- Pilier du forum
- Nombre de messages : 1765
Age : 56
Localisation : Lot 46
Date d'inscription : 28/12/2013
Re: DE RE METALLICA
Freebird :chinese:
Tu es un coureur de marathon et le fil de ce sujet passionnant, il vient en corollaire des possibilités d'évolution de nos belles armes.
Que Vulcain bénisse ta journée.
Tu es un coureur de marathon et le fil de ce sujet passionnant, il vient en corollaire des possibilités d'évolution de nos belles armes.
Que Vulcain bénisse ta journée.
fcrozet- Pilier du forum
- Nombre de messages : 4115
Age : 66
Date d'inscription : 20/02/2012
Re: DE RE METALLICA
Pour ma part, j'imprime, je relie et je relis. Merci pour votre travail formidable (en plus d'un sens).
Invité- Invité
Re: DE RE METALLICA
......et je transmets à mon frangin forgeron sans copyright 

fcrozet- Pilier du forum
- Nombre de messages : 4115
Age : 66
Date d'inscription : 20/02/2012
Page 2 sur 4 • 1, 2, 3, 4
Page 2 sur 4
Permission de ce forum:
Vous ne pouvez pas répondre aux sujets dans ce forum